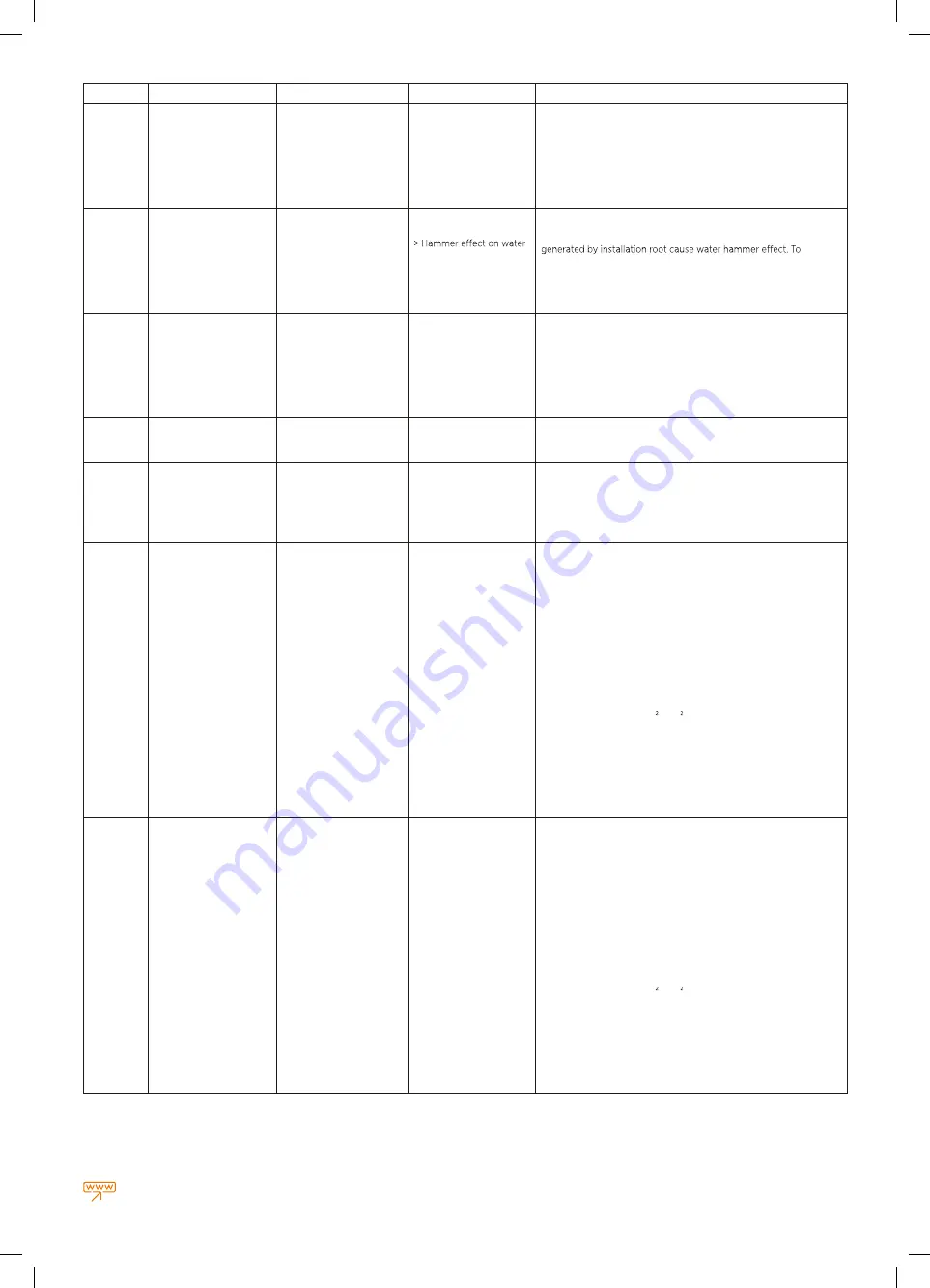
61
warmhaus.co.uk
Error Code
Description of the Error
Malfunction
Probable Cause
Solution(s)
E 43
Opentherm
communication error
Boiler does not work, E43
error code flashing on the
screen after 1 minute of
communucation error
Opentherm line
disconnected
1-) Remove energy from boiler and re energised E43 will be removed
and boiler & buttons will get back to funcitional
2-) Replace the room unit batteries with the fresh ones and reset from
room unit
3-) Check cabeling between boiler and room thermostat unit and re
connect if any disconnection, if connection set up succesfully then
connection symbol will be activated on the screen
4-) Call for authorised service to re connect openterm connection
rE 44
Cumulated intermittent
ignition without reaching
burner ignition.
