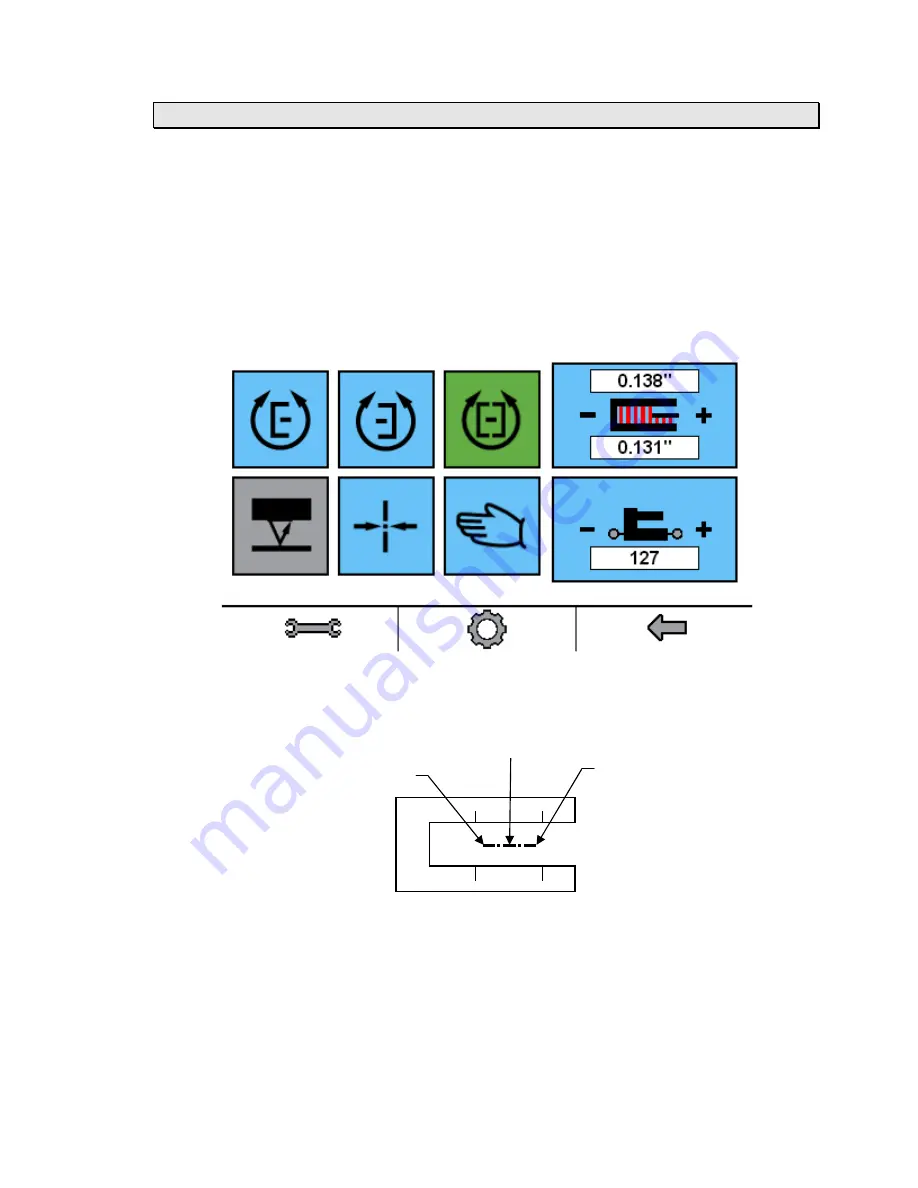
EVO 150 Controller
41
Appendix 3 / Centerline Guiding with One Detector
The Centerline Guiding with One Detector feature allows for centerline guiding within the area of
detection of one edge detector, as well as, either edge of the web within the edge detector. This
feature can be used for applications that do not allow for standard centerline guiding with two
edge detectors.
To select Centerline Guiding with One Detector, set parameter 98 to a value of 1. Centerline
Guiding with One Detector can also be selected over the fieldbus interface, see page 103.
When using a web browser to operate the EVO 150 select the applicable edge detector to begin
guiding.
Edge Detector A
Edge A
Edge B
C/L
Summary of Contents for EVO 150
Page 1: ...P O Box 7816 Madison Wisconsin 53707 7816 Instruction Manual EVO 150 Web Guide Control System...
Page 2: ......
Page 6: ...EVO 150 Controller 4 EVO 150TM Web Guide Control System...
Page 56: ...PointSource and WideArray Edge Detectors 54 PointSource and WideArray Edge Detectors...
Page 62: ...AccuBeam 3 Digital Line Guide Sensor 60 AccuBeam 3 Digital Line Guide Sensor...
Page 85: ...AccuWeb Linear Actuators 83 AccuWeb Linear Actuators...
Page 90: ...Remote Station Guide Point Adjust 88 Remote Station Guide Point Adjust...
Page 99: ...Remote Station Auxiliary 97 Remote Station Auxiliary...
Page 104: ...Fieldbus Interface 102 Fieldbus Interface...
Page 124: ......
Page 125: ......
Page 126: ......
Page 127: ......
Page 128: ......
Page 129: ......
Page 130: ......
Page 131: ......
Page 132: ......
Page 133: ......
Page 134: ......
Page 135: ......
Page 136: ......
Page 137: ...NOTES...