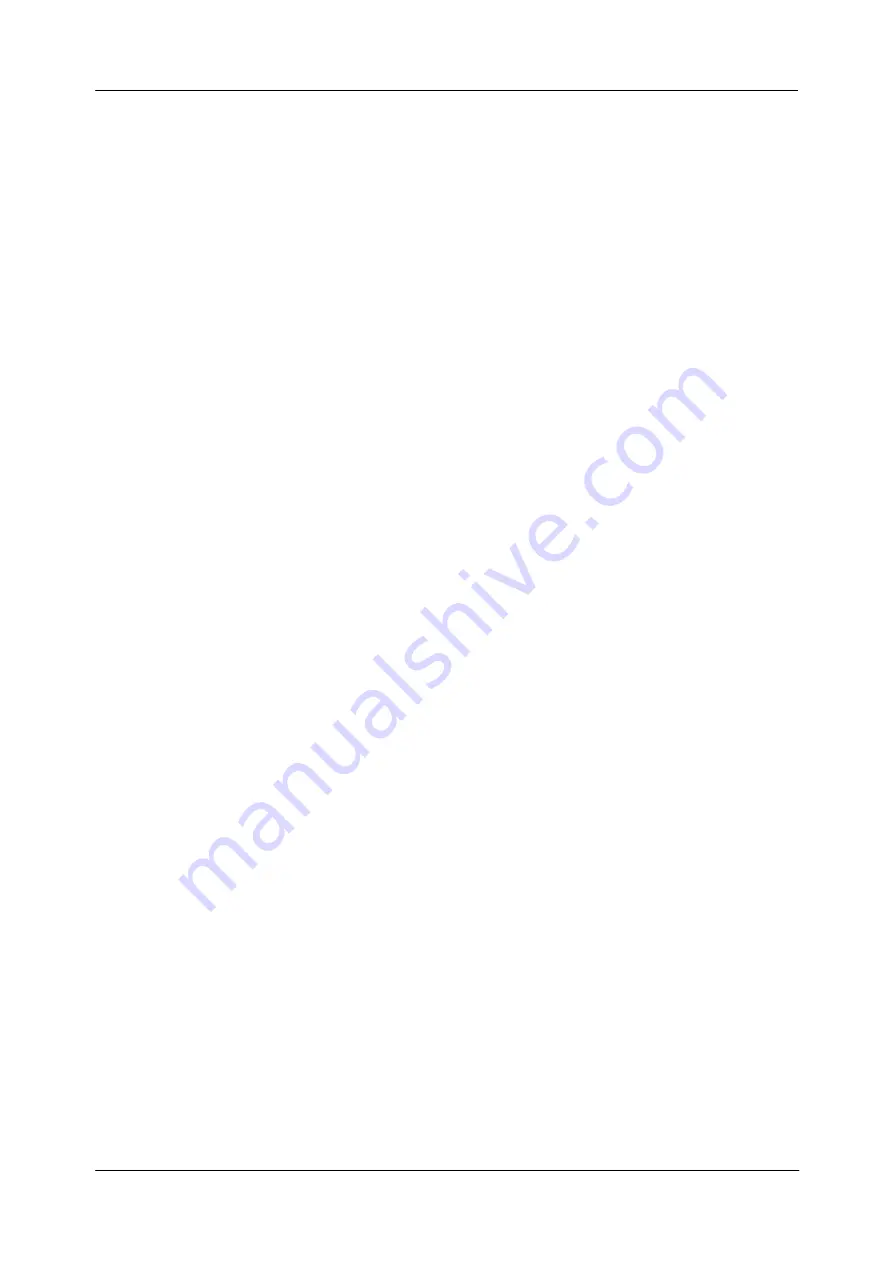
Section 10
—
Troubleshooting
VC350A Flexoseal
®
System
Valco Cincinnati
10-16
2. If the “ENC” LEDS (D4 and D11) do not illuminate and the “SCAN” LED does not blink, replace the main
board.
3. If the “RATIO” LED (D10) does not illuminate, do the following:
3a. Ensure that the U9 chip is firmly seated in the socket.
3b. Ensure that there is a “Ratio Comp” setting on switches SW3-SW7 (e.g., 1.0000).
3c. Ensure that JP2 is selected either for “STD” mode or for “ENB-500”.
3d. Check for ON/OFF comp setting at DS1 and DS2 (or P1, P2). (A minimum of .5 ms should be
selected.)
3e. If the “RATIO” LED (D10) still does not illuminate, replace the main board.
4. Return the “ENC” and “SCAN” switches to the down (external mode) position, and reconnect the valve
connectors at the valve driver board.
5. Run the parent machine above minimum speed. Again, the “ENC” LEDs (D4 and D11) should illuminate,
the “SCAN” LED should blink, and the “RATIO” LED (D10) should illuminate.
6. If the LEDs operated properly in the test (“TST”) mode, but not in the external mode, do the following:
6a. Check the interface ribbon cable at J1 on the interface board and J2 on the main board.
6b. Ensure that the encoder and scanner cable connectors on the interface board are properly seated.
6c. Check the external encoder and scanner cables.
6d. Check the encoder (see
Encoder Diagnostics
in this section).
6e. Check the scanner and mounting (see
Scanner Diagnostics
in this section).
