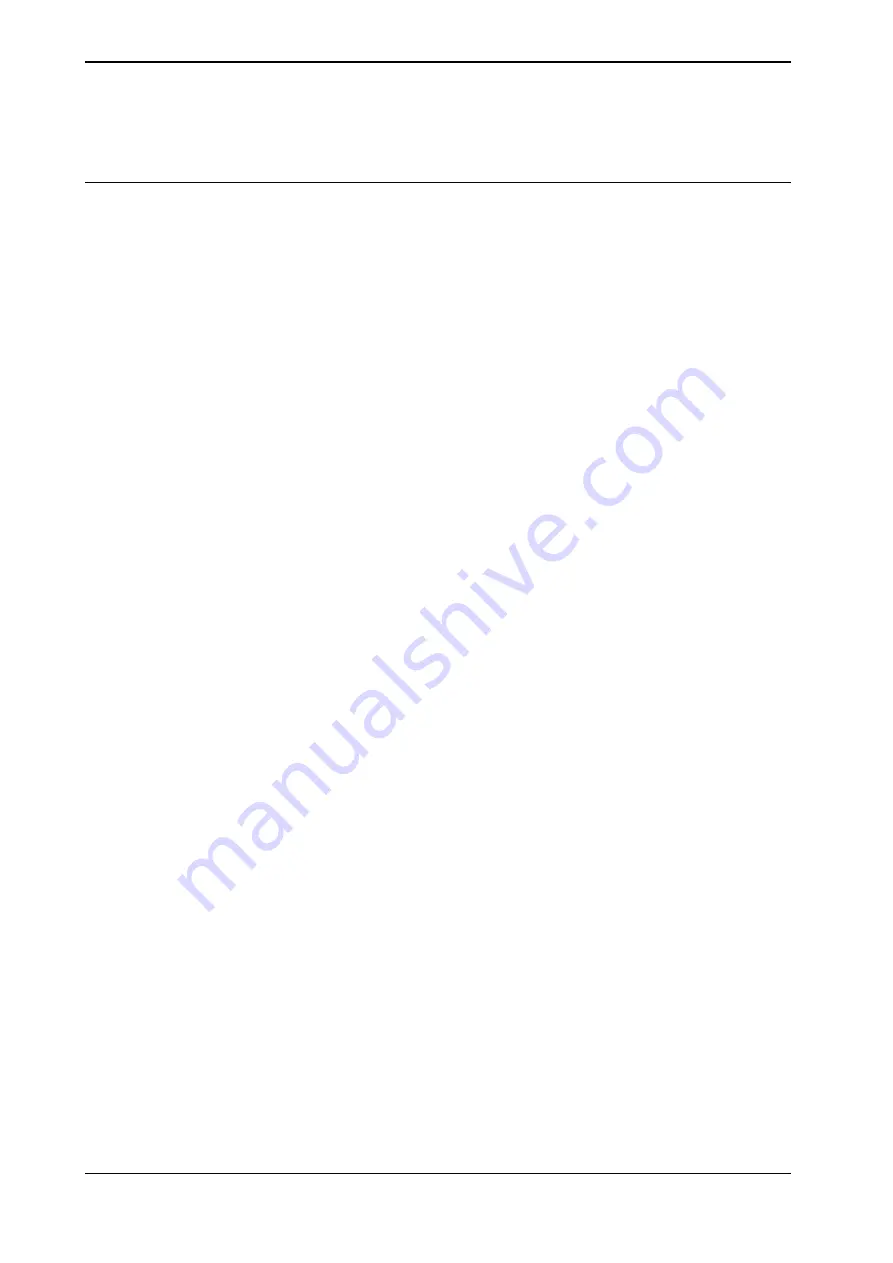
2 The position of each axis is displayed in the
Position Information
section.
Position format
The position can be displayed in different formats using the Jog application. To
configure the position formats, in the
Position Information
section, tap
Position
Format
.
The
Position Format
can be displayed relative to the following frames:
•
World
•
Base
•
Workobject
Enable the
Display Orientation Values
option to configure the Orientation fomats.
The
Orientation format
can be set to:
•
Quaternion
•
Euler angles
The
Presentation angle unit
can be set to:
•
Degrees
•
Radians
84
Operating manual - OmniCore
3HAC065036-001 Revision: J
© Copyright 2019-2021 ABB. All rights reserved.
5 Jogging
5.4 Reading the exact position
Continued
Summary of Contents for OmniCore
Page 1: ...ROBOTICS Operating manual OmniCore ...
Page 8: ...This page is intentionally left blank ...
Page 24: ...This page is intentionally left blank ...
Page 62: ...This page is intentionally left blank ...
Page 72: ...This page is intentionally left blank ...
Page 98: ...This page is intentionally left blank ...
Page 234: ...This page is intentionally left blank ...
Page 242: ...This page is intentionally left blank ...
Page 264: ......
Page 265: ......