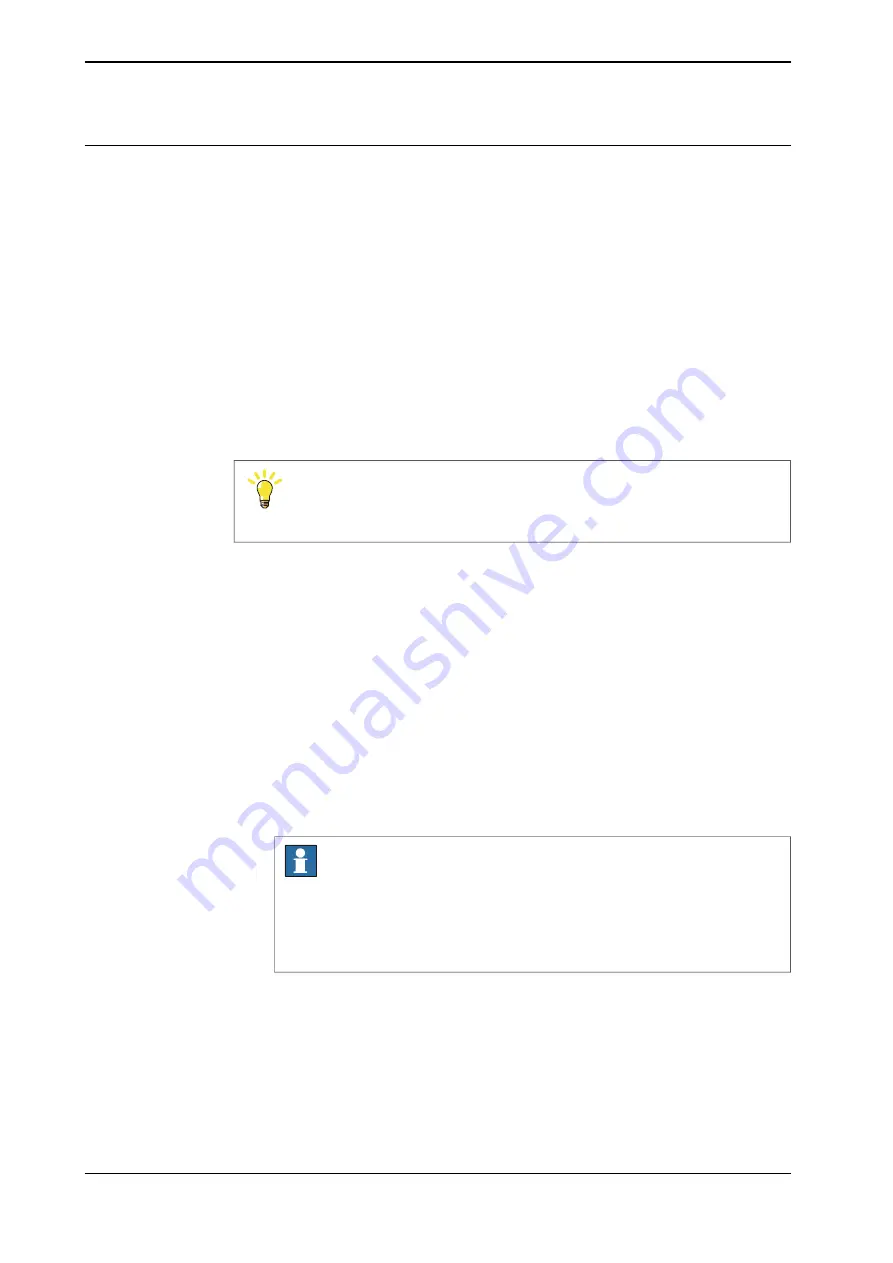
Running LoadIdentify with ModalPayLoadMode deactivated
When the system parameter ModalPayLoadMode is deactivated, set to 0,
LoadIdentify will identify the tool load and the total load. It is no longer possible to
define the payload.
With ModalPayLoadMode deactivated it is possible to use the
\TLoad
argument
in movement instructions. The
\TLoad
argument describes the total load used in
the movement. The total load is the tool load together with the payload that the
tool is carrying. If the
\TLoad
argument is used, then the
loaddata
in the current
tooldata
is not considered. For more information about ModalPayLoadMode in
movement instructions, see the section MoveL in
Technical reference
manual - RAPID Instructions, Functions and Data types
.
To start the load identification service routine you must have an active program in
manual mode and the tool and payload that you want to identify must be defined
and active in the
Jogging
window.
Tip
Always run load identification with cold motors (no warm-up).
1 On the start screen, tap
Operate
, and then select
Service Routines
from the
menu.
2 Tap LoadIdentify.
3 Press the three-position enabling device.
4 In the
Control Panel
tap
Play
. You can also press the
START
hard button
on the FlexPendant.
The
Load Identification
operator message window is displayed.
5 Tap
OK
to confirm that current path will be cleared and that the program
pointer will be lost.
6 In the operator message window, tap
Tool
or
PayLoad
.
7 Tap
OK
to confirm that the correct tool or payload is active in the jogging
menu and that the tool or payload is correctly mounted.
Note
If it is not correct, release the three-position enabling device and select
the correct tool/payload in the
Jogging
menu. Then return to LoadIdentify,
press the three-position enabling device, and press Start. Tap
Retry
and
confirm that the new tool/payload is correct.
8 When identifying tool loads, confirm that the tool is active.
9 Select the identification method. If you select the method where the mass is
assumed to be known, remember that the tool/total load that you use must
have the correct mass defined. Tap
OK
to confirm.
10 Select the configuration angle. The optimum is +90 or -90 degrees. If this is
impossible, tap
Other
and set the angle. The minimum is +30 or -30 degrees.
Continues on next page
190
Operating manual - OmniCore
3HAC065036-001 Revision: J
© Copyright 2019-2021 ABB. All rights reserved.
6 Programming and testing
6.10.7 Load identification service routine
Continued
Summary of Contents for OmniCore
Page 1: ...ROBOTICS Operating manual OmniCore ...
Page 8: ...This page is intentionally left blank ...
Page 24: ...This page is intentionally left blank ...
Page 62: ...This page is intentionally left blank ...
Page 72: ...This page is intentionally left blank ...
Page 98: ...This page is intentionally left blank ...
Page 234: ...This page is intentionally left blank ...
Page 242: ...This page is intentionally left blank ...
Page 264: ......
Page 265: ......