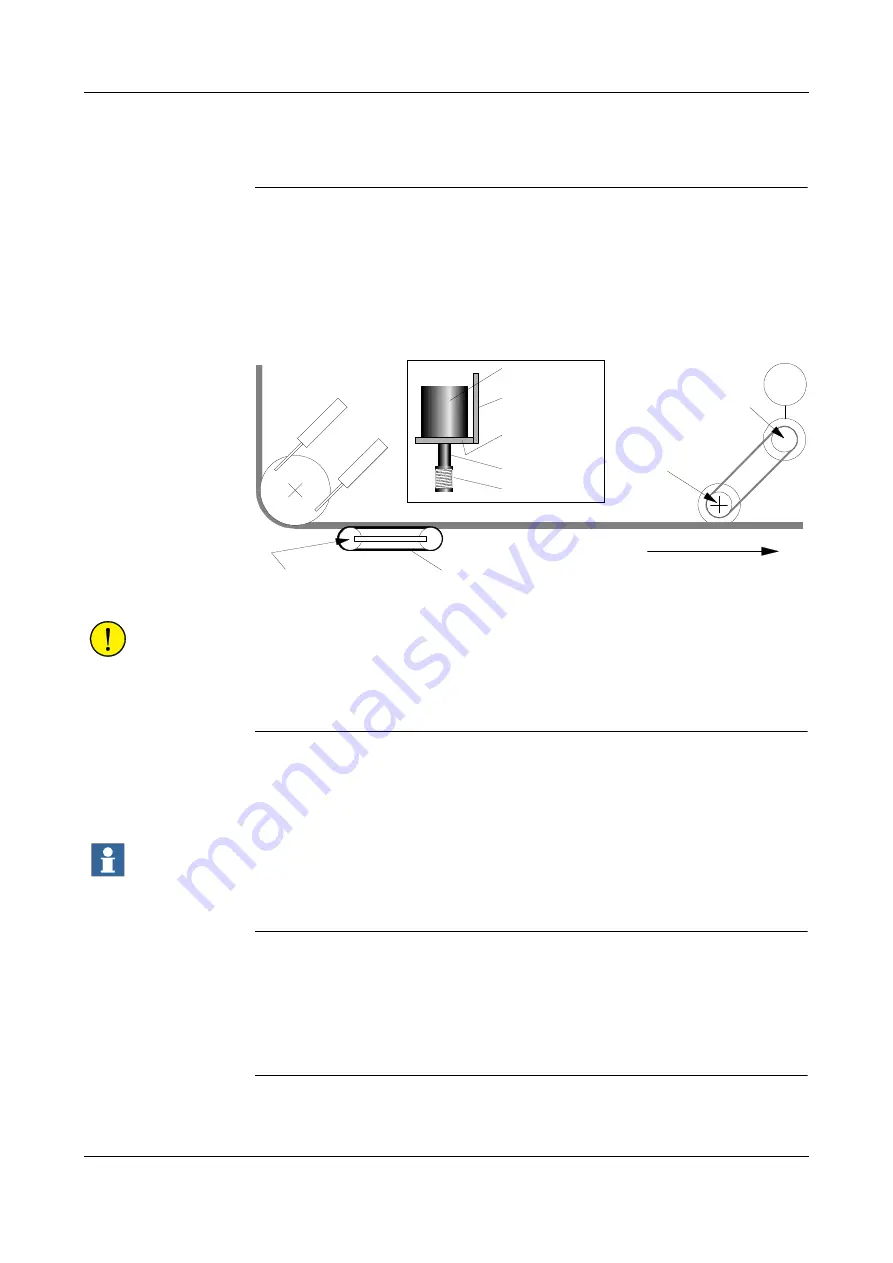
5 Installation and Commissioning
Product Manual, Control Cabinet IRC5P
91
5.6 Encoder and Sync Switch Installation
5.6.5 Encoder Installation
General
The encoder must be installed in such a way that it gives a precise feedback of the
conveyor motion (reflects the true conveyor motion). This means that the encoder
should be installed as close to the robot as practically possible, typically not more
than 30 meters away, and that a good connection between the encoder shaft and the
conveyor should be made.
Figure 39 Conveyor and encoder, top view
CAUTION!
The encoder is a sensitive measuring device and it is for this reason
important that no other forces than the shaft rotation is transferred from the
conveyor to the encoder, and that the encoder is mounted using shock absorbers to
prevent damage from vibration.
Mechanical Connection
The encoder can be installed in conjunction with the conveyor drive unit or
connected via a chain system, called ‘auxiliary chain’, gripping into the conveyor
chain. The encoder shaft can be connected to the shaft of the conveyor drive wheel
or one of the wheels of the ‘auxiliary chain’.
Important:
The encoder must not be connected directly to the conveyor drive unit
itself, as play in the drive belt will not be registered, and, if the drive belt should
break, the robot will operate as if the conveyor was still running.
Using Flexible Coupling
The connection can be performed either directly to the shaft via a flexible coupling,
or more commonly via a drive belt, chain- or gear wheel arrangement. If a flexible
coupling is used, it must be a coupling specially designed for this purpose. A
coupling using a plastic/rubber hose should be avoided as it makes a connection
which is too stiff and thereby may cause damage to the encoder.
Conveyors with
‘Take-Up’ Station
If a ‘Take-Up’ is used (used to keep tension in the conveyor chain), the encoder
must be placed on the same side of the ‘Take-Up’ station as the robot.
Chain or
drivebelt
Encoder
Encoder bracket
Encoder shaft
Flexible coupling
Encoder
attachment
Encoder must not be
connected to this shaft
Conveyor chain
'Take-Up station'
M
Conveyor drive
motor and gear
Encoder connection
point on conveyor
drive
Encoder connection
point to auxiliary chain
Conveyor direction
Conveyor chain
'Auxiliary chain'
Summary of Contents for IRC5P
Page 1: ...The heart of Robotics Product Manual Control Cabinet IRC5P 3HNA009834 001 en Rev 06 ...
Page 2: ......
Page 10: ...10 3HNA009834 001 en Rev 06 Product Manual Control Cabinet IRC5P ...
Page 14: ...2 Safety 14 3HNA009834 001 en Rev 06 Product Manual Control Cabinet IRC5P ...
Page 218: ...218 3HNA009834 001 en Rev 06 Product Manual Control Cabinet IRC5P Manual Status ...