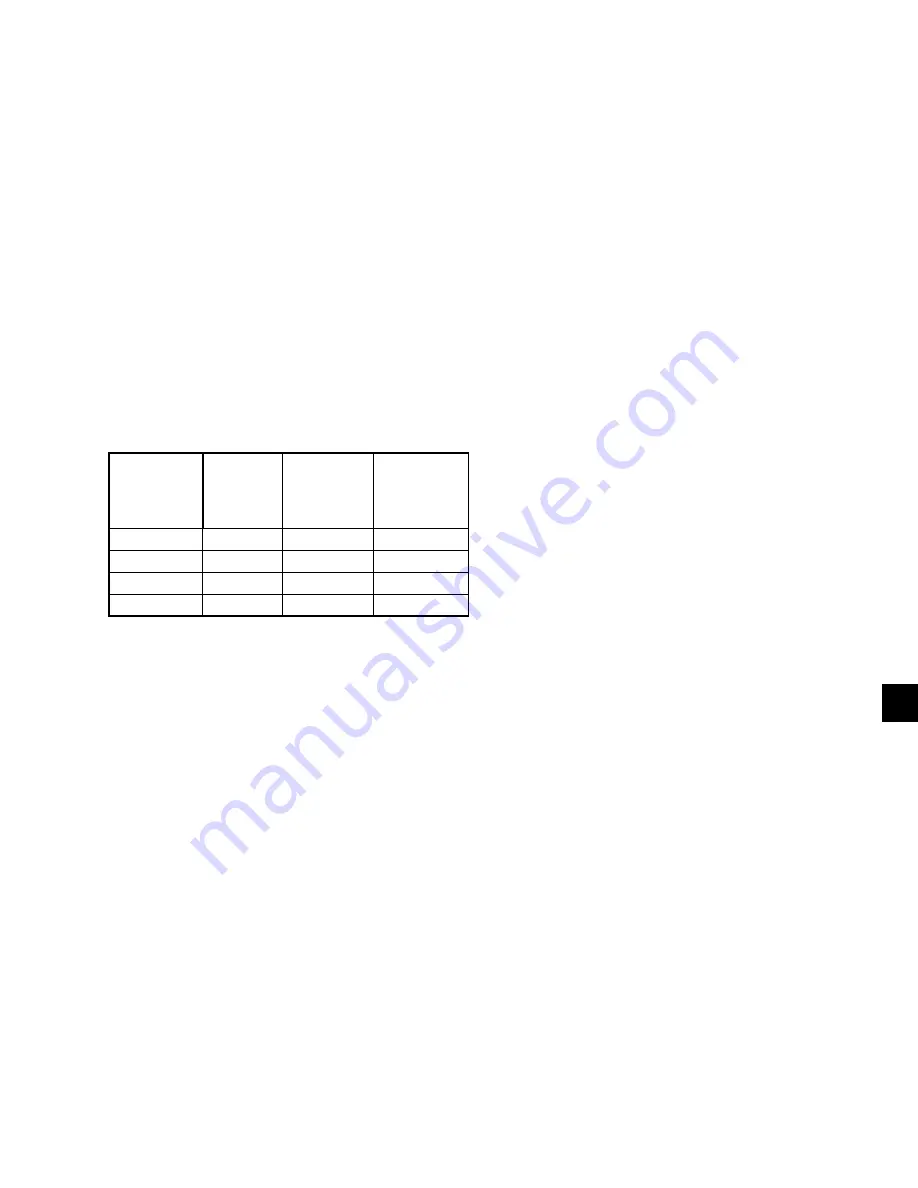
245
SECTION 29 - HEAD PRESSURE CONTROL
FORM 160.54-M1
ISSUE DATE: 10/25/2019
JOHNSON CONTROLS
JCI COMPANY CONFIDENTIAL
29
OPERATION WHEN EQUIPPED WITH BOTH
HEAT RECOVERY AND HEAD PRESSURE
CONTROL
If the chiller is equipped with both Heat Recovery and
Head Pressure Control and both are enabled, there is no
separate HEAD PRESSURE CONTROL Screen. All
Head Pressure Control Parameters and setpoints are
shown on the HEAT RECOVERY Screen. Also, there
is not a Control Valve for each feature. Rather, there is
one common valve that is either performing Hot Water
Control for Heat Recovery or Head Pressure Control.
It will not be performing control for both features at the
same time. Normally, it would be performing Hot wa-
ter Control until certain operating conditions cause it to
switch over to Head Pressure Control. The PID Control
Mode displays which feature is controlling the valve at
any given time. When performing Hot Water Control,
“Hot Water“ is displayed. When performing Head Pres-
sure Control, “Head Pressure“ is displayed. There are
also conditions under which it is not controlling either
feature, in which case “Inactive“ is displayed and the
valve is set to 0% position. Which feature is controlling
the vale at any given instant and when it is inactive is
determined by operating conditions as shown in flow
.
Remote Head Pressure Setpoint
This setpoint cannot be set from a remote input.
The Control Valve Output Settings keys are used to
configure the output signal to the Heat Recovery Con-
trol Valve. The Type setpoint is used to make the con-
trol signal either 0 to 10 VDC or 4 to 20mA.
The Auto setpoint is used to place the control in Auto-
matic Mode. The Set setpoint places the valve control
in manual. It is used to manually position the control
valve at any position between 0.0% and 100%. The
Control Valve Control Mode shall be reset to Auto
upon logging out of Service Level Access. The Control
Valve Control Mode data box displays the operating
Mode as MANUAL or AUTO as appropriate.
The PID Output setpoint is used to configure the signal
to the Control Valve to be DIRECT or REVERSE act-
ing (default DIRECT). In this application, it should be
set to DIRECT. The output for each setting is per the
following table.
CONTROL
VALVE
OUTPUT
TYPE
PID
OUTPUT
PID
CONTROL
0% OUTPUT
PID
CONTROL
100%
OUTPUT
0-10V
Direct
0V
10V
0-10V
Reverse
10V
0V
4 to 20mA
Direct
4mA (2V)
20mA (10V)
4 to 20mA
Reverse
20mA (10V)
4mA (2V)