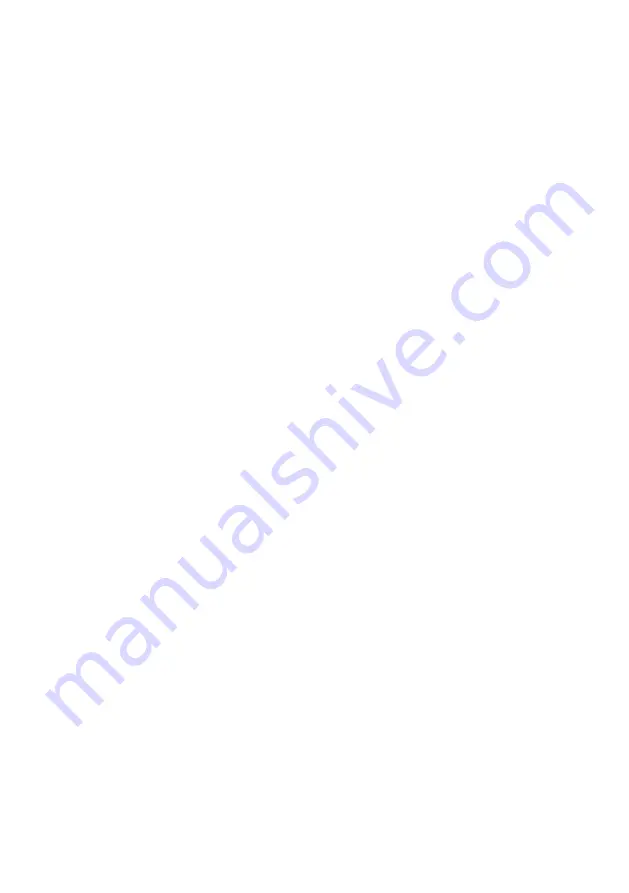
IM 12A06S01-00EN-P
25
o Stabilization time for pH/ORP:
During calibration, the stability of the pH value is constantly monitored. When variations
of the pH value during this stabilization time are within a value set in Step Range, the
value is regarded as being stable. If the measurement value does not stabilize within the
time set for stabilization (default 5 seconds), the calibration procedure is aborted.
o Calibration interval:
Set the interval in which a new calibration must take place. If the interval set here is
exceeded, the SA11 will notify according to the setting in “Calib. time exceeded” in the
error configuration.
•
Buffer select
Calibration is made using standard calibration buffers. Yokogawa recommends the NIST
(JIS equivalent) standard buffers for highest accuracy, but can also select DIN 19267 or
US. The standard buffers can be found in Appendix 2.
It is even possible to use a user-defined buffer. Three types of user-defined buffer tables
can be defined. These buffer tables are default defined as sodium buffers 4.00, 7.00 and
10.00. The buffer tables have to be set by an expert Yokogawa HOST system.
4.2 Communication setup
The SA11 is a slave device communicating with a HOST system using MODBUS protocol.
For correct communication the following settings can be made:
•
MODBUS address
The MODBUS address (Slave ID) is default set to 1, but can be set by HOST system to
another address in between #1 and #247.
•
Serial profile
MODBUS is an application layer messaging protocol which provides client/server
communication between devices connected on different types of buses/networks. The
SA11 is able to communicate with two predefined serial profile settings, to be selected by
the HOST system, which is default set to 1:
1. 9600 bps, 8 bits, even parity, 1 stop bit
2. 19200 bps, 8 bits, no parity, 2 stop bits
4.3 Error configuration
The SA11 contains error diagnostics, which is a summary of all related measurement
warnings, diagnostics, sensor statuses and other kind of failures. Part of the configuration
will be pre-defined by the sensor configuration as stored in the ID-chip.
Errors can be defined in different levels: critical and fail. An error will always result in non-
calculated output data or a pre-defined value. These errors and related limits are not user
configurable.
Beside this there are configurable measurement warnings. A warning is only a flag and has
no consequence for calculated output data.
At last there are sensor- and device statuses which reflect a certain state of performance
and/or operations. A sensor failure can result in a critical device error.
The SA11 show the four (4) categories:
• Critical device errors
• Sensor failures and sensor statuses
• Measurement warnings on calculated outputs
• Device status