Boiler does not work, E44
error code flashing on the
screen
"> Intermittent contacts on
harness
net
> Too many request from
in shotr time from out side
room units or thermosad
bridge etc. "
1-) Call For service
2-) Check for domestic heating water net this problem generally
eliminate this adjust P26=2 or 3 on TsP Menu
3-) Check intermittent contacts on harness carefully
4-) Check room unit or thermostad bridge againt too many request
in short time
E 62
Calibration request
Boiler does not work, E62
error code flashing on the
screen
"> Calibration not done
> Replacing board but not
service key from the board
dismantled
> Service key damaged or
disconnected
> Updating Software
( probable )"
1-) Call For service
2-) Check TsP default values before calibration specially P15, P31, P32,
P33
2-) Perform Auto Calibration.
Attention: Only authorised service must perform Au-To
calibration
E 72
Delta T heating at ignition
not occurred
Boiler does not work, E72
error code flashing on the
screen
> FLOW OR RETURN
Sensor not on position
1-) Call for authorised service at first
2-) Check RETURN and FLOW sensor on position.
E 74
Second CH temperature
Probe faulty
Boiler does not work, E74
error code flashing on the
screen
> FLOW and LIMIT Sensor
( double NTC ) faulty
1-) Call for authorised service at first
2-) Check CH temperature probe ressistance (double CH NTC probe
is used as high temperature limit device) if its out of tolerance replace
double NTC
3-) Check cabeling and connectors between double NTC and board
4-) Reset & Restart boiler
E 77
Absolute current values
reached
Boiler does not work, E77
error code flashing on the
screen
> Gas inlet pressure
> Aging or rust on the
electrode
> Recirculation on fluegas
path
> Blokage on flue or wrong
flue
> Electrode position
> Cabeling disconnections
> Combustion calibration
> Electronic board
> Gas valve failiure
1-) Call for authorised service at first
2-) Check gas supply pressure must be 20-17 mbar. Gas pressure must
be in between on this values while boiler on operational
3-) Check wrong flue OR flue gas blockage
4-) Check recirculation ( flue gas leak ) from flue gas path to fresh air
side, check flue gas sealings specially
5-) Check any problems on the ionisation electrode, (like
condensation, rust etc.), and control poistioning of the electrode, if
electrode poistion wrong calibrate electrode.
6-) Check if the heat exchanger coils clogged or not
7-) Check for condensation on the cabling AND/OR on board
8-) Check earth connection between board and electrode
9-) Check electrode cabeling between board and electrode
10-) Check combustion CO or O values on HI and LO mode at
sweeper mode.
11-) Perform Auto Calibration.
12-) If fault still persists Replace board, but use original service key
from the board dismantled to keep original parameters and calibration
points. If original service key not used aslo adjust P15 releated to the
default value of boiler power and perform Au-To calibration.
13-) If not successfull replace gas valve, and Perform Au-To calibration.
Attention: Only authorised service must perform Au-To calibration
E 78
Max regulation current
value reached
Boiler does not work, E78
error code flashing on the
screen
> Gas inlet pressure
> Aging or rust on the
electrode
> Recirculation on fluegas
path
> Blokage on flue or wrong
flue
> Electrode position
> Cabeling disconnections
> Combustion calibration
> Electronic board
> Gas valve failiure
1-) Call for authorised service at first
2-) Check gas supply pressure must be 20-17 mbar. Gas pressure must
be in between on this values while boiler on operational
3-) Check wrong flue OR flue gas blockage
4-) Check recirculation ( flue gas leak ) from flue gas path to fresh air
side, check flue gas sealings specially
5-) Check any problems on the ionisation electrode, (like
condensation, rust etc.), and control poistioning of the electrode, if
electrode poistion wrong calibrate electrode.
6-) Check if the heat exchanger coils clogged or not
7-) Check for condensation on the cabling AND/OR on board
8-) Check earth connection between board and electrode
9-) Check electrode cabeling between board and electrode
10-) Check combustion CO or O values on HI and LO mode at
sweeper mode.
11-) Perform Auto Calibration.
12-) If fault still persists Replace board, but use original service key
from the board dismantled to keep original parameters and calibration
points. If original service key not used aslo adjust P15 releated to the
default value of boiler power and perform Au-To calibration.
13-) if not successfull replace valve, and Perform Au-To calibration.
Attention: Only authorised service must perform Au-To calibration
Содержание EWA 2525C
Страница 1: ...CONDENSING COMBI BOILERS INSTALLATION SERVICE MANUAL EWA 2525C 25 kW EWA 2530C 30 kW...
Страница 2: ......
Страница 3: ...3 warmhaus co uk...
Страница 28: ...28 warmhaus co uk 3 16 Ewa Combi Boiler Wiring Diagram Wiring Diagram RISK OF ELECTRIC SHOCK 0100_00 W211130...
Страница 57: ...57 warmhaus co uk...