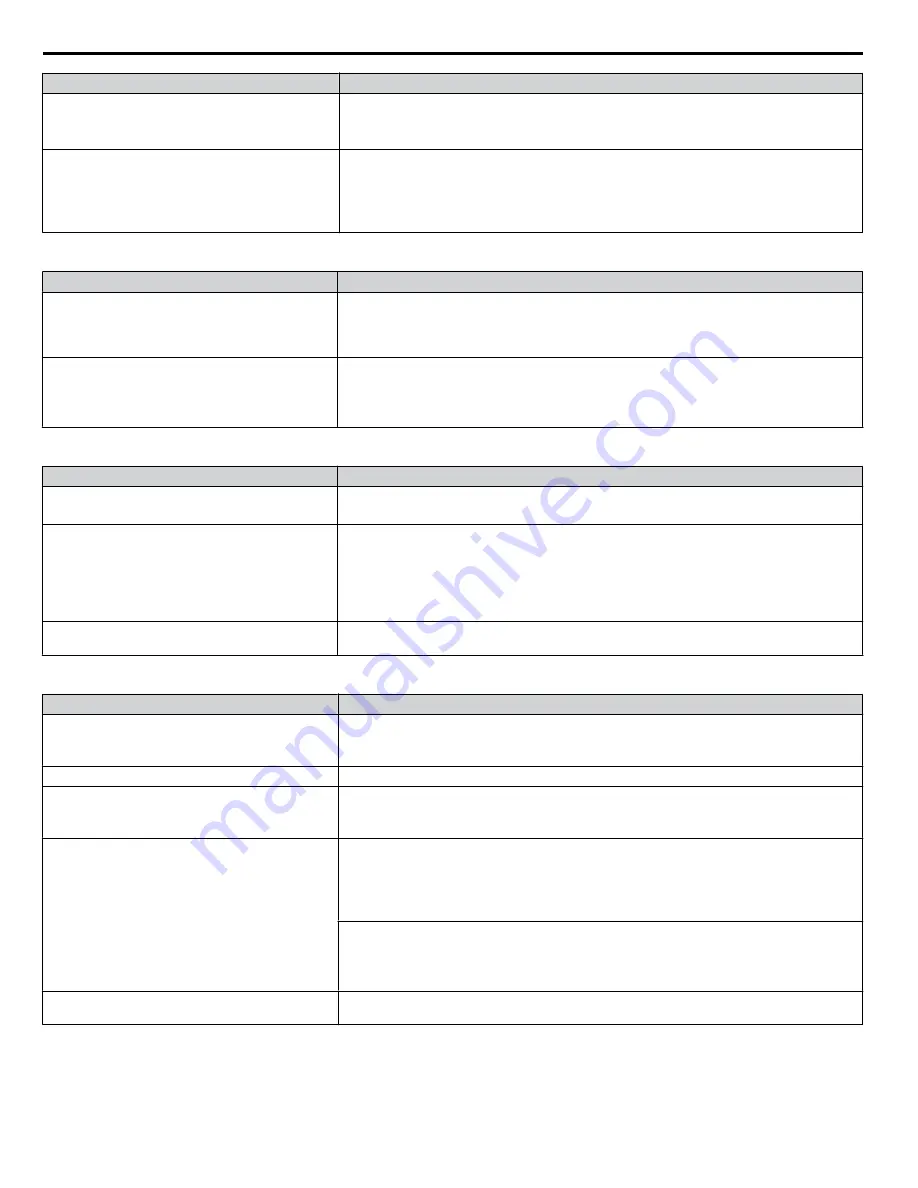
Cause
Possible Solutions
Although the drive is operating in Open Loop Vector
motor control method, Auto-Tuning has not been
performed.
• Perform Auto-Tuning.
• Calculate motor data and reset motor parameters.
• Switch to the V/f motor control method (A1-02 = “0”).
Drive reached the limitations of the V/f motor control
method.
• The motor cable may be long enough (over 50 m) to require Auto-Tuning for line-to-line
resistance.
• Be aware that V/f Control is comparatively limited when it comes to producing torque at low
speeds.
• Consider switching to Open Loop Vector Control.
n
Drive Frequency Reference Differs from the Controller Frequency Reference Command
Cause
Possible Solutions
The analog input frequency gain and bias are set to
incorrect values.
• Check the main speed frequency reference terminal input gain level assigned to terminals A1
and A2, as well as the frequency reference input bias to terminals A1 and A2 (parameters H3-03,
H3-04, and H3-12).
• Set these parameters to the appropriate values.
A frequency bias signal is being entered via analog
input terminals A1 or A2.
• If multi-function analog input terminals A1 and A2 are set for frequency reference (H3-02 = 0
and H3-10 = 0), the addition of both signals builds the frequency reference.
• Ensure that H3-02 and H3-10 are set appropriately.
• Check the input level set for terminals A1 and A2 (U1-13, U1-14).
n
Poor Speed Control Accuracy
Cause
Possible Solutions
Drive reached the slip compensation limit.
• Check the slip compensation limit (C3-03).
• Increase the value set to C3-03.
Motor-rated voltage is set too high in Open Loop
Vector Control.
• The input voltage for the drive determines the maximum output voltage. A drive with an input
of 200 Vac can only output a maximum of 200 Vac. Open Loop Vector Control sometimes
calculates an output voltage reference value that exceeds the maximum drive output voltage
level, resulting in a loss of speed control accuracy.
• Use a motor with a lower voltage rating (a vector control motor).
• Increase the input power voltage.
Auto-Tuning did not complete properly for Open Loop
Vector Control.
• Perform Auto-Tuning again.
n
Deceleration Takes Longer Than Expected with Dynamic Braking Enabled
Cause
Possible Solutions
L3-04 is set incorrectly.
• Check the Stall Prevention Level during deceleration (L3-04).
• If a braking resistor option has been installed, disable Stall Prevention during deceleration
(L3-04 = “0”).
The deceleration time is set too long.
Set deceleration to more appropriate time (C1-02, C1-04, C1-06, C1-08).
Insufficient motor torque.
• Assuming parameter settings are normal and that no overvoltage occurs when there is
insufficient torque, it is likely that the demand on the motor has exceeded the motor capacity.
• Use a larger motor.
Reaching the torque limit.
• Check the settings for the torque limit (L7-01 through L7-04).
• If the torque limit is enabled, deceleration might take longer than expected because the drive
cannot output more torque than the limit setting. Ensure the torque limit is set to a large enough
value.
• Increase the torque limit setting.
• If multi-function analog input terminal A1 or A2 is set to torque limit (H3-02 or H3-10 equals
10, 11, 12, or 15), ensure that the analog input levels are set to the correct levels.
• Ensure H3-02 and H3-10 are set to the right levels.
• Ensure the analog input is set to the correct value.
Load exceeded the internal torque limit determined by
the drive rated current.
Switch to a larger capacity drive.
6.9 Troubleshooting without Fault Display
304
YASKAWA ELECTRIC SIEP C710606 18F YASKAWA AC Drive – V1000 Technical Manual