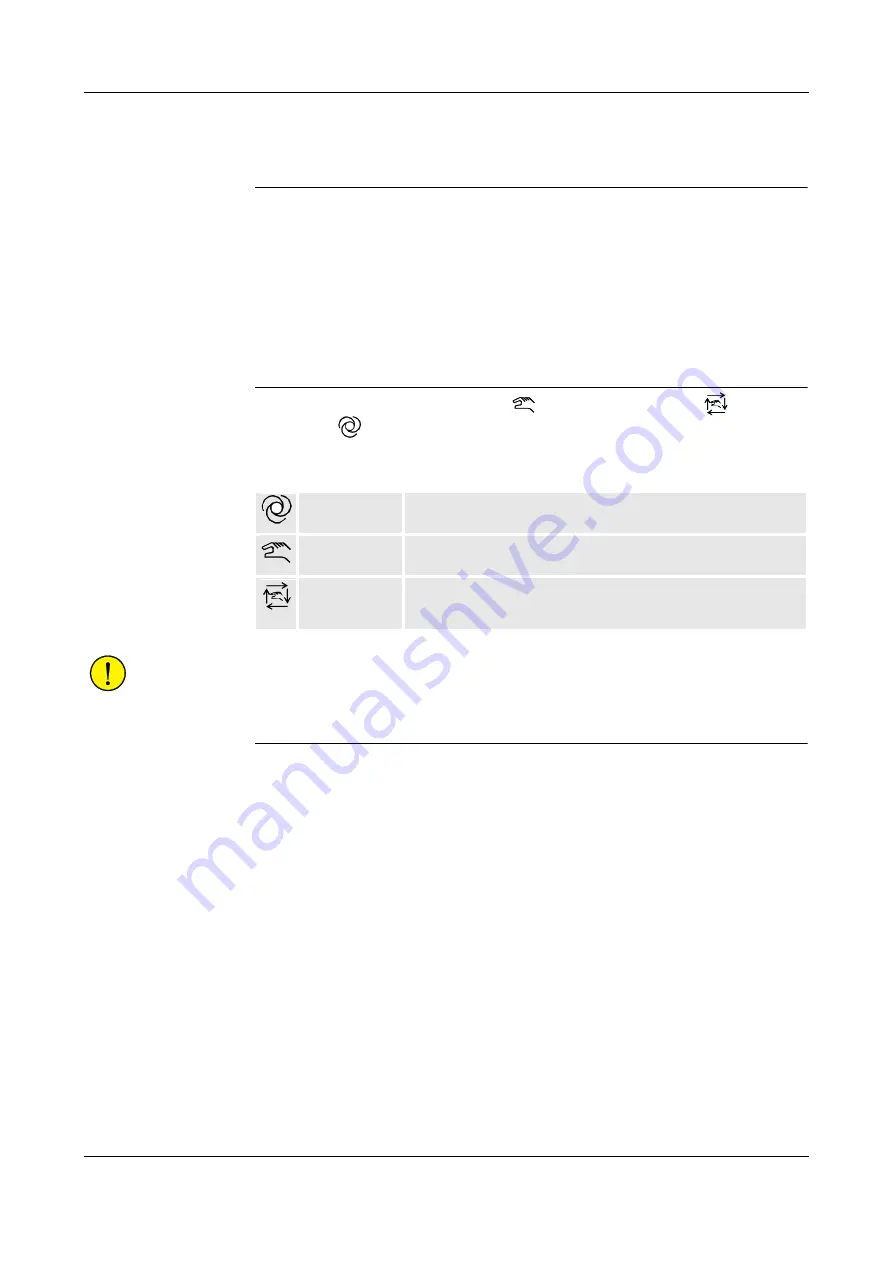
5 Installation and Commissioning
Product Manual, Control Cabinet IRC5P
73
5.4 Robot Safety System Connections
5.4.5 Run Chain
General
The run chain is a dual channel chain where all switches must be closed to be able to
run the robot. Breaking the run chain will remove electric power from the robot axis
motors. By closing the run chain, power will be re-applied to the motors, and
operation can continue. The function of the run chain is depending on the position
of the Mode Selector on the main control panel. This section describes the
connections that can be made in the run chain.
A principle diagram of the run chain is shown in
Mode Selection
Test modes, Manual Reduced Speed /
- Manual High Speed /
and
Automatic /
mode, are operating modes selected by the mode selector key
switch on the main panel, and are part of the total safety concept for the robot
installation. The three operating modes are as follows:
CAUTION!
The key in the mode selector must be brought to the operating site
together with the pendant to avoid another person from accidentally changing the
operating mode for the robot.
Auto Mode Stop
(Category 0)
Operating the Auto Mode Stop function will remove power from the robot when the
mode selector is in Automatic mode. Typical use of this function is as safety switch
for the spray booth entrance door to allow for a person to enter the spray booth for
test or programming when the robot is in Manual Reduced / High Speed mode. If
the spray booth has more entrances, switches must be installed in series for all
entrances. Light grid / switches must also be installed at the conveyor entrance / exit
etc.
•
To install the Auto Mode Stop switch, install a 2 pole switch at terminals marked
‘Auto Mode Stop’ (for chain 1 and 2) in connector SCB-X1 pin 5-8 as shown in
and in principle diagram in
. The switch must be of a type
which will be closed when activated (spray booth door closed etc.). The switch
Note:
To prevent running the robot without paying attention to the auto mode stop
switch, the robot is shipped without jumper installed in this position.
Automatic mode: Used to run the robot in production.
Manual Reduced
Speed mode:
Used for program teach and program optimizing purpose. Maximum
robot speed is restricted to 250 mm/sec.
Manual High
Speed Mode:
Used to run the program for test and program optimizing. Robot may
be running at full speed (no optimizing operations that can change the
path of the robot can be performed).
Summary of Contents for IRC5P
Page 1: ...The heart of Robotics Product Manual Control Cabinet IRC5P 3HNA009834 001 en Rev 06 ...
Page 2: ......
Page 10: ...10 3HNA009834 001 en Rev 06 Product Manual Control Cabinet IRC5P ...
Page 14: ...2 Safety 14 3HNA009834 001 en Rev 06 Product Manual Control Cabinet IRC5P ...
Page 218: ...218 3HNA009834 001 en Rev 06 Product Manual Control Cabinet IRC5P Manual Status ...