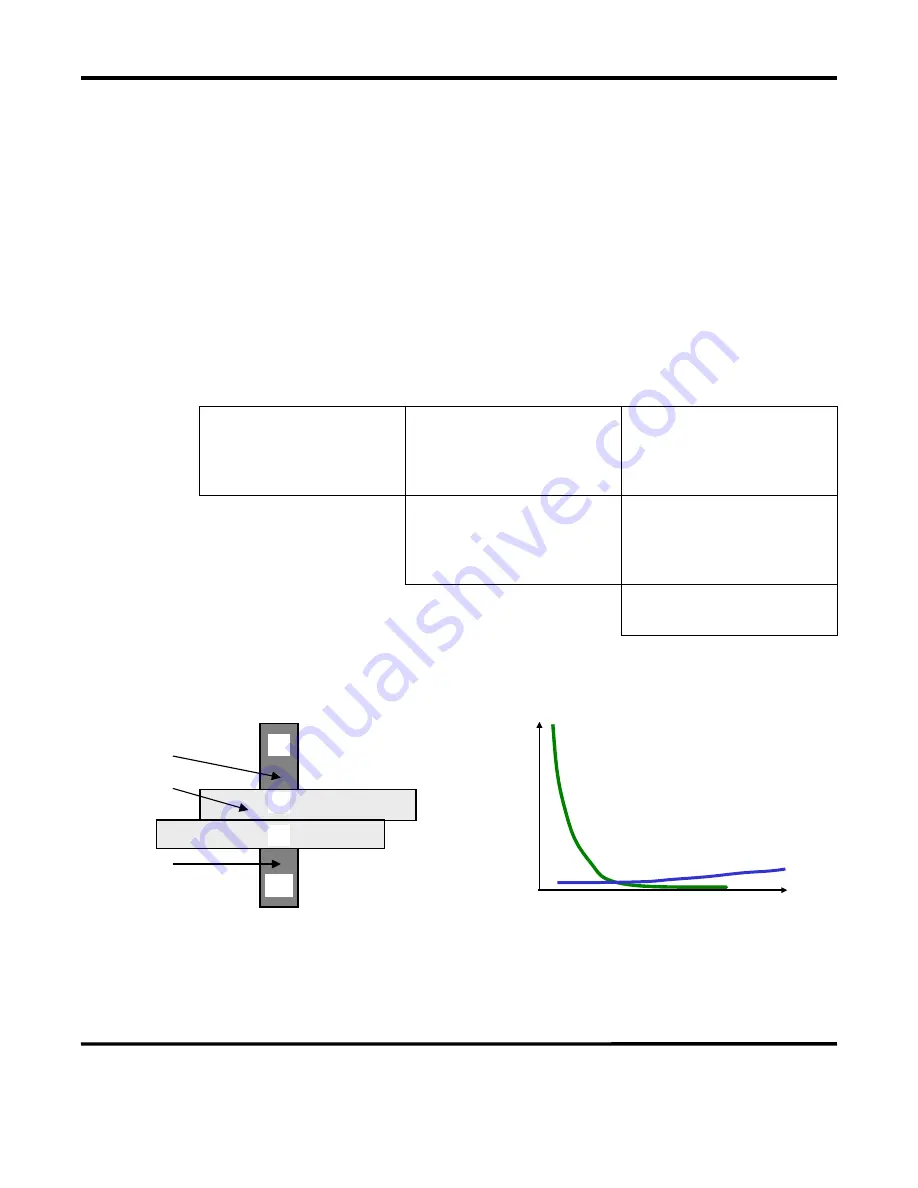
APPENDIX F: DEFINING THE OPTIMUM PROCESS
CD-A DUAL PULSE RESISTANCE WELDING POWER SUPPLY
F-4
990-430
•
Group II – Resistive Metals
It is easier to generate and trap heat at the interface of resistive metals and therefore it is possible
to form both solid state and fusion welds depending on time and temperature. Upslope can reduce
contact resistances and provide heating in the bulk material resistance.
•
Group III – Refractory Metals
Refractory metals have very high melting points and excess heating can cause micro-structural
damage. A solid-state joint is therefore preferred.
The chart below gives some guidance on the type of joint that can be expected and design considerations
required when joining materials from the different groups.
Group I
Group II
Group III
Group I
(Copper)
•
Solid-State
•
W/Mo electrodes
•
Solid-State
•
Projection on Group I
•
Solid-State
•
Fine projections on
Group III
Group II
(Steel)
•
Solid-State or Fusion
•
Solid-state or braze of II
on III
•
Projection on III
Group III
(Moly)
•
Solid-State
Basic Principles
The figure above shows the key resistances in a typical opposed resistance weld and the relationship
between contact resistances and bulk resistances over time, during a typical resistance weld:
R1
R7
R3
R5
R2
R4
R6
Time
Contact Resistance
Bulk Resistance
Resistance