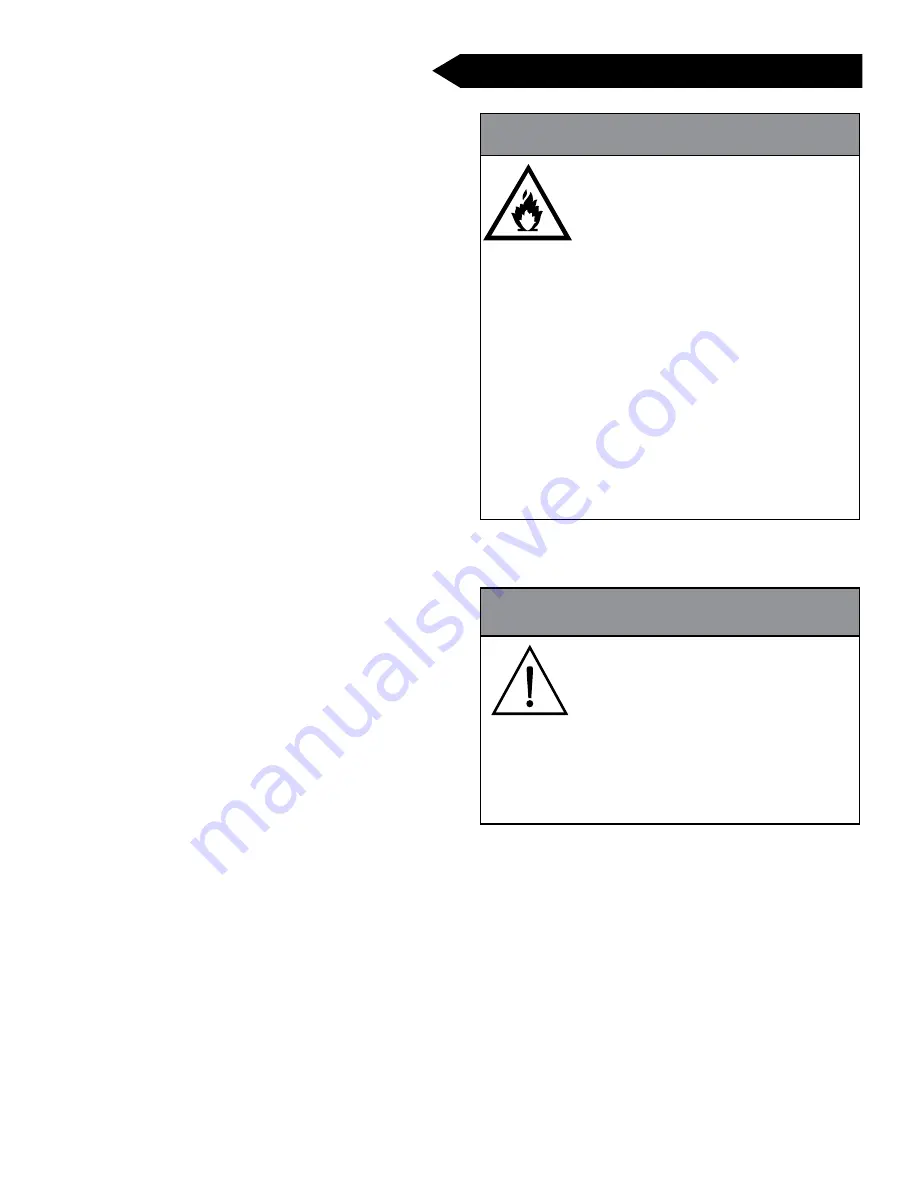
MN-36580 (Rev. 2) 01/16 • Quickchillers • 3
•
To prevent serious injury, death or property
damage, your appliance should be inspected and
serviced at least every twelve (12) months by an
authorized service partner or trained technician.
•
ONLY allow an authorized service partner or
trained technician to service or to repair your
appliance. Installation or repairs that are not
performed by an authorized service partner or
trained technician, or the use of non-factory
authorized parts will void the warranty and relieve
Alto-Shaam of all liability.
•
When working on this appliance, observe
precautions in the literature, on tags, on labels
attached to or shipped with the appliance and other
safety precautions that may apply.
•
If the appliance is installed on casters freedom of
movement of the appliance must be restricted so
that utility connections (including gas, water, and
electricity) cannot be damaged when the unit is
moved. If the appliance is moved, make sure that all
utility connections are properly disconnected. If the
unit is returned to its original position, make sure
that any retention devices and utility connections
are properly connected.
•
ONLY use the appliance when it is stationary.
Mobile oven racks, mobile plate racks, transport
trolleys, and appliances on casters can tip over
when being moved over an uneven floor or
threshold and cause serious injury.
•
ALWAYS apply caster brakes on mobile appliances
or accessories when these are not being moved.
These items could move or roll on uneven floors
and cause property damage or serious injury.
•
Be extremely careful when moving appliances
because the food trays may contain hot fluids that
may spill, causing serious injury.
•
ALWAYS open the appliance door very slowly.
Escaping hot vapors or steam can cause serious
injury or death.
aDDItIonal safety proceDures
anD precautIons
•
If your gas appliance is installed under an
exhaust hood, the hood must be switched ON
when the oven is in use to avoid the build up of
combustion gases. Failure to do so may result in
serious injury, death or property damage.
•
NEVER place objects near the oven exhaust vents.
This area is hot and could be a potential ignition
source for a fire.
•
Do not allow objects to block or obstruct the area
below the oven base. This may result in fire,
damage to the equipment or serious injury.
•
Do not use the attached hand-held hose to spray
anything other than the interior of the oven
compartment.
•
Do not use the attached hand-held hose on the
surface of a hot cooking compartment. The
sudden temperature change can damage the oven
interior. Allow the oven to cool to a minimum of
150°F (66°C). Failure to observe this precaution
can void the warranty.
W a r n I n g
To prevent SERIOUS INJURY,
DEATH, or PROPERTY DAMAGE:
The appliance must be cleaned
thoroughly to avoid deposits of
grease and or food residues inside
the appliance that may catch fi re. If
fat deposits and/or food waste inside
the appliance ignite, shut down the
appliance immediately and keep the
appliance door closed to extinguish
the fi re. If further extinguishing is
required, disconnect the appliance
from the main power and use a fi re
extinguisher (do not use water to
extinguish a grease fi re!). Failure
to clean the appliance properly
invalidates the warranty and relieves
Alto-Shaam of all liability.
WarnIng
This appliance is not intended for use
by persons (including children) with
reduced physical, sensory or mental
capabilities, or lack of experience and
knowledge, unless they have been
given supervision concerning use of
the appliance by person responsible for
their safety.
Children should be supervised to ensure
that they do not play with the appliance.