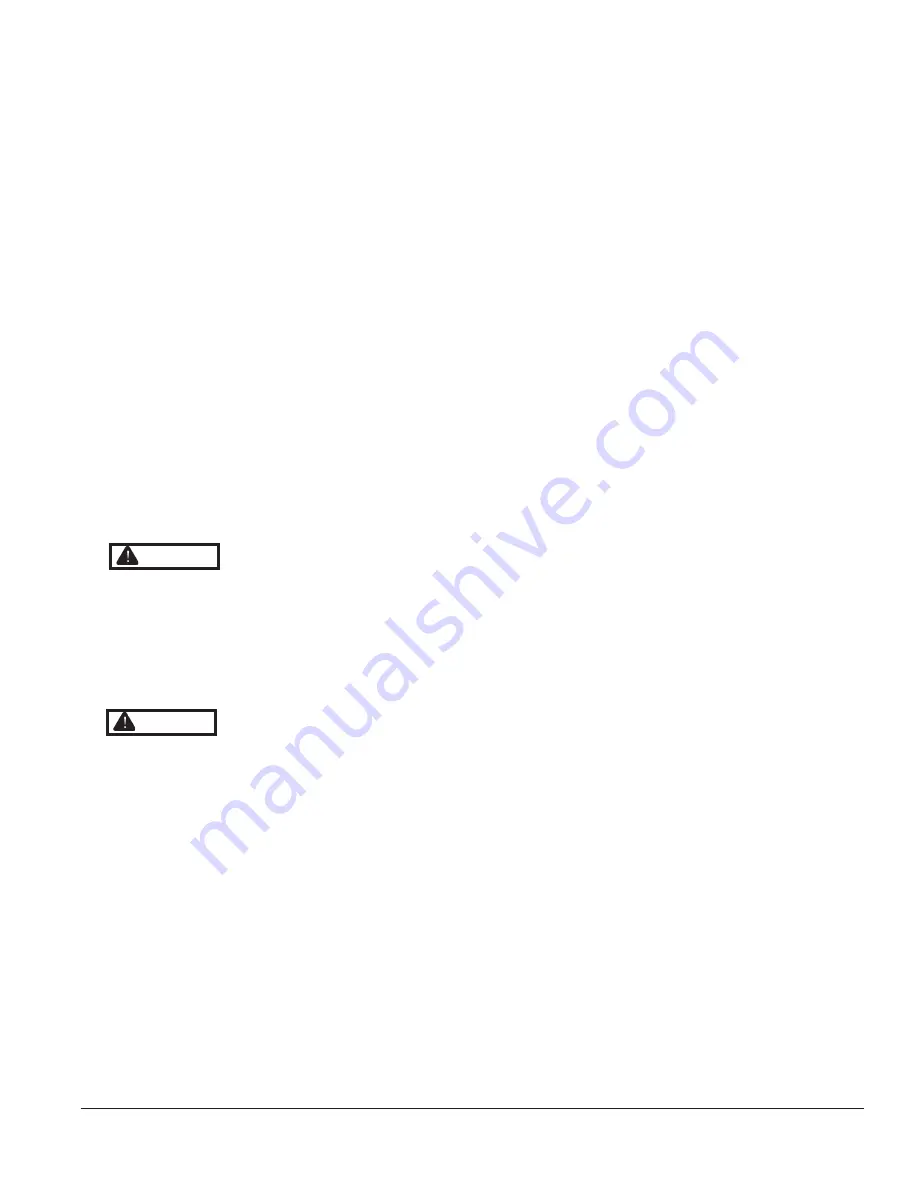
129
107774-02- 4/18
i.
Unplug the ignition, ground, and flame rod wires
from the ignition electrode and the flame rod (Figure
14.1).
j.
Use a 10 mm wrench to remove the four nuts
securing the fire door to the heat exchanger (Figure
14.1). Carefully remove the door/blower/gas valve assembly from the heat exchanger, being careful
not to damage the refractory insulation on the inside of the door (see Refractory Warning on next page)
or
the
electrodes.
k.
Inspect the heat exchanger combustion chamber and vacuum
any debris found on the coil surfaces.
If necessary, the coils may be brushed with a nonabrasive, nonmetallic brush. Do not use cleaning
agents, solvents, acid or alkali products of any type to clean the heat exchanger .
l.
Inspect the target wall and fire door insulation
.
If either shows signs of damage, it must be replaced.
m.
Inspect the burner for heat damage
or other deterioration. Use a non-metallic brush or source of
compressed air to clean off dust or debris from ports.
n.
