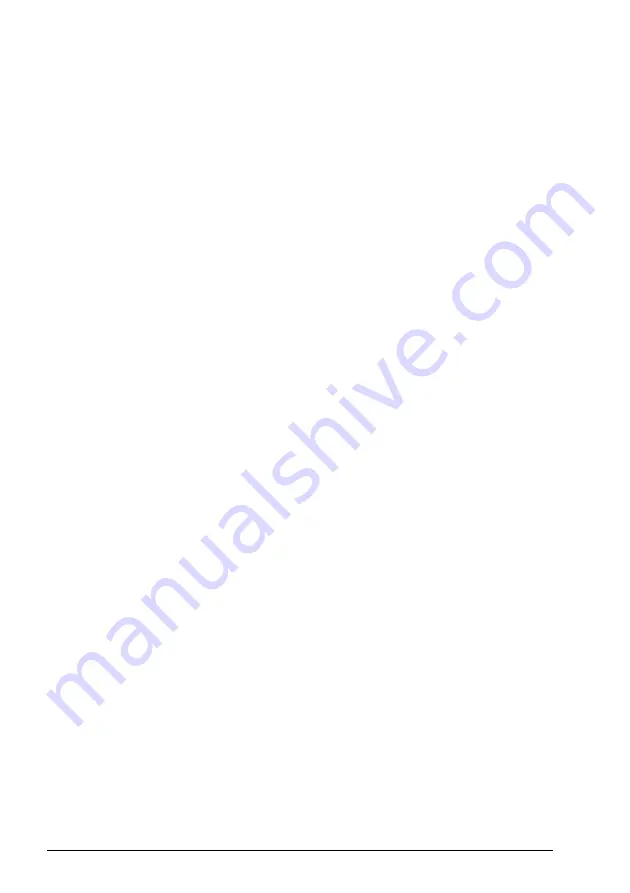
48 Planning the electrical installation
Other regions
The disconnecting device must conform to the applicable local safety regulations.
Checking the compatibility of the motor and drive
Use an asynchronous AC induction motor, permanent magnet motor or synchronous
reluctance motor (SynRM) with the drive. Several induction motors can be connected
to the drive at a time.
Make sure that the motor and the drive are compatible according to the rating table in
section
. The table lists the typical motor power for each drive
type.
Selecting the power cables
Select the input power and motor cables according to the local regulations:
• The input power and the motor cables must be able to carry the corresponding
.
• The cable must be rated for at least 70
°
C maximum permissible temperature of
conductor in continuous use. For the US, refer to
page
• The conductivity of the PE conductor must be sufficient, refer to page
• A 600 V AC cable is accepted for up to 500 V AC.
To comply with the EMC requirements of the CE mark, use an approved cable type.
Refer to
on page
Use a symmetrical shielded cable to decrease:
• The electromagnetic emissions of the drive system.
• The stress on the motor insulation.
• The bearing currents.
The protective conductor must always have an adequate conductivity.
Unless local wiring regulations state otherwise, the cross-sectional area of the
protective conductor must agree with the conditions that require automatic
disconnection of the supply required in 411.3.2. of IEC 60364-4-41:2005 and be
capable of withstanding the prospective fault current during the disconnection time of
the protective device.
The cross-sectional area of the protective conductor can either be selected from the
table below or calculated according to 543.1 of IEC 60364-5-54.
This table shows the minimum cross-sectional area related to the phase conductor
size according to IEC 61800-5-1 when the phase conductor and the protective
conductor are made of the same metal. If this is not so, the cross-sectional area of
Summary of Contents for ACS380 Series
Page 1: ...ABB MACHINERY DRIVES ACS380 drives Hardware manual...
Page 4: ......
Page 12: ...12 Table of contents...
Page 20: ...20 Safety instructions...
Page 46: ...46 Mechanical installation...
Page 60: ...60 Planning the electrical installation...
Page 86: ...86 Maintenance...
Page 120: ...120 Technical data...
Page 122: ...122 Dimension drawings Frame R0 1 phase 230 V...
Page 123: ...Dimension drawings 123 Frame R0 400 V...
Page 124: ...124 Dimension drawings Frame R1 230 V...
Page 125: ...Dimension drawings 125 Frame R1 3 phase 230 V and 3 phase 400 V...
Page 126: ...126 Dimension drawings Frame R2 230 V...
Page 127: ...Dimension drawings 127 Frame R2 400 V...
Page 128: ...128 Dimension drawings Frame R3 400 V...
Page 129: ...Dimension drawings 129 Frame R4 400 V...
Page 130: ...130 Dimension drawings...
Page 138: ...138 Resistor braking...
Page 169: ...BTAC 02 pulse encoder interface module 169 Dimensions 3AXD50000031154 rev A...