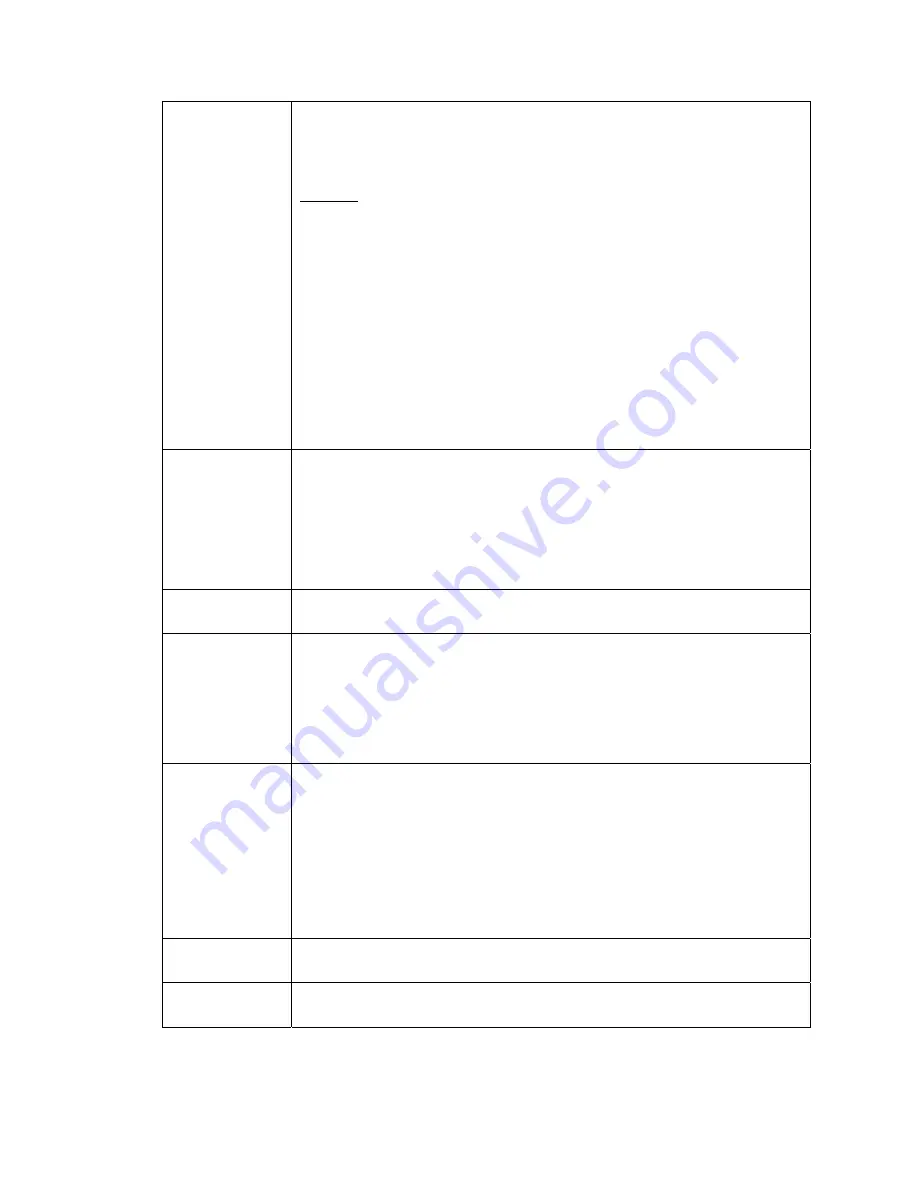
EVO 150 Controller
13
5
New software was installed during routine maintenance.
or
Non-volatile memory contains invalid data or has malfunctioned.
DO NOT perform these steps unless you are qualified personal.
Reset all parameters to their default values:
Caution:
This procedure will erase all previously entered parameter
settings! Be sure to record all current settings on page 37 before
performing this step. If you are installing new software, then you must
record the current settings
before
installing the new software.
1. Turn the DC power
off
.
2. Press and hold the S1 button.
3. Turn the DC power
on
.
4. When the LED near S1 turns from Red to Green, release the EXIT
button.
5. Set parameter 2 (end-of-travel mode) and other parameters to their
previous values. Refer to page 21 for more information about setting
controller parameters.
6
Sensor polarity is wrong.
The value of parameter 3 or 4 must be changed
for the selected sensor. Refer to page 21 for more information about setting
controller parameters.
Sensor Polarity can also be changed by simultaneously holding down the
MANUAL button and the EDGE A (or EDGE B) button on the switch pad for
5 seconds. The Manual LED will go out and the EDGE A (or EDGE B) LED
will blink indicating the polarity change.
7
Servo gain is too high.
Decrease the value of parameter 5. Refer to page
21 for more information about setting controller parameters.
8
End play in the actuator or mounting.
Press the MANUAL button and
then press IN and OUT buttons several times. Actuator operation should be
smooth and free, without binding. Firmly grasp the web guide mechanism
moving part and push and pull to check for end play. Observe the actuator,
mechanical components, and mounting hardware. There should be no
observable motion in the mechanical system. If motion is noted, repair the
web guide or actuator as required, or return the equipment for repair.
9
Sensor in wrong position.
Unwind stand:
The sensor should be located down-web, close to the last
shifting idler roll. Refer to the guide application drawings on page 121.
Winder stand:
The sensor should be located up-web before the last fixed
idler roll, one to two web widths from the shifting base. Refer to the guide
application drawings on page 121.
Intermediate guides:
The sensor should be placed close to the exiting
idler roll. Refer to the guide application drawings on page 121.
10
Excessive chuck wobble.
Decrease the web speed or re-chuck the roll of
material.
11
Web tension is low or tension control varies.
Increase the web tension
or repair the tension control.
Summary of Contents for EVO 150
Page 1: ...P O Box 7816 Madison Wisconsin 53707 7816 Instruction Manual EVO 150 Web Guide Control System...
Page 2: ......
Page 6: ...EVO 150 Controller 4 EVO 150TM Web Guide Control System...
Page 56: ...PointSource and WideArray Edge Detectors 54 PointSource and WideArray Edge Detectors...
Page 62: ...AccuBeam 3 Digital Line Guide Sensor 60 AccuBeam 3 Digital Line Guide Sensor...
Page 85: ...AccuWeb Linear Actuators 83 AccuWeb Linear Actuators...
Page 90: ...Remote Station Guide Point Adjust 88 Remote Station Guide Point Adjust...
Page 99: ...Remote Station Auxiliary 97 Remote Station Auxiliary...
Page 104: ...Fieldbus Interface 102 Fieldbus Interface...
Page 124: ......
Page 125: ......
Page 126: ......
Page 127: ......
Page 128: ......
Page 129: ......
Page 130: ......
Page 131: ......
Page 132: ......
Page 133: ......
Page 134: ......
Page 135: ......
Page 136: ......
Page 137: ...NOTES...