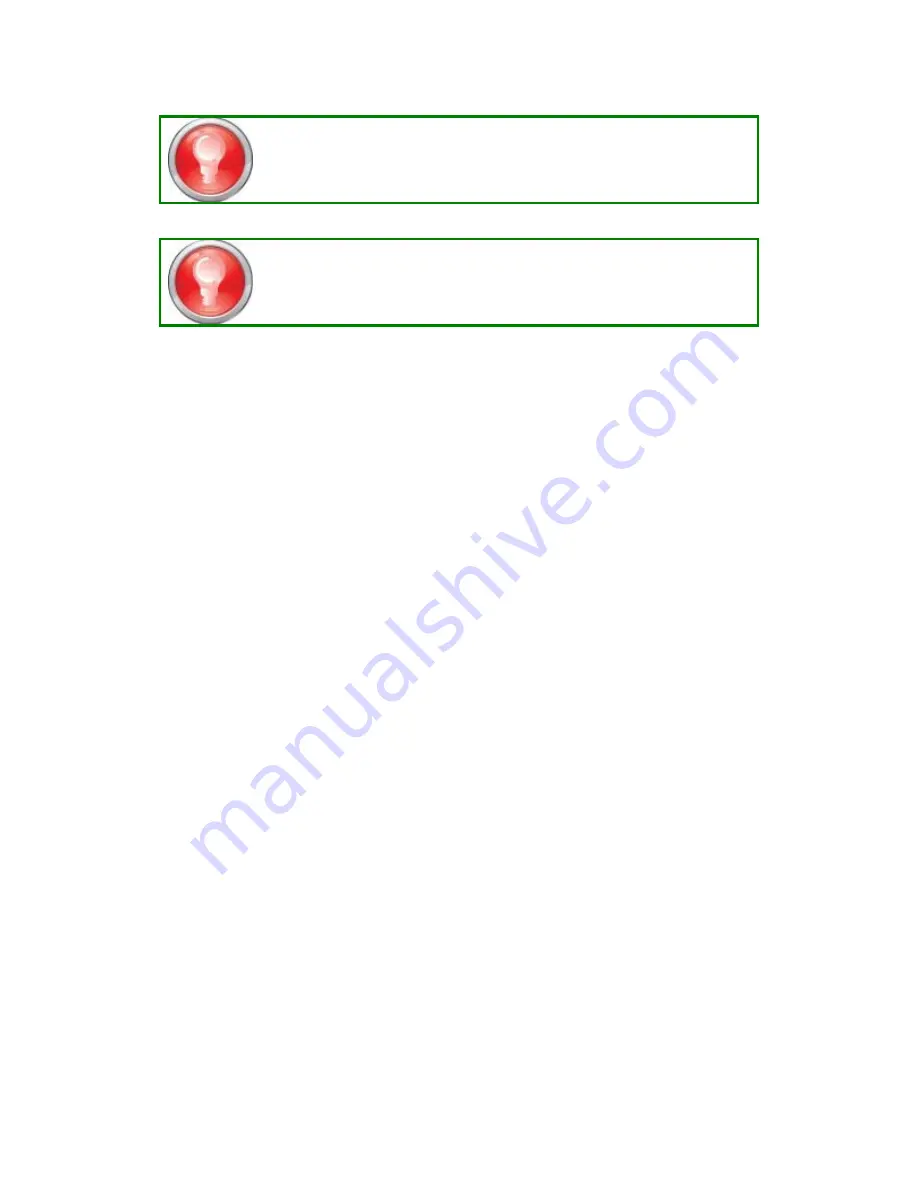
ZScan Manual
34
For better digitization, any object that is shinny, black, transparent
or reflective, (mirror, shiny or metallic surface) might need to be
covered with white powder in order to give it a matte finish.
Proper target distribution may be difficult to obtain, particularly for
small surfaces (small objects). It is then suggested to distribute the
targets on a plane (preferably black/dark and matte) and to
place the object on this plane.
Importing Positioning Features
It is possible to import in ZScan a previously acquired positioning model or positioning
features acquired by the ZScanner 800 or by a photogrammetry system. The two types of
files that can be imported are .txt and .obc files.
The text files (.txt) to be imported must include three columns (X, Y, Z), separated with a
SPACE. The three columns represent the center of the target. Files exported by ZScan are
exported in the right format and can be used natively by the software.
The .obc files are files produced by AICON photogrammetry systems. These files can be
imported directly into ZScan.
Imported targets will then appear as spheres in the 3D Viewer as it is impossible for ZScan
to know in which direction they are. The scanner will use the positioning targets pattern
to position itself in space and will add the normal after detecting the targets for the first
time. Please note that only ZScanner targets can be recognized. Any other type of
reflective target will not be usable in ZScan.
Using Sensor Configuration
Depending on the color and finish of the part to scan, the ZScanner 800's parameters
may require a little tuning. These adjustments are necessary to allow acquisition and to
limit the level of noise in the data. While the default laser and camera parameters are set
for a wide range of surfaces, it is possible that they need to be changed in order to
acquire the data properly. Moreover, when the part to scan includes more than one
color or finish, adjusting laser parameters becomes more complex.
Three situations can occur when trying to scan:
•
Under-exposition: The reflection of the laser is not or is weakly perceived by the
cameras. There is not enough information gathered by the software to calculate
and build a mesh from the physical surface.
•
Saturation: The reflection of the laser is so intense that the cameras are blinded.
The laser line is not clearly defined and may lead to an improper surface
reconstruction, or an unusual amount of noise in the data.