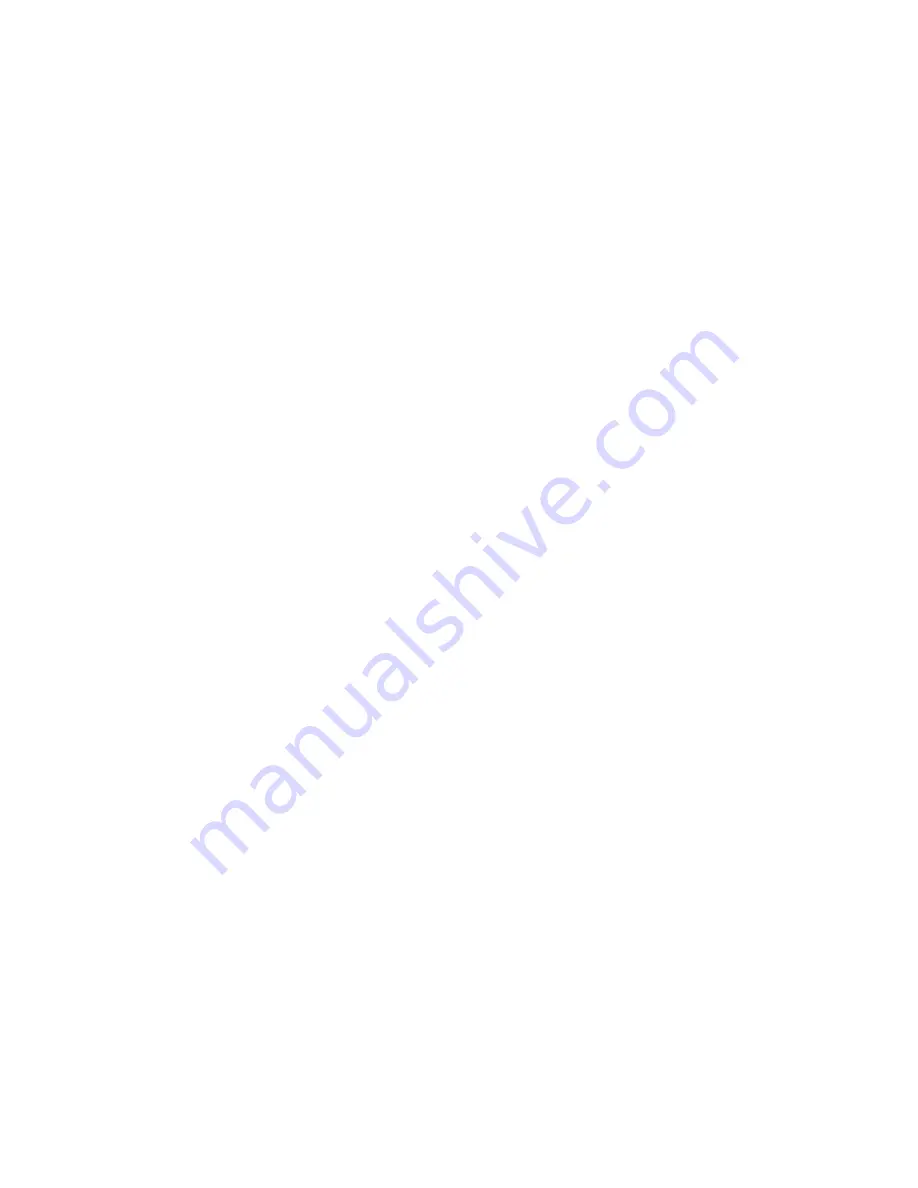
146
FORM 160.54-M1
ISSUE DATE: 10/25/2019
SECTION 14 - ADAPTIVE CAPACITY CONTROL BOARD
JCI COMPANY CONFIDENTIAL
JOHNSON CONTROLS
In Manual Speed Control Mode, the speed can be con-
trolled from the VSD
TUNING Screen using Keypad
keys. The speed can be set to a pre-selected frequency
over the range of 10 to 60 (50)Hz, using the SET key.
Or, it can be increased or decreased over the range of
0.0 to 60 (50)Hz in increments of 0.1 to 10Hz using the
RAISE/LOWER keys. Or, it can be set to full speed
using the FIXED key. Beginning with software version
C.OPT.01.23.307 (and later), the E-Link Gateway se-
rial communications can no longer change the setting
from AUTO to FIXED.
Instructions for manual control are included in
SECTION 33 - SYSTEM CALIBRATION, SERVICE
SETPOINTS, AND RESET PROCEDURES
manual. With software version C.OPT.01.19.307 (and
later), this is displayed as SPEED COMMAND on the
VSD TUNING Screen and ACC DETAILS Screen.
Via Serial communications, the speed command is
sent from the microboard to the ACC Board, where it
is passed on to the VSD Logic Board. The VSD Logic
Board controls the VSD to operate the motor at this
frequency. While Manual control is selected, VALID
POINT LED CR8 is illuminated, indicating that surges
will not be mapped in the Surge Map. Anytime this
LED is illuminated, surges are not mapped, as ex-
plained below. In making the transition from Manual
to Auto Mode, if the speed was manually set to less
than 30Hz, it will automatically be set to 30Hz and au-
tomatically adjusted from this value. If not in Current
Limit and the actual speed is less than 60 (50)Hz, and
60 (50)Hz is selected, the speed will be increased as
follows. If the Leaving Chilled Liquid Temperature is
within 0.2°F, the PRV will simultaneously be driven
closed according to the following:
Speed Increase
• 0.2 Hz every second if Leaving Chilled Liquid
Temperature greater than 0.2°F below the setpoint
and motor current is less than 80%FLA.
• 0.2 Hz every 1 + (% FLA-80) second if Leaving
Chilled Liquid Temperature is greater than 0.2°F
below the setpoint and the motor current is greater
than 80% but less than 98%FLA.
• 0.2 Hz every 19 seconds if none of the above con-
ditions are present.
PRV Close
A close signal of the following durations is applied
every 4.5 seconds:
• 3.9 seconds if PRV position greater than 50%.
• 3.0 seconds if PRV position greater than 25% but
less than 50%.
• 1.5 seconds if PRV position less than 25%.
In Auto Speed Control Mode, the ACC Board controls
the speed. It determines the optimum compressor mo-
tor speed (frequency) over the range of 30 to 60 (50)Hz
and sends this value to the VSD Logic Board via the
serial communications link. The VSD logic Board con-
trols the VSD to operate the motor at this frequency.
The optimum speed is the slowest speed possible that
will avoid compressor surge conditions but still allow
the chiller to meet capacity requirements. This speed is
found in an adaptive sense as explained below.
In determining the optimum motor speed, the ACC
Board employs the following:
•
Delta P/P –
This is the chiller Head pressure. It is
calculated as (Condenser Pressure minus Evapo-
rator Pressure) divided by Evaporator Pressure. It
ranges from 0.00 to 3.60. The ACC Board calcu-
lates this value from Evaporator and Condenser
Pressure Values received from the microboard
via serial communications link. The ACC Board
returns the calculated Delta P/P value to the mi-
croboard for display over the same link.
•
Pre-rotation Vanes (PRV) position –
The Pre-
rotation Vanes position, as used by the VSD con-
trol, is provided by a potentiometer mounted to
the PRV control arm. The potentiometer interface
varies according to whether or not the ACC Board
is used. In YORK Protocol configuration, it is
connected to the ACC Board (
In Modbus Protocol configuration, it is connected
The PRV position (0 to 100%) is displayed on the
OptiView display as 0% when fully closed, 100
% when fully open and whole percentage points
in between.