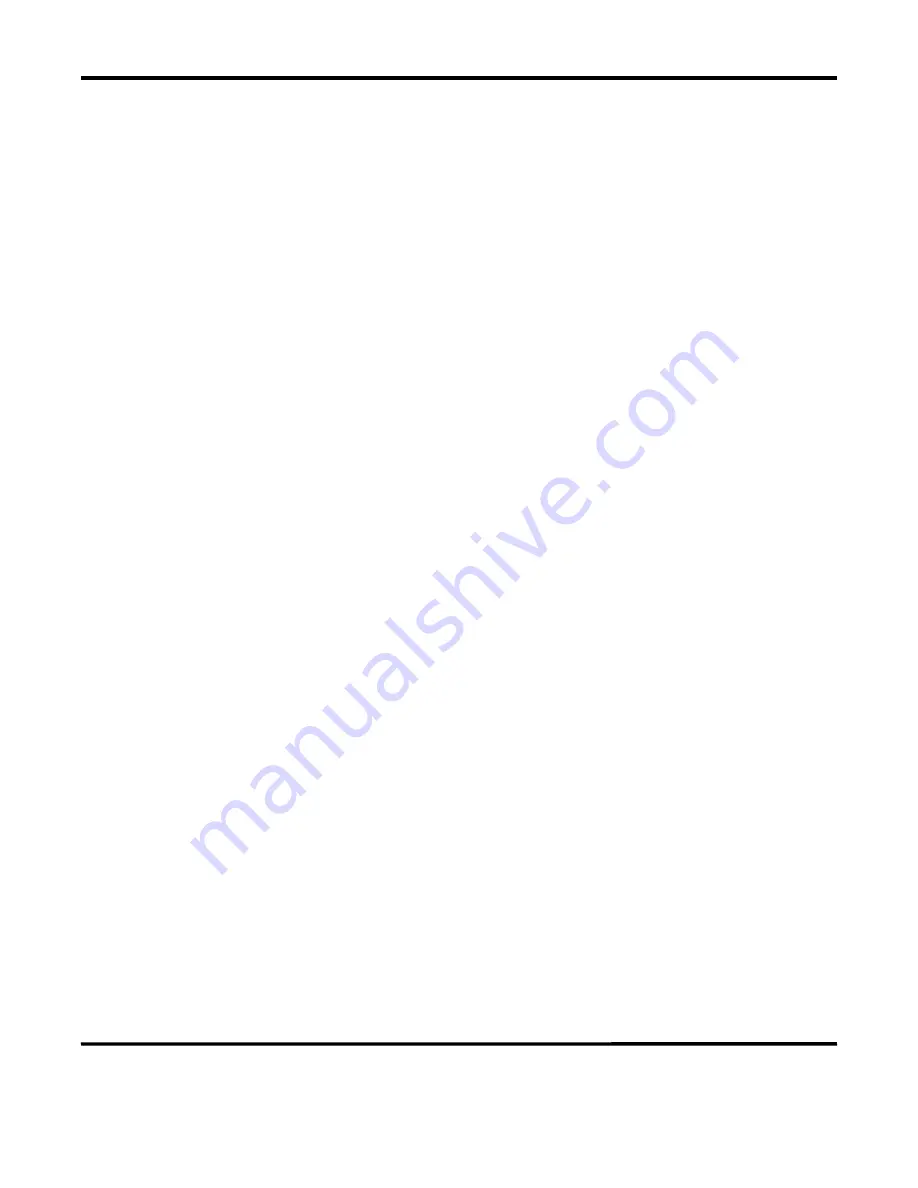
APPENDIX F: DEFINING THE OPTIMUM PROCESS
CD-A DUAL PULSE RESISTANCE WELDING POWER SUPPLY
990-430
F-5
R1 & R7
The electrode resistances affect the conduction of energy and weld heat to the parts and
the rate of heat sinking from the parts at the end of the weld.
R2, R4 & R 6
The electrode-to-part and part-to-part “Contact Resistances” determine the amount of
heat generation in these areas. The contact resistances decline over time as the parts
achieve better fit up.
R3 & R5
The metal “Bulk Resistances” become higher during the weld as the parts are heated.
If a weld is initiated when the contact resistances are still high, the heat generated is in relation to the level
and location of the contact resistances, as the materials have not had a chance to fit up correctly. It is
common for the heat generated at the electrode-to-part and part-to-part resistances to cause multiple
welding problems when welding resistive materials including:
•
Part marking and surface heating
•
Weld splash or expulsion
•
Electrode sticking
•
Weak welds
Alternately, conductive materials can be welded by using high contact resistance and fast heating because
their bulk resistance is not high and cannot be relied upon for heat generation.
If a weld is initiated when both parts and electrodes are fitted up correctly, the contact resistance is lower
and bulk resistance now controls the heat generation. This type of weld is achieved with a slower heating
rate and normally longer time is preferred for welding resistive materials, which can generate heat through
their bulk resistance.
The contact resistances present at the weld when the power supply is fired have a great impact on the heat
balance of a weld and, therefore, the heat affected zone.