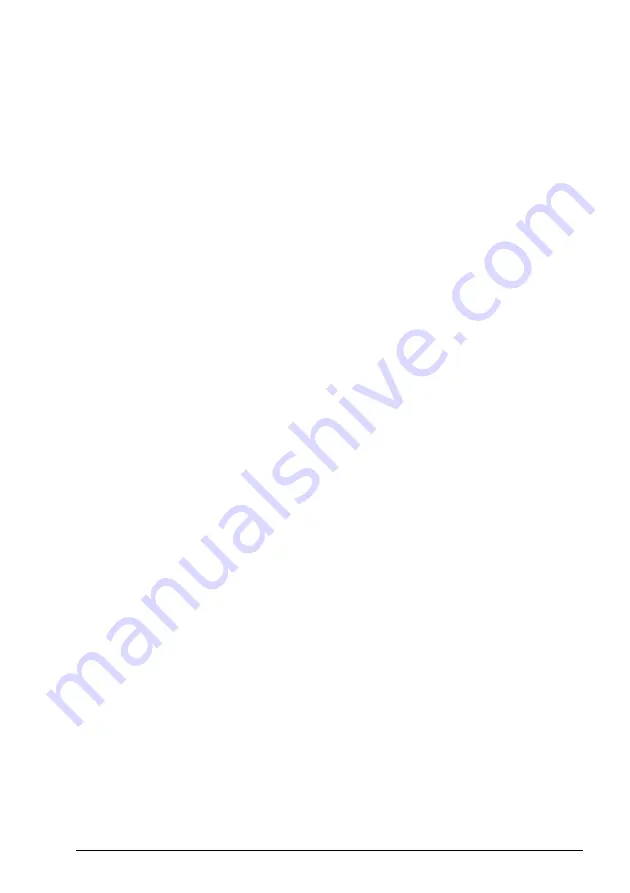
Safe torque off function 143
Cable types and lengths
• Double-shielded twisted-pair cable is recommended.
• Maximum cable length 100 m (328 ft) between activation switch (K) and drive
control unit.
Note:
A short-circuit in the wiring between the switch and an STO terminal causes a
dangerous fault and therefore it is recommended to use a safety relay (including
wiring diagnostics), or a wiring method (shield grounding, channel separation) which
reduces or eliminates the risk caused by the short-circuit.
Note:
The voltage at the S1 and S2 terminals of each drive must be at least 13 V DC
to be interpreted as “1”. Pulse tolerance of input channels is 1 ms.
Grounding of protective shields
• Ground the shield in the cabling between the activation switch and the control
board at the control board.
• Ground the shield in the cabling between two control boards at one control board
only.
Operation principle
1. The Safe torque off activates (the activation switch is opened, or safety relay
contacts open).
2. The STO inputs S1 and S2 on the drive control board de-energize.
3. The STO cuts off the control voltage from the output IGBTs.
4. The control program generates an indication as defined by parameter
31.22 STO
indication run/stop
.
The parameter selects which indications are given when one or both Safe torque
off (STO) signals are switched off or lost. The indications also depend on whether
the drive is running or stopped when this occurs.
Note:
This parameter does not affect the operation of the STO function itself. The
STO function will operate regardless of the setting of this parameter: a running
drive will stop upon removal of one or both STO signals, and will not start until
both STO signals are restored and all faults reset.
Note:
The loss of only one STO signal always generates a fault as it is interpreted
as a malfunction of STO hardware or wiring.
5. The motor coasts to a stop (if running). The drive cannot restart while the
activation switch or safety relay contacts are open. After the contacts close, a
reset may be needed (depending on the setting of parameter
31.22).
A new start
command is required to start the drive.
Summary of Contents for ACS380 Series
Page 1: ...ABB MACHINERY DRIVES ACS380 drives Hardware manual...
Page 4: ......
Page 12: ...12 Table of contents...
Page 20: ...20 Safety instructions...
Page 46: ...46 Mechanical installation...
Page 60: ...60 Planning the electrical installation...
Page 86: ...86 Maintenance...
Page 120: ...120 Technical data...
Page 122: ...122 Dimension drawings Frame R0 1 phase 230 V...
Page 123: ...Dimension drawings 123 Frame R0 400 V...
Page 124: ...124 Dimension drawings Frame R1 230 V...
Page 125: ...Dimension drawings 125 Frame R1 3 phase 230 V and 3 phase 400 V...
Page 126: ...126 Dimension drawings Frame R2 230 V...
Page 127: ...Dimension drawings 127 Frame R2 400 V...
Page 128: ...128 Dimension drawings Frame R3 400 V...
Page 129: ...Dimension drawings 129 Frame R4 400 V...
Page 130: ...130 Dimension drawings...
Page 138: ...138 Resistor braking...
Page 169: ...BTAC 02 pulse encoder interface module 169 Dimensions 3AXD50000031154 rev A...