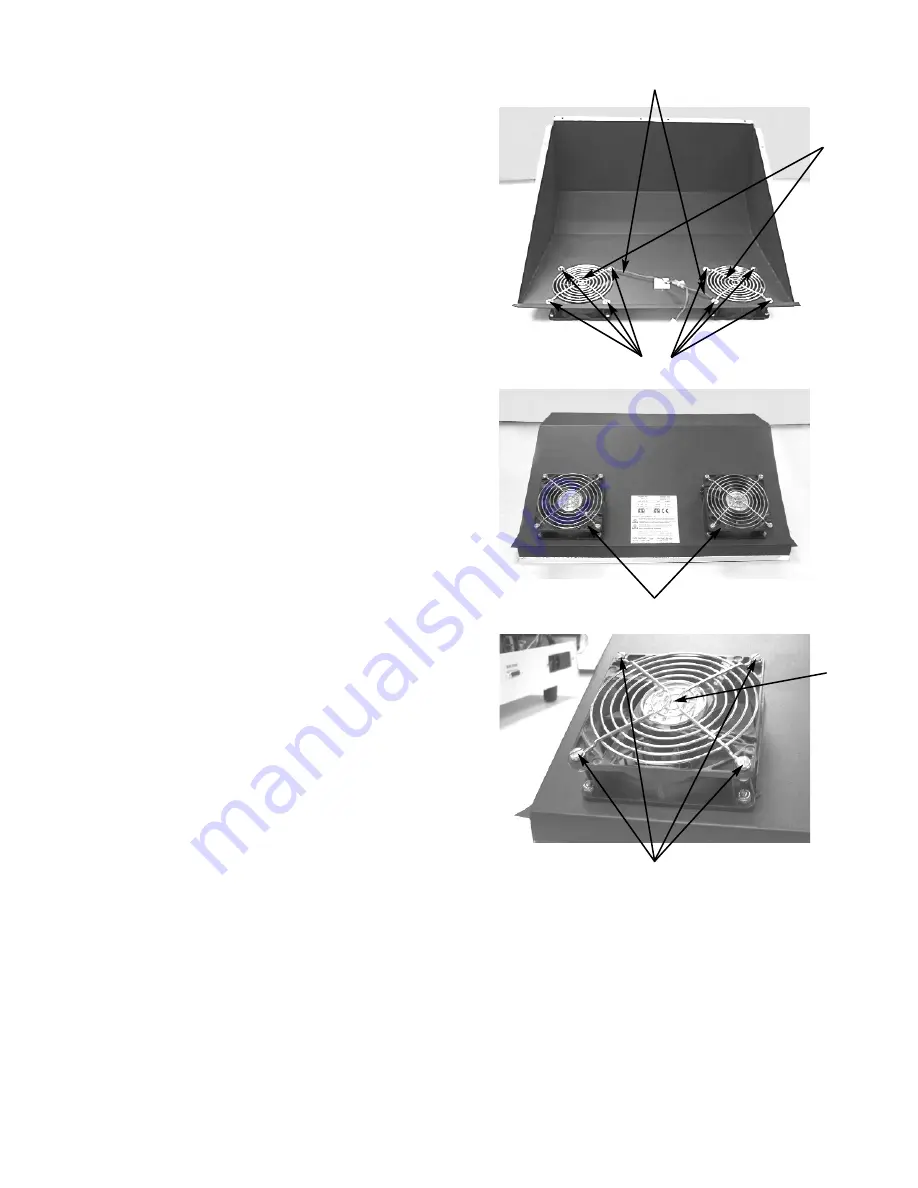
4CP121 Rev0
(4C35/3905 Service Manual)
Page 2 of 4
6. Mount replacement fans with the flow
arrow pointing to the outside of the cover.
Orient the fans so that the wires (H) are
located as shown and align with the holes
provided on the cover.
7. Reassemble the instrument by reversing
steps 1-5.
C
D
E
G
F
H
Summary of Contents for 3900
Page 1: ...3905SM Rev14 050415 The Advanced Osmometer Model 3900 Service Manual ...
Page 2: ......
Page 5: ...1 Introduction ...
Page 6: ......
Page 13: ...2 General Overview ...
Page 14: ......
Page 15: ...The Advanced Model 3900 Service Manual 15 Circuit Diagram ...
Page 20: ...20 The Advanced Model 3900 Service Manual Notes ...
Page 21: ...3 Maintenance ...
Page 22: ......
Page 25: ...4 Troubleshooting ...
Page 26: ......
Page 36: ...36 The Advanced Model 3900 Service Manual Notes ...
Page 37: ...5 Adjustments ...
Page 38: ......
Page 41: ...6 Replacement Instructions ...
Page 42: ......
Page 44: ......
Page 46: ......
Page 50: ......
Page 54: ......
Page 68: ......
Page 74: ......
Page 84: ......
Page 100: ......
Page 104: ......
Page 113: ...4CP450 Rev1 4C35 3905 Service Manual Page 3 of 3 E J12 J3 J11 J13 ...
Page 114: ......
Page 118: ......
Page 130: ......
Page 138: ......
Page 148: ......
Page 152: ......
Page 154: ...4CP446 Rev0 4C35 3905 Service Manual Page 2 of 2 C D E ...
Page 159: ...7 Schematics ...
Page 160: ......
Page 162: ......
Page 169: ...Appendix A Symbol Definitions ...
Page 170: ......
Page 173: ...Appendix B Product Disposal and Recycling ...
Page 174: ......
Page 176: ...The Advanced Model 3900 Service Manual Notes ...
Page 177: ...Appendix C Service Log ...
Page 178: ......
Page 180: ...Symptoms or Problems Repairs Replacements or Changes Serviced by ...
Page 181: ...Index ...
Page 182: ......