Inspect the ignition electrode and flame rod
for deposits. Clean any found with steel wool. Do not
use sand paper or Emory cloth for this cleaning. Inspect the ceramic portion of both of these parts for
cracks and replace if any are found. Verify that the ignition electrode gap is within the range shown in
Figure
14.2.
o.
Inspect the blower gas valve assembly
, looking for dust, lint, or other debris that may have been
drawn into this assembly. Excessive deposits may be vacuumed out. Verify that “flappers” in venturi
move freely. Inspect all rubber and plastic components on the blower/gas valve assembly, looking for
deterioration. Replace blower and/or gas valve if deterioration is found.
p
.
Inspect and clean the condensate trap
.
Place a bucket under the condensate cleanout cap on the
bottom of the boiler (see Figure 2.1) to catch water in the trap as well as the ball and ball support.
Unscrew the cap, being careful not to lose the ball or ball support. Flush any debris found in the trap
with water – do not use other cleaning agents. Reassemble the trap as shown in Figure 14.3.
q.
Reinstall the fire door/blower/gas valve assembly
,
following the above steps in reverse order.
r.
Inspect the vent system to verify that
:
• All gaskets and joints between the boiler heat exchanger and terminal are leak tight.
• All supports are intact and vent system is properly pitched
• All pipe is in good condition. Look for damage such as cracks, heat distortion, discoloration, and
embrittlement. If any such damage is found, the pipe must be replaced and the cause of the
damage
identified.
• Vent/Intake terminals are in good condition, free from blockages, and still correctly located relative to
doors,
windows,
decks,
etc.
• There is no gasoline, flammable liquids/vapors, or halogen based products stored in the vicinity of
the vent or inlet terminals. Also verify that there are no chemical products containing chlorine,
chloride based salts, chlorofluorocarbons, paint removers, cleaning solvents, or detergents stored
near the air intake terminal.
XIV. Service and Maintenance
(continued)
WARNING Asphyxiation Hazard. Do not operate the boiler without the ball and ball support in
place. Doing so could result in flue gas leakage into the indoors resulting in personal injury or death from
Carbon Monoxide (CO) poisoning.
NOTICE
Attempting to clean the heat exchanger or trap with anything other than water could result in
condensate backup, causing the boiler to shut-down.
CAUTION Do not over tighten fire door mounting nuts. Doing so could break the fire door mounting
studs. If any of these studs are damaged, the heat exchanger must be replaced. Use of a short 10 mm box
wrench will reduce the risk of damaging these studs.
Содержание K2WTC-135
Страница 10: ...10 107774 02 4 18 Figure 4 1 Minimum Clearances To Combustible Construction IV Locating the Boiler continued...
Страница 12: ...12 107774 02 4 18 Figure 5 1 Wall Layout Mounting Hole Location V Mounting The Boiler continued...
Страница 74: ...74 107774 02 4 18 Figure 9 2 Piping Method 1 Near Boiler Piping Heating Only IX System Piping continued...
Страница 76: ...76 107774 02 4 18 Figure 9 5 Piping Method 1 Near Boiler Piping Shaded Boiler Loop IX System Piping continued...
Страница 81: ...81 107774 02 4 18 X Domestic Hot Water Piping continued Figure 10 1 Domestic Hot Water Piping...
Страница 87: ...87 107774 02 4 18 Figure 11 6 J3 Field Wiring Figure 11 5 4 20 mA EMS Field Wiring XI Wiring continued...
Страница 89: ...89 107774 02 4 18 XI Wiring continued...
Страница 90: ...90 107774 02 4 18 Figure 11 8 Internal Wiring Connections Diagram XI Wiring continued...
Страница 92: ...92 107774 02 4 18 Figure 11 9 TACO SR504 or Equivalent Zone Panel Wiring Connection Diagram XI Wiring continued...
Страница 93: ...93 107774 02 4 18 Figure 11 10 Sage Zone Control Circulator Panel Wiring Connection Diagram XI Wiring continued...
Страница 101: ...101 107774 02 4 18 Lighting and Operating Instructions XII Start Up and Checkout continued...
Страница 142: ...142 107774 02 4 18 XVI Repair Parts continued...
Страница 145: ...145 107774 02 4 18 XVI Repair Parts continued...
Страница 148: ...148 107774 02 4 18 XVI Repair Parts continued...
Страница 150: ...150 107774 02 4 18 XVI Repair Parts continued...
Страница 152: ...152 107774 02 4 18 XVI Repair Parts continued 120 121 122 123 124 125 126 127...
Страница 159: ...159 107774 02 4 18 SERVICE RECORD DATE SERVICE PERFORMED...
Страница 160: ...160 107774 02 4 18 U S Boiler Company Inc P O Box 3020 Lancaster PA 17604 1 888 432 8887 www usboiler net...