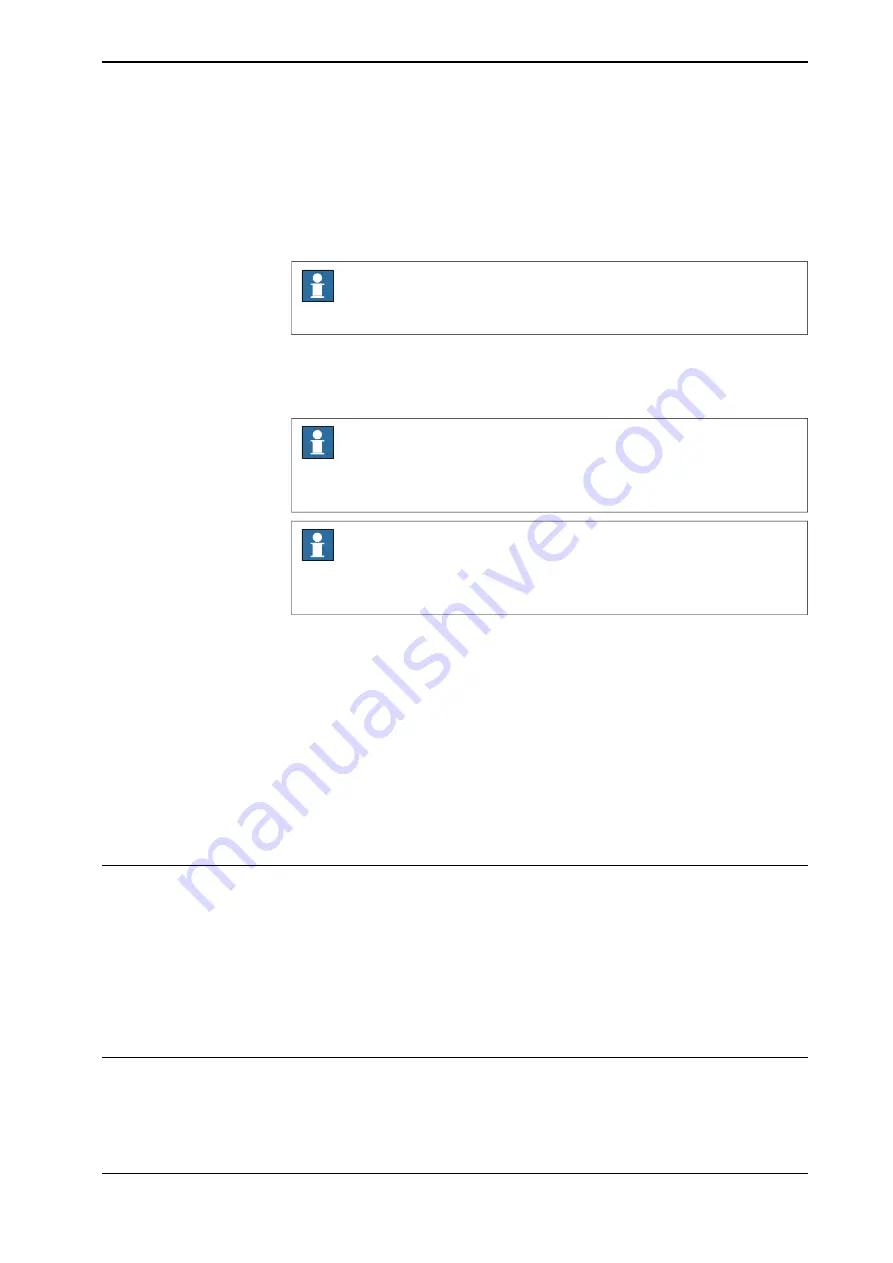
11 If the robot is not in correct position for load identification, you are asked to
jog one or more axes roughly to a specified position. When you have done
this tap
OK
to confirm.
If the robot is still not in a correct position for load identification, the robot
will slowly move to the correct position. Press
Move
to start the movement.
Note
Axis 1 to 3 must not be more than 10 degrees from proposed position.
12 The robot can go through the load identification movements slowly before
performing the load identification (slow test). Tap
Yes
if you want a slow test
and
No
to proceed to the identification.
Note
This is useful for ensuring that the robot will not hit anything during the
identification. However, this will take a lot longer time.
Note
If the load identification is planned to be run in manual full speed, then the
slow test is required before the actual measurement can start.
13 The setup for load identification is now complete. To start the motion, switch
to Automatic mode and Motors On. Then tap
Move
to start the load
identification movements.
14 When the identification is finished, switch back to manual mode, press the
three-position enabling device and the Start button. Tap
OK
to confirm.
15 The result of the load identification is now presented on the FlexPendant.
Tap
Tool
if you want to update the selected tool, tap
Loaddata
if you want
to update the total load, or tap
No
if you want to quit without saving.
16 If
Loaddata
is selected it is possible to update the total load to either an
existing or a new
loaddata
persistent variable.
Error handling
If the three-position enabling device is released during the load identification (before
the movements start), the routine can always be restarted by pressing the
three-position enabling device again and then pressing the START button.
If an error should occur during the load identification movements, the routine must
be restarted from the beginning. This is done automatically by pressing Start after
confirming the error. To interrupt and leave the load identification procedure, tap
Cancel Call Routine
in
Program Editor
debug menu.
Limitations for LoadIdentify
Only tool loads and payloads can be identified with LoadIdentify. Thus arm loads
cannot be identified.
Continues on next page
Operating manual - OmniCore
191
3HAC065036-001 Revision: J
© Copyright 2019-2021 ABB. All rights reserved.
6 Programming and testing
6.10.7 Load identification service routine
Continued
Summary of Contents for OmniCore
Page 1: ...ROBOTICS Operating manual OmniCore ...
Page 8: ...This page is intentionally left blank ...
Page 24: ...This page is intentionally left blank ...
Page 62: ...This page is intentionally left blank ...
Page 72: ...This page is intentionally left blank ...
Page 98: ...This page is intentionally left blank ...
Page 234: ...This page is intentionally left blank ...
Page 242: ...This page is intentionally left blank ...
Page 264: ......
Page 265: ......