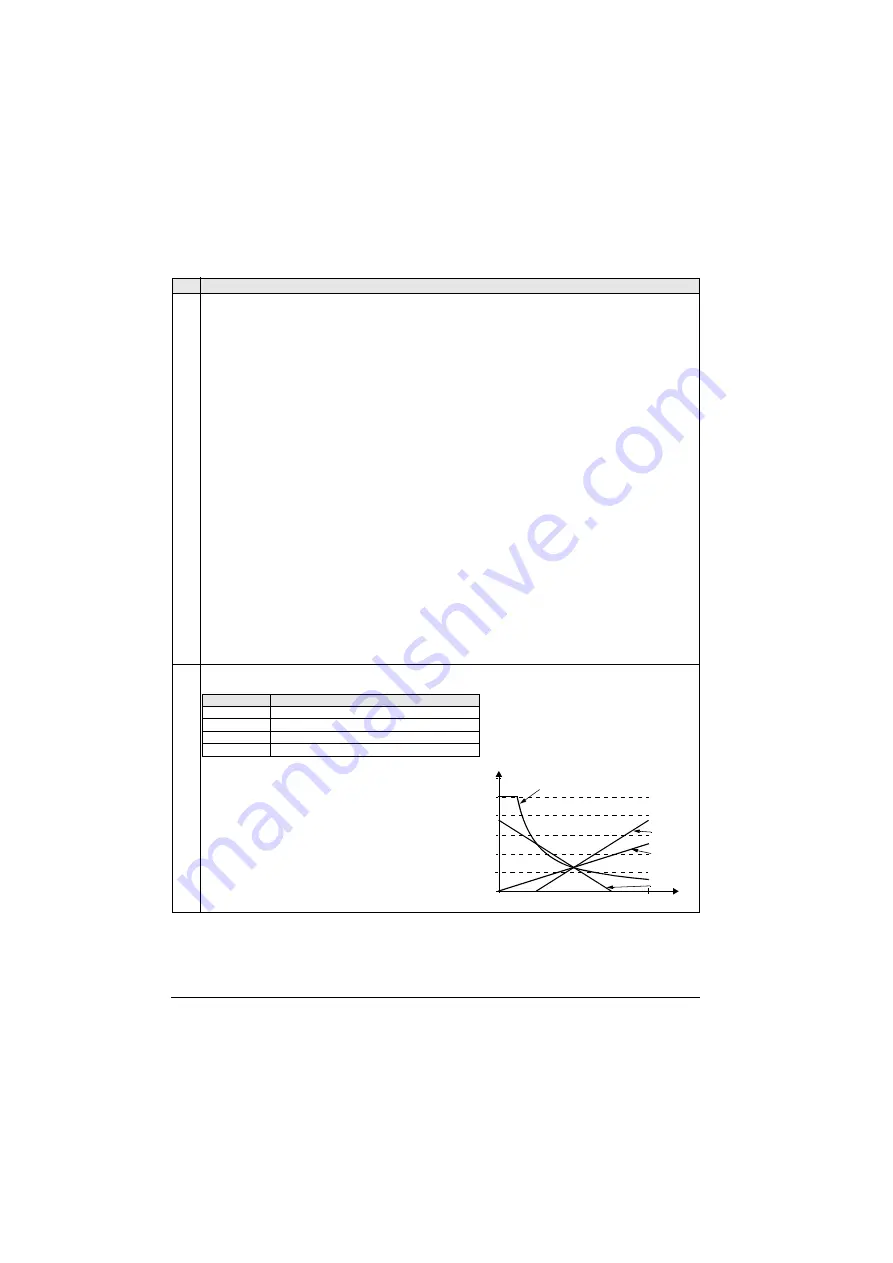
110
ACS550 User’s Manual
5 =
DI
3
U
,4
D
(
R
) – Defines digital inputs as the speed reference source (motor potentiometer control).
• Digital input
DI
3 increases the speed (the
U
stands for “up”).
• Digital input
DI
4 decreases the speed (the
D
stands for “down”).
• A Stop command resets the reference to zero (the
R
stands for “reset”).
• Parameter 2205
ACCELER
TIME
2 controls the reference signal’s rate of change.
