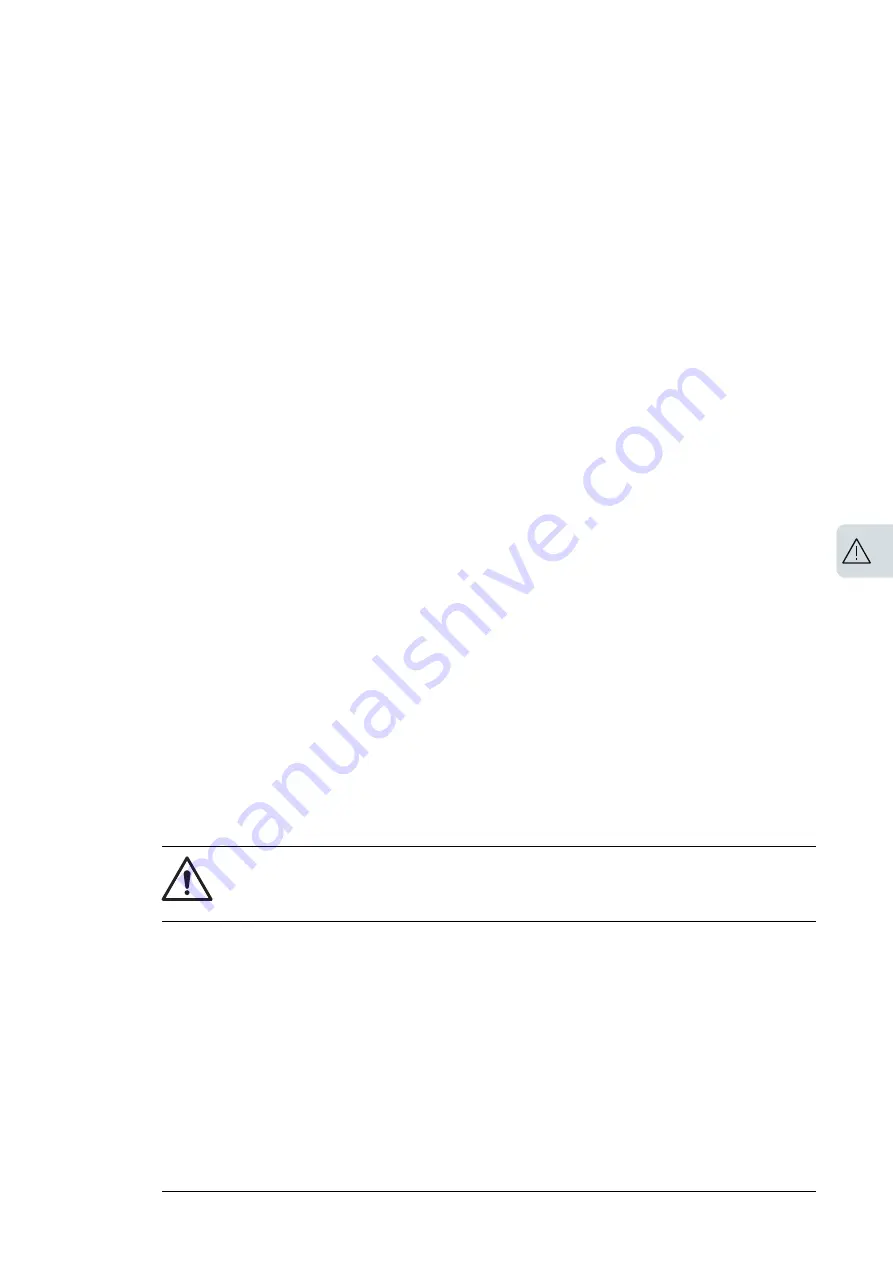
•
Beware of hot surfaces. Some parts, such as heatsinks of power semiconductors, and
brake resistors, remain hot for a while after disconnection of the electrical supply.
•
Make sure that debris from borings and grindings does not enter the drive during the
installation. Electrically conductive debris inside the drive may cause damage or
malfunction.
