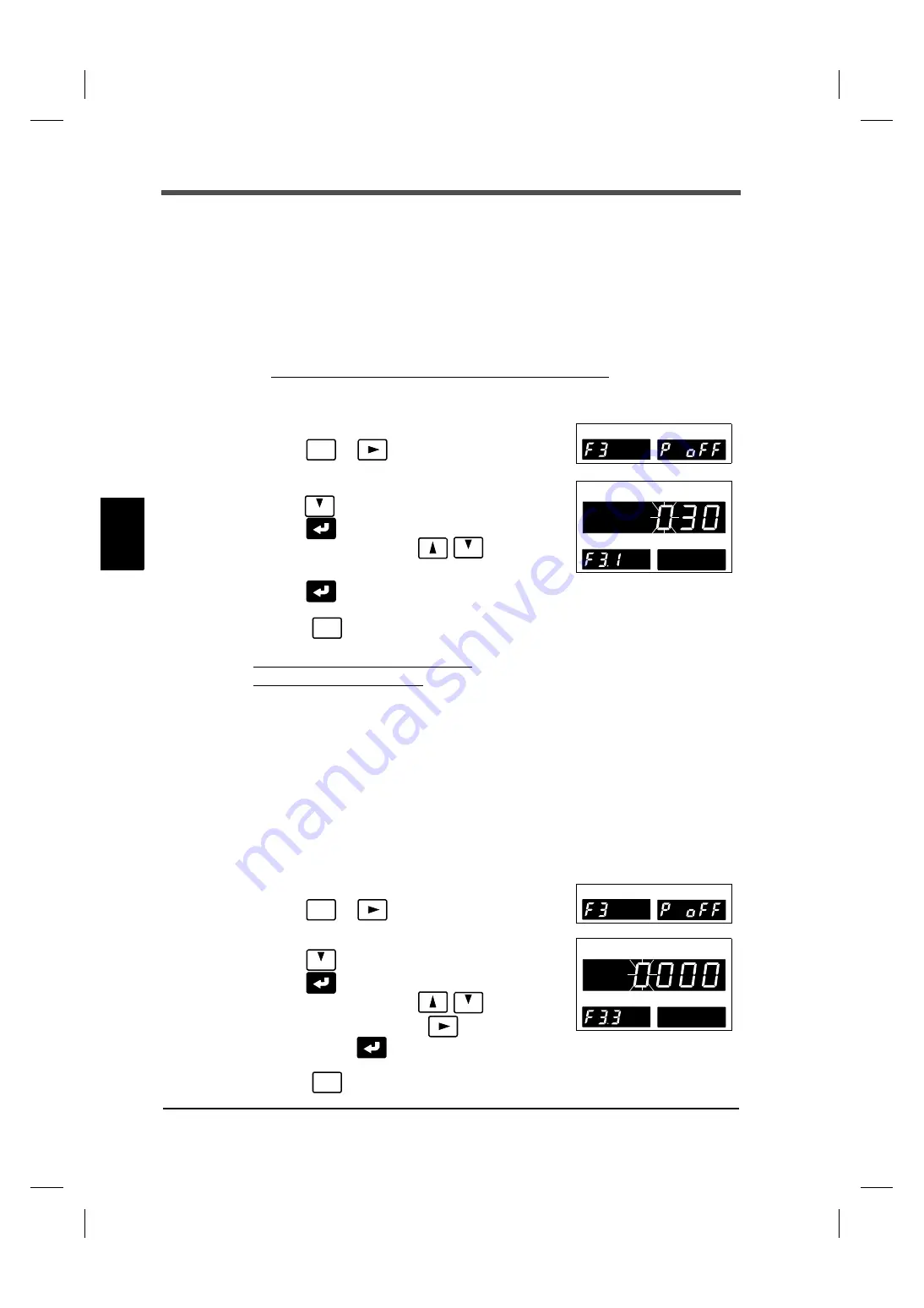
42
5
EXPLANATION OF INDICATED- VALUE-RELATED FUNCTIONS
42
EXPLANATIO
N OF INDI
CATED-
VAL
U
E