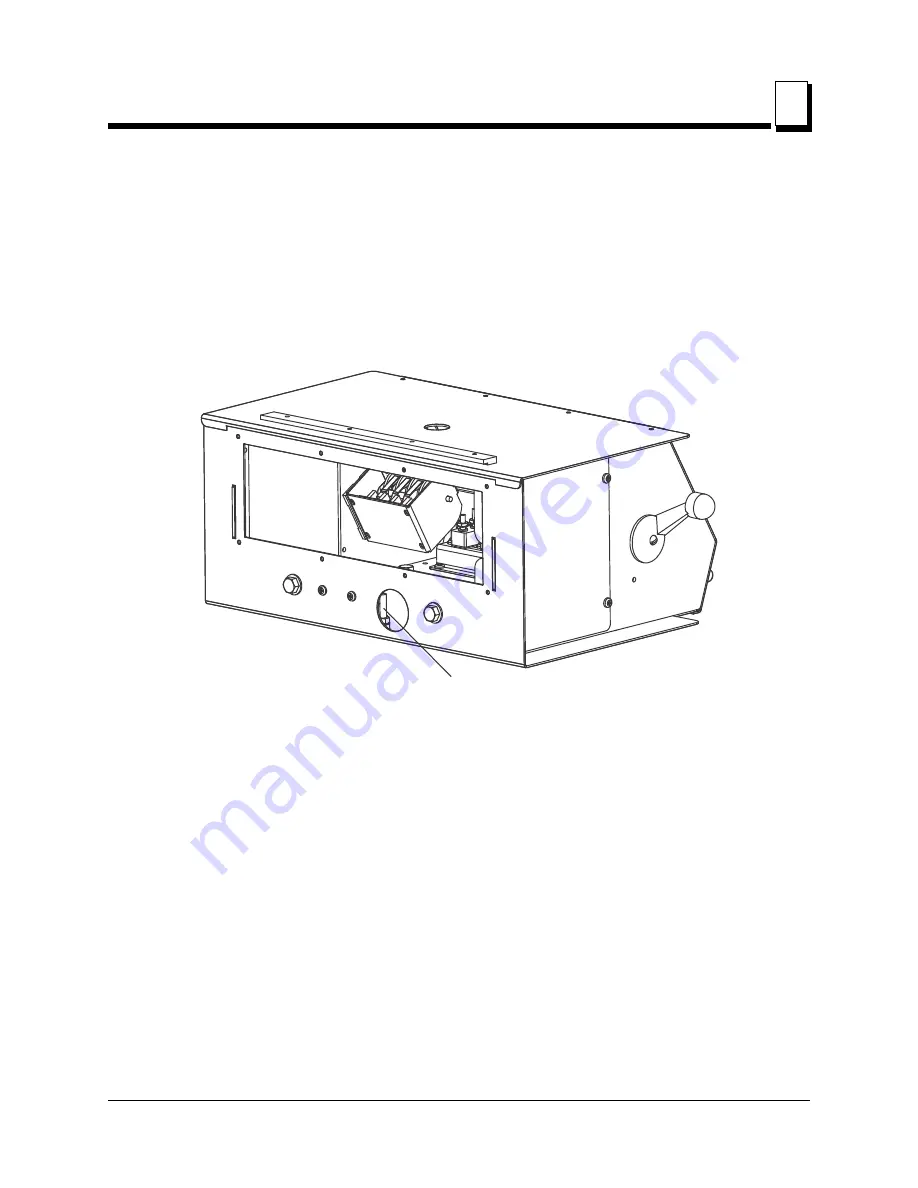
Installation Procedure
Accuset Final Installation
Installation Procedure
AS00doc032519
1-29
1
1.7
Accuset Final Installation
See Figure 1-27.
1.
Remove the existing 1/4-20 self-locking nut and flat washer which secure the existing
wires on the back ground stud at the rear of the control box. Install the provided black wire
labeled GND to the ground stud and replace the washer and self-locking nut. Tighten the
nut securely.
2.
Route the free ends of the black and red MOTOR wires, black GND wire and the red
12VDC wire through the hole in the top of the control box.
3.
Temporarily place the Accuset control upright on top of the sawmill control box. Leave all
pre-installed Accuset wires connected.
4.
Route the black Accuset wire labeled DRUM UP and the red Accuset wire labeled DRUM
DN through the hole in the top of the sawmill control box.
FIG. 1-27
3H0849-7
Back Ground Stud