•
Make sure that there is sufficient cooling. See the technical data.
•
Keep the cabinet doors closed when the drive is powered. With the doors open, a risk
of a potentially fatal electric shock, arc flash or high-energy arc blast exists. If you cannot
avoid working on a powered drive, obey the local laws and regulations on live working
(including – but not limited to – electric shock and arc protection).
•
Before you adjust the drive operation limits, make sure that the motor and all driven
equipment can operate throughout the set operation limits.
•
Before you activate the automatic fault reset or automatic restart functions of the drive
control program, make sure that no dangerous situations can occur. These functions
reset the drive automatically and continue operation after a fault or supply break. If these
functions are activated, the installation must be clearly marked as defined in
IEC/EN 61800-5-1, subclause 6.5.3, for example, "THIS MACHINE STARTS
AUTOMATICALLY".
•
The maximum drive power cycles is once every 2 minutes. Power cycling the drive too
often can damage the charging circuit of the DC capacitors.
•
Validate any safety circuits (for example, Safe torque off or emergency stop) in start-up.
See separate instructions for the safety circuits.
Note:
•
If you select an external source for the start command and it is on, the drive will start
immediately after fault reset unless you configure the drive for pulse start. See the
firmware manual.
•
Depending on the wiring and parametrization of the drive, the stop key on the control
panel may not stop the drive.
•
Only authorized persons are allowed to repair a malfunctioning drive.
■
Work on the liquid cooling system
These instructions are intended for all personnel that do installation, commissioning and
maintenance work on the liquid cooling system.
WARNING!
Obey these instructions. If you ignore them, injury or death, or damage to the
equipment can occur.
•
Use the required personal protective equipment. See the Safety data sheet for
Antifrogen
®
L coolant by Clariant (www.clariant.com) for the instructions on the
respiratory, hand and eye protection when handling the coolant.
•
Beware of hot, high-pressure coolant (6 bar, max. 50 °C) that is present in the internal
cooling circuit when it is in operation. Before you disconnect a pipe, release the pressure.
Close the appropriate stop valve(s). If necessary, stop the cooling circuit pumps.
•
Avoid skin contact with coolant. If coolant splashes onto the skin or in the eyes, rinse
immediately with plenty of water. Do not syphon it by mouth. If you swallow or get it into
the eyes, seek medical advice.
•
Before the drive power up, make sure that the internal cooling circuit is filled up with
coolant, and the cooling is in operation (coolant circulates).
Safety instructions 15
Summary of Contents for ACS880-37LC
Page 1: ... ABB INDUSTRIAL DRIVES ACS880 37LC drives Hardware manual ...
Page 2: ......
Page 4: ......
Page 78: ...78 ...
Page 116: ...116 ...
Page 134: ...5 Set the real time clock 134 Maintenance ...
Page 144: ...144 ...
Page 167: ... Dimension drawing examples ACS880 37LC 0390A 7 with main contactor Dimensions 167 ...
Page 169: ...ACS880 37LC 1270A 7 with common motor terminal cubicle Dimensions 169 ...
Page 170: ...ACS880 37LC 1940A 7 with common motor terminal cubicle 170 Dimensions ...
Page 172: ...Location and size of input terminals Contact ABB for details 172 Dimensions ...
Page 174: ...Inverter module cubicle with two R8i modules bottom cable exit 174 Dimensions ...
Page 175: ...Inverter module cubicle with three R8i modules bottom cable exit Dimensions 175 ...
Page 176: ...Brake chopper cubicle D150 176 Dimensions ...
Page 178: ...Cubicle width 300 mm top cable exit 178 Dimensions ...
Page 179: ...Cubicle width 400 mm bottom cable exit Dimensions 179 ...
Page 180: ...Cubicle width 400 mm top cable exit 180 Dimensions ...
Page 181: ...Cubicle width 600 mm bottom cable exit Dimensions 181 ...
Page 182: ...Cubicle width 600 mm top cable exit 182 Dimensions ...
Page 198: ...198 ...
Page 200: ...200 ...