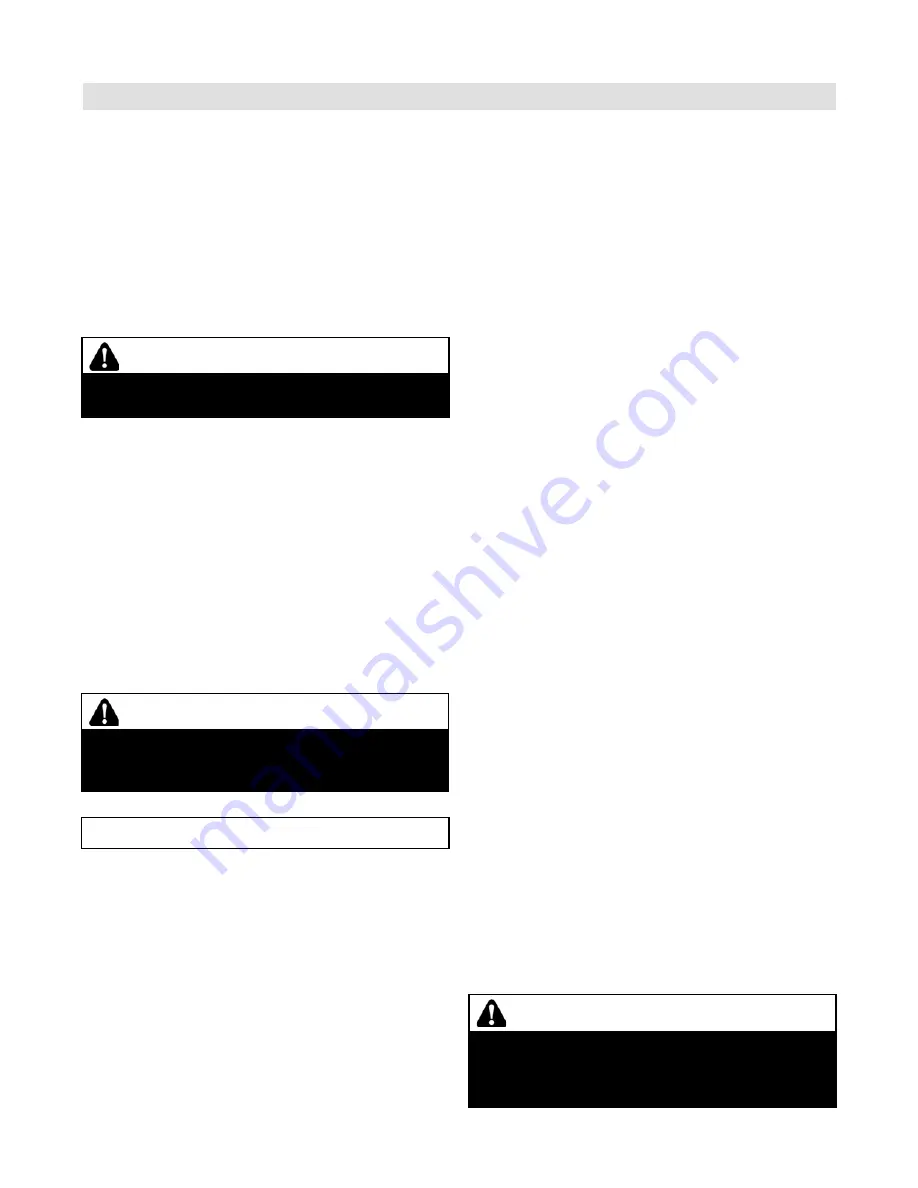
Vitodens 200-W B2HA 112, 150 Service
5683 710 - 09
10
Mechanical Room
General Information
During the early stages of designing a new home, we recommend that proper consideration be given to constructing a
separate mechanical room dedicated to the gas- or oil-fired heating equipment and domestic hot water storage tank(s).
The boiler must be located in a heated indoor area, near a floor drain, and as close as possible to a wall. Whenever
possible, install the boiler near an outside wall so that it is easy to duct the venting system to the boiler.
Locate the boiler on a wall capable of supporting the weight of the boiler filled with water (see section entitled
“Technical Data” on page 98 for information required for total boiler weight calculation). Ensure that the boiler location
does not interfere with the proper circulation of combustion and ventilation air of other fuel burning equipment within
the mechanical room (if applicable).
The maximum room temperature of the mechanical room where the boiler is located must not exceed 104ºF (40ºC).
H
Ensure ambient temperatures are higher than 32°F
(0°C) and lower than 104°F (40°C).
H
Prevent the air from becoming contaminated by
halogenated hydrocarbons (e.g. as contained in paint
solvents or cleaning fluids) and excessive dust (e.g.
through grinding or polishing work). Combustion air
for the heating process, and ventilation of the boiler
room must be free of corrosive contaminants. To that
end, any boiler must be installed in an area that has no
chemical exposure. The list to the right indicates the
main, currently known sources.
H
Avoid continuously high levels of humidity (e.g. through
frequent drying of laundry).
H
Never close existing ventilation openings.
Sources of combustion and ventilation air contaminants
Areas likely to contain contaminants:
H
New building construction
H
Swimming pools
H
Remodelling areas, hobby rooms
H
Garages with workshops
H
Furniture refinishing areas
H
Dry cleaning/laundry areas and establishments
H
Auto body shops
H
Refrigeration repair shops
H
Metal fabrication plants
H
Plastic manufacturing plants
H
Photo processing plants
H
Beauty salons
Products containing contaminants:
H
Chlorine-type bleaches, detergents and cleaning
solvents found in household laundry rooms
H
Paint and varnish removers
H
Hydrochloric acid, muriatic acid
H
Chlorine-based swimming pool chemicals
H
Spray cans containing chlorofluorocarbons
H
Chlorinated waxes and cleaners
H
Cements and glues
H
Refrigerant leaks
H
Calcium chloride used for thawing
H
Sodium chloride used for water softening salt
H
Permanent wave solutions
H
Adhesives used to fasten building products and other
similar items
H
Antistatic fabric softeners used in clothes dryers
Boiler operation in marine environments (damp, salty
coastal areas)
WARNING
If you notice fire coming from the appliance, call the fire
department immediately! Do not attempt to extinguish
the fire unless qualified to do so.
WARNING
Fire causes a risk of burns and explosion!
H
Shut down the boiler
H
Close fuel shut-off valves
H
Use a tested fire extinguisher, class ABC.
IMPORTANT
The service life of the boiler’s exposed metallic surfaces,
such as the casing and fan housing, is directly influenced
by proximity to damp and salty marine environments. In
such areas, higher concentration levels of chlorides from
sea spray, coupled with relative humidity, can lead to
degradation of the exposed metallic surfaces mentioned
above. Therefore, it is imperative that boilers installed
in such environments not be installed using direct vent
systems which draw outdoor air for combustion. Such
boilers must be installed using room air dependent vent
systems; i.e. using room air for combustion. The indoor
air will have a much lower relative humidity and, hence,
potential corrosion will be minimized.
Installation area conditions
WARNING
Incorrect ambient conditions can lead to damage to the
heating system and put safe operation at risk.