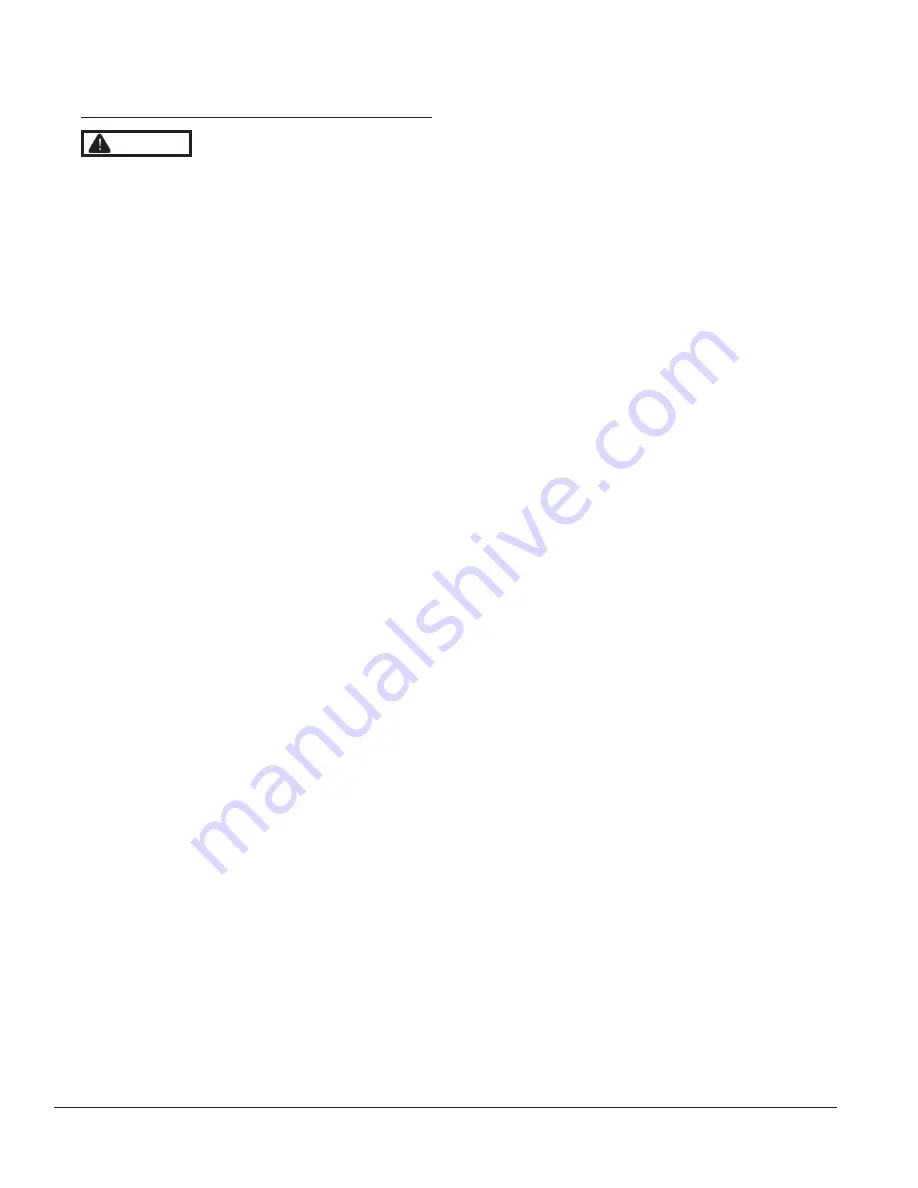
56
107774-02 - 4/18
VII. Venting
F. Assy of DuraVent PolyPro & G. Selkirk Polyflue Vent Systems (continued)
8. Installations using PolyPro-flex (Vent Options 9 & 15):
Refer to DuraVent PolyPro flex Instructions for assembly of all flex components including the chimney cap and
the adaptor to rigid PolyPro at the base of the masonry or B vent chimney. In addition, observe the following
requirements:
a. Refer to the appropriate Vent option in Tables 7.13b or 7.21 for a list of the principle flex components
required. Rigid vent pipe by the same manufacturer will also be required for the run from the boiler to the
base of chimney.
b. Masonry chimneys cannot be used for an air chase
c. B vent chimneys can only be used for an air chase (Vent option 9) if the B vent has the minimum size shown
in Table 7.13b and is fully accessible for sealing of all joints and seams.
d. When Vent Option 9 is used, install a Tee on the base of the B-vent that is the same size as the B- Vent
chimney. Install the PolyPro Lower B–Vent adaptor in the base of this Tee as described in the DuraVent
PolyPro Flex instructions.