Note!
Scanner and encoder problems can be isolated by selecting either SW12-1 or SW12-2.
7. If all of the components in step 6 are working, ensure that the “FLAP” LED (D6) and the “GLUE” LED
(D8) are flashing.
8. Turn on the “GUN1” selector switch (it should illuminate), and check to see if the “GUN1” LED (D14)
and the “GLUE” LED (D8) flash. If they do not flash, check the “GUN1” selector switch connector at J5
on the main board.
9. Ensure that the “PEAK” and the “HOLD” LEDs on the valve driver board are flashing.
9a. If they are not flashing, check the ribbon cable to the valve driver.
9b. If they still are not flashing, replace the valve driver board.
10. If any of steps 7, 8, or 9 fail, disconnect the valve connectors at the valve driver board, set the ‘ENC” and
the “SCAN” switches back to the up (“TST”) position, and see if LEDs are operating properly in the test
mode.
11. If the LEDs do not operate properly in either the test or the external-mode positions, recheck the settings on
DS1 and DS2 to ensure that ON/OFF comp is at the minimum setting:
11a. Using a DVM, measure between TP5 (Reset) and TP5 (gnd). This measurement should be +5V. If
measurement is not +5V, replace the main board.
12. If the LEDs operate properly in the test mode but not in the external mode, ensure that the minimum speed
is set properly. Also verify that all internal cables are properly seated in the connectors, and not kinked or
pinched between components.
Содержание VC350A
Страница 1: ...VC350A Flexoseal System Manual Number MC037 Release Date May 2001 ...
Страница 8: ...Section 1 Introduction VC350A Flexoseal System Valco Cincinnati 1 2 Figure 1 1 VC350A Control ...
Страница 68: ...Section 9 Maintenance VC350A Flexoseal System Valco Cincinnati 9 9 Figure 9 4 Fluid Regulator ...
Страница 79: ...Section 10 Troubleshooting VC350A Flexoseal System Valco Cincinnati 10 9 Figure 10 2 No Glue Flowchart ...
Страница 95: ...Section 12 Part Number List VC350A Flexoseal System Valco Cincinnati 12 6 Shaft Encoder Assembly 155xx001 ...
Страница 105: ...Section 12 Part Number List VC350A Flexoseal System Valco Cincinnati 12 16 Mounting Bracket Assembly 578xx530 ...
Страница 107: ...Section 12 Part Number List VC350A Flexoseal System Valco Cincinnati 12 18 Scanner Mounting Bracket Assembly 581xx157 ...
Страница 113: ...Section 12 Part Number List VC350A Flexoseal System Valco Cincinnati 12 24 Glue Station Top Down Tab Side 578xx644 ...
Страница 115: ...Section 12 Part Number List VC350A Flexoseal System Valco Cincinnati 12 26 Glue Station Bottom Up Tab Side 578xx649 ...
Страница 117: ...Section 12 Part Number List VC350A Flexoseal System Valco Cincinnati 12 28 Conversion Kit Assembly 723xx003 ...
Страница 119: ...Section 12 Part Number List VC350A Flexoseal System Valco Cincinnati 12 30 3 Way valve 12VDC 411xx751 ...
Страница 127: ...Section 12 Part Number List VC350A Flexoseal System Valco Cincinnati 12 38 LP366WGT Low Pressure Glue Valve 705xx112 ...
Страница 129: ...Section 12 Part Number List VC350A Flexoseal System Valco Cincinnati 12 40 0 40 mm 0 016 Zoll 08 Glue Valve 703xx907 ...
Страница 131: ...Section 12 Part Number List VC350A Flexoseal System Valco Cincinnati 12 42 366 Glue Valve Assembly 706xx051 ...
Страница 133: ...Section 12 Part Number List VC350A Flexoseal System Valco Cincinnati 12 44 400EZ Glue Valve ...
Страница 135: ...Section 12 Part Number List VC350A Flexoseal System Valco Cincinnati 12 46 Scanner Assembly 280xx201 3 4 1 5 6 ...
Страница 139: ...Section 12 Part Number List VC350A Flexoseal System Valco Cincinnati 12 50 Glue Filter 529 Small 593xx024 ...
Страница 143: ...Section 12 Part Number List VC350A Flexoseal System Valco Cincinnati 12 54 DD 1 Pump 66 47 5 5 11 ...
Страница 147: ...Section 12 Part Number List VC350A Flexoseal System Valco Cincinnati 12 58 Glue Regulator Option ...
Страница 159: ...Section 12 Part Number List VC350A Flexoseal System Valco Cincinnati 12 70 Air Filter Regulator Assembly 594xx031 ...
Страница 161: ...Section 12 Part Number List VC350A Flexoseal System Valco Cincinnati 12 72 Electrical Connectors ...
Страница 163: ...Section 12 Part Number List VC350A Flexoseal System Valco Cincinnati 12 74 Fittings ...
Страница 182: ...Appendix A Wiring Diagrams VC350A Flexoseal System Valco Cincinnati A 3 Figure A 2 Interface Board Schematic ...
Страница 211: ...VC350AG VC350AG VC350AG VC350AG VC350AG AutoGlue Control Operations Manual Manual Number MC060 Release Date August 2005 ...