6 =
DI
3
U
,4
D
– Same as above (
DI
3
U
,4
D
(
R
)), except:
• A Stop command does not reset the reference to zero. The reference is stored.
• When the drive restarts, the motor ramps up (at the selected acceleration rate) to the stored reference.
7 =
DI
5
U
,6
D
– Same as above (
DI
3
U
,4
D
), except that
DI
5 and
DI
6 are the digital inputs used.
8 =
COMM
– Defines the fieldbus as the reference source.
9 =
COMM
+
AI
1 – Defines a fieldbus and analog input 1 (
AI
1) combination as the reference source. See Analog input
reference correction below.
10 =
COMM
*
AI
1 – Defines a fieldbus and analog input 1 (
AI
1) combination as the reference source. See Analog input
reference correction below.
11 =
DI
3
U
,4
D
(
RNC
) – Same as
DI
3
U
,4
D
(
R
) above, except that:
• Changing the control source (
EXT
1 to
EXT
2,
EXT
2 to
EXT
1,
LOC
to
REM
) does not copy the reference.
12 =
DI
3
U
,4
D
(
NC
) – Same as
DI
3
U
,4
D
above, except that:
• Changing the control source (
EXT
1 to
EXT
2,
EXT
2 to
EXT
1,
LOC
to
REM
) does not copy the reference.
13 =
DI
5
U
,6
D
(
NC
) – Same as
DI
5
U
,6
D
above, except that:
• Changing the control source (
EXT
1 to
EXT
2,
EXT
2 to
EXT
1,
LOC
to
REM
) does not copy the reference.
14 =
AI
1+
AI
2 – Defines an analog input 1 (
AI
1) and analog input 2 (
AI
2) combination as the reference source. See
Analog input reference correction below.
15 =
AI
1*
AI
2 – Defines an analog input 1 (
AI
1) and analog input 2 (
AI
2) combination as the reference source. See
Analog input reference correction below.
16 =
AI
1-
AI
2 – Defines an analog input 1 (
AI
1) and analog input 2 (
AI
2) combination as the reference source. See
Analog input reference correction below.
17 =
AI
1/
AI
2 – Defines an analog input 1 (
AI
1) and analog input 2 (
AI
2) combination as the reference source. See
Analog input reference correction below.
20 =
KEYPAD
(
RNC
) – Defines the control panel as the reference source.
• A Stop command resets the reference to zero (the
R
stands for reset.).
• Changing the control source (
EXT
1 to
EXT
2,
EXT
2 to
EXT
1) does not copy the reference.
21 =
KEYPAD
(
NC
) – Defines the control panel as the reference source.
• A Stop command does not reset the reference to zero. The reference is stored.
• Changing the control source (
EXT
1 to
EXT
2,
EXT
2 to
EXT
1) does not copy the reference.
Analog input reference correction
Parameter values 9, 10 and 14…17 use the formula in the following table.
Where:
• C = Main reference value
( =
COMM
for values 9, 10 and
=
AI
1 for values 14…17).
• B = Correcting reference
( =
AI
1 for values 9, 10 and
=
AI
2 for values 14…17).
Example:
The figure shows the reference source curves for value
settings 9, 10 and 14…17, where:
• C = 25%.
• P 4012
SETPOINT
MIN
= 0.
• P 4013
SETPOINT
MAX
= 0.
• B varies along the horizontal axis.
Code Description
Value setting
Calculation of the AI reference
C + B
C value + (B value - 50% of reference value)
C * B
C value · (B value / 50% of reference value)
C - B
(C value + 50% of reference value) - B value
C / B
(C value · 50% of reference value) / B value
120
100
80
60
40
20
0
0
100%
9, 14 (+)
16 (-)
10, 15 (*)
17 (/)
B
Summary of Contents for ACS550 Series
Page 1: ...ACS550 User s Manual ACS550 01 Drives 0 75 132 kW ACS550 U1 Drives 1 200 hp ...
Page 4: ......
Page 10: ...10 ACS550 User s Manual Table of contents ...
Page 84: ...84 ACS550 User s Manual Application macros ...
Page 188: ...188 ACS550 User s Manual Parameters ...
Page 242: ...242 ACS550 User s Manual Fieldbus adapter ...
Page 276: ...276 ACS550 User s Manual Technical data WARNING Do not use RFI EMC filters on IT systems ...