Connection of the PVC air intake pipe to the side outlet of the tee is made using a cap and a PVC socket
x male thread adaptor. Cut a clearance hole in the cap for the male threads. Secure the adaptor to the cap
using a 3” electrical conduit lock nut. Seal all joints with RTV.
G. Assembly of Selkirk Polyflue Vent Systems
1. This boiler has been approved for use with the Selkirk Polyflue single wall Polypropylene vent system to be
provided by the installer.
2. Assemble the vent system, starting at the boiler:
a. The vent adaptor has three different inside diameters. The middle inside diameter accepts 3” nominal Polyflue
(Figure 7.27). A locking band clamp in the adaptor prevents the vent pipe from coming out of the adaptor
once it is installed and tightened. Lubricate the gaskets in the vent adaptor with mild soapy water and insert
the first piece of 3” Polyflue into the adaptor until it bottoms out. Tighten locking band clamp to secure vent
pipe.
b. Assemble the next piece of 3” Polyflue.
c. For each joint, verify that the gasket is evenly seated in the bell (female) end of the pipe. Lubricate this gasket
with mild soapy water. Slide a Pipe Locking Band over the male end of the pipe to be joined as shown in
Figure 7.41. Push the male end of the next section of pipe into the bell until it bottoms out, then back out 1/8—
1/4” to provide room for thermal expansion. Slide pipe locking band over the female end of the connections
and tighten both hose clamps.
d. Assemble the rest of the vent system per the manufacturer’s installation instructions, being sure to pitch
horizontal sections back towards the boiler 5/8” per ft.
WARNING Asphyxiation Hazard. When using PolyPro flex, observe the following precautions:
• PolyPro flex may be damaged by handling at low temperatures. Do not bend, uncoil, or attempt to install
if it has been stored at a temperature below 42°F without allowing it to warm to a higher temperature
first.
• Do not bend PolyPro flex more than 45°.
• Instructions below reference the DuraVent PolyPro Flex instruction manual. Not all vent
configurations shown in the DuraVent manual are approved for use with this boiler.
Содержание K2WTC-135
Страница 10: ...10 107774 02 4 18 Figure 4 1 Minimum Clearances To Combustible Construction IV Locating the Boiler continued...
Страница 12: ...12 107774 02 4 18 Figure 5 1 Wall Layout Mounting Hole Location V Mounting The Boiler continued...
Страница 74: ...74 107774 02 4 18 Figure 9 2 Piping Method 1 Near Boiler Piping Heating Only IX System Piping continued...
Страница 76: ...76 107774 02 4 18 Figure 9 5 Piping Method 1 Near Boiler Piping Shaded Boiler Loop IX System Piping continued...
Страница 81: ...81 107774 02 4 18 X Domestic Hot Water Piping continued Figure 10 1 Domestic Hot Water Piping...
Страница 87: ...87 107774 02 4 18 Figure 11 6 J3 Field Wiring Figure 11 5 4 20 mA EMS Field Wiring XI Wiring continued...
Страница 89: ...89 107774 02 4 18 XI Wiring continued...
Страница 90: ...90 107774 02 4 18 Figure 11 8 Internal Wiring Connections Diagram XI Wiring continued...
Страница 92: ...92 107774 02 4 18 Figure 11 9 TACO SR504 or Equivalent Zone Panel Wiring Connection Diagram XI Wiring continued...
Страница 93: ...93 107774 02 4 18 Figure 11 10 Sage Zone Control Circulator Panel Wiring Connection Diagram XI Wiring continued...
Страница 101: ...101 107774 02 4 18 Lighting and Operating Instructions XII Start Up and Checkout continued...
Страница 142: ...142 107774 02 4 18 XVI Repair Parts continued...
Страница 145: ...145 107774 02 4 18 XVI Repair Parts continued...
Страница 148: ...148 107774 02 4 18 XVI Repair Parts continued...
Страница 150: ...150 107774 02 4 18 XVI Repair Parts continued...
Страница 152: ...152 107774 02 4 18 XVI Repair Parts continued 120 121 122 123 124 125 126 127...
Страница 159: ...159 107774 02 4 18 SERVICE RECORD DATE SERVICE PERFORMED...
Страница 160: ...160 107774 02 4 18 U S Boiler Company Inc P O Box 3020 Lancaster PA 17604 1 888 432 8887 www usboiler net...