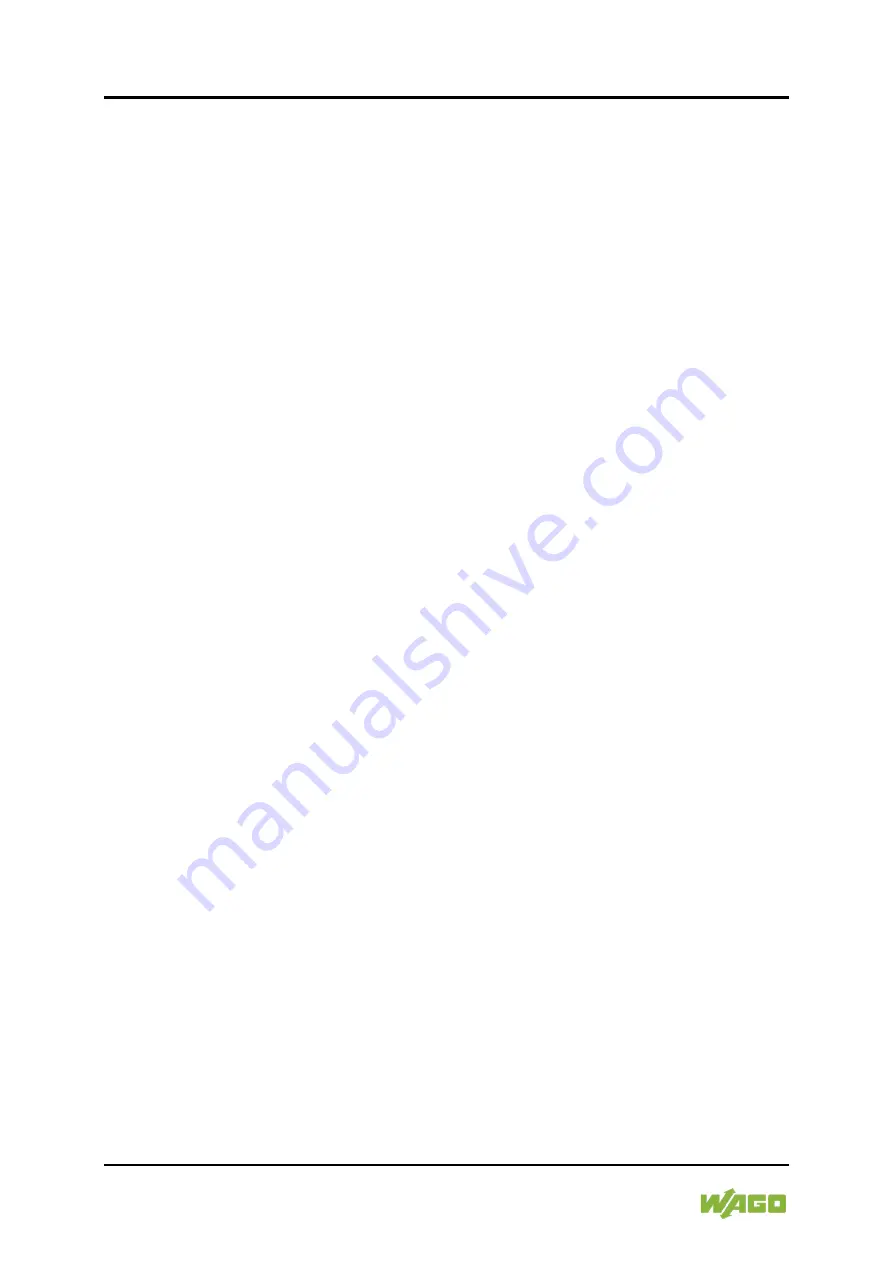
176 List of Figures
WAGO-I/O-SYSTEM 750
750-325 CC-Link Fieldbus Coupler
Manual
Version 2.0.1
List of Figures
Figure 2: Marking Area for Serial Numbers ........................................................18
Figure 5: Isolation for Fieldbus Couplers/Controllers (Example) .........................22
Figure 6: System Supply via Fieldbus Coupler/Controller (left) and via Internal
System Supply Module (right) ...................................................................23
Figure 7: System Voltage for Standard Couplers/Controllers and Extended
Figure 8: Field Supply for Standard Couplers/Controllers and Extended ECO
Figure 9: Supply Module with Fuse Carrier (Example 750-610) ..........................30
Figure 11: Opening the Fuse Carrier and Changing the Fuse ............................31
Figure 12: Changing the Fuse and Closing the Fuse Carrier ..............................32
Figure 14: Fuse Modules for Automotive Fuses, Series 282...............................33
Figure 15: Fuse Modules for Automotive Fuses, Series 2006 .............................33
Figure 16: Fuse Modules with Pivotable Fuse Carrier, Series 281 .....................33
Figure 17: Fuse Modules with Pivotable Fuse Carrier, Series 2002....................34
Figure 19: Supply Example for Standard Couplers/Controllers ...........................36
Figure 21: Cable Shield at Ground Potential ......................................................41
Figure 22: Examples of the WAGO Shield Connecting System ..........................42
Figure 23: Application of the WAGO Shield Connecting System ........................42
Figure 24: View Fieldbus Coupler CC-
V 2.0 ................................................44
Figure 26: Fieldbus connections, Series 231 (MCS) ...........................................47
Figure 28: Service Interface (Closed and Opened Flap) .....................................49
Figure 29: Rotary Encoder Switch Station Address ............................................50
Figure 32: Release Tab of Extended ECO Fieldbus Coupler (Example) .............65
Figure 34: Snap the I/O Module into Place (Example) ........................................66
Figure 35: Removing the I/O Module (Example) .................................................67
Figure 37: Example for the Arrangement of Power Contacts ..............................69
Figure 38: Connecting a Conductor to a CAGE CLAMP
...................................70
Figure 40: 750-325750-325Memory Areas and Data Exchange for a Fieldbus
Figure 41: Timing Diagram for the Initial Data Transfer Handshake ...................93
Figure 42: Timing Diagram for the Error Handshake ..........................................94