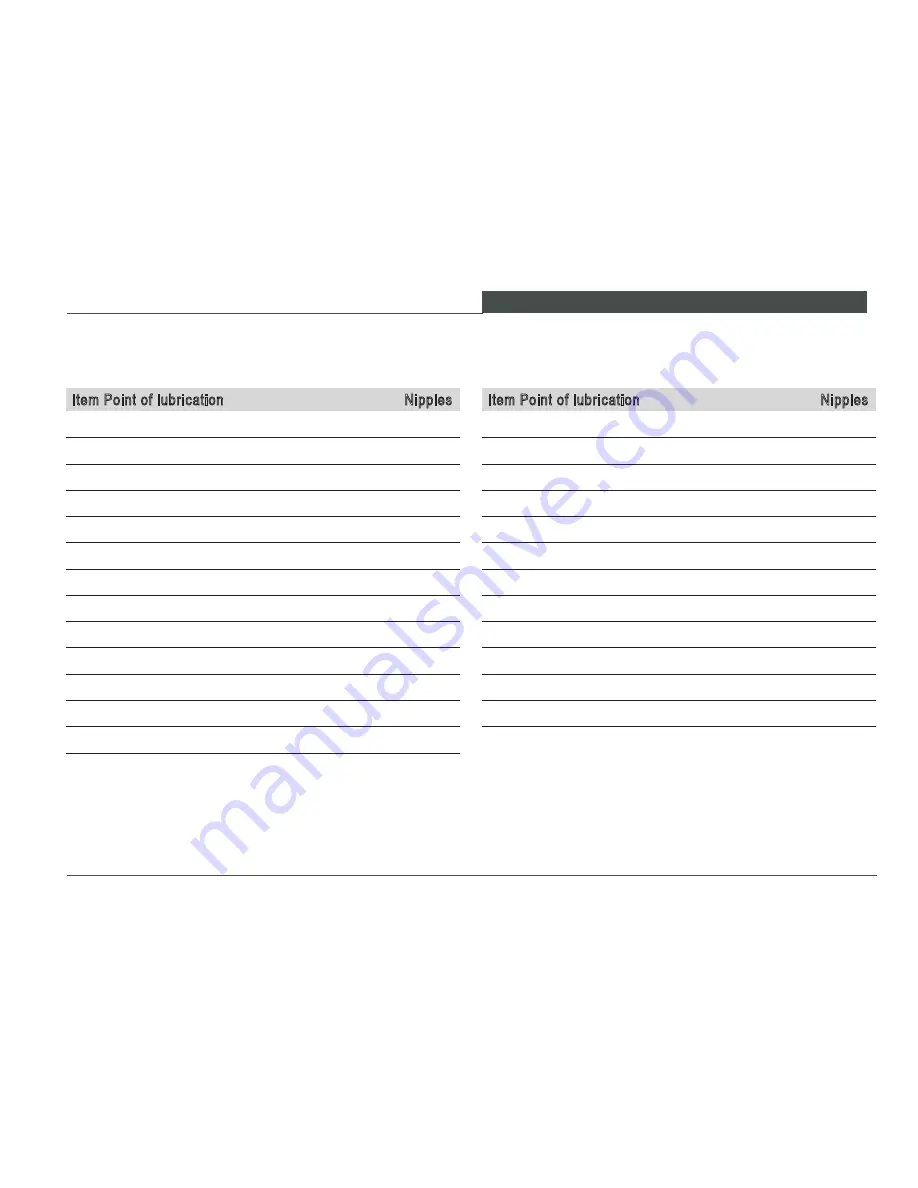
SE RVICING A ND INSPEC TION
159
W L 50
Item Point of lubrication Nipples
13 Bearing for reversing lever
[1]
14 Tie rod, front
[1]
15 Cab tipping cylinder (under the cab)
[2]
16 Drive shaft, rear
[1]
17 Center pivot bearing, top (remote lubrication)
[1]
18 Steering cylinder, rear (remote lubrication)
[1]
19 Center pivot lager, bottom
[1]
20 Steering cylinder, front
[1]
21 Drive shaft, front
[1]
22 Tie rod, rear
[1]
23 Pivot point of tool attachment
[2]
24 Tool locking bolts
[2]
Item Point of lubrication Nipples
1
Engine enclosure hinges
[2]
2
Cab tilting hinge, rear
[1]
3
Door hinges
[4]
4
Brake pedal bearing (in the cab)
[1]
Brake lever bearing (under the cab)
[1]
5
Accelerator (in the cab)
[1]
6
Cab tilting hinge, front
[1]
7
Center pivot bearing, top
[1]
8
Lifting cylinder, rear
[2]
9
Arm, top
[2]
10 Tipping cylinder, rear
[1]
11 Lifting cylinder, front
[2]
12 Tipping cylinder, front
[1]
Lubricate all the points of lubrication daily with water-resistant multi-purpose grease. Lubricate all other moving parts
such as the handbrake lever, foot pedals, cables, etc. using the oil can.
Содержание WL 50
Страница 1: ...Operator s Manual Wheel Loader WL 50 www wackerneuson com...
Страница 2: ...December 08 Edition...
Страница 46: ...TECHNICAL DATA 44 Dimensions 3 4 Dimensions Fig 11...
Страница 103: ...Operating and operation 101 WL50 Fig 46 Switch for differen tial lock 1 12V 1...
Страница 123: ...Operating and operation 121 WL50...
Страница 134: ...Towing and transporting 132 Fig 66 Tying down the loader...
Страница 169: ...SERVICING AND INSPECTION 167 WL50 Fig 72 Position of the cab mounting bolts Fig 73 Tilting the cab 1 2 3...
Страница 243: ...Appendix 241 WL50 For personal notes...
Страница 253: ...List of figures 251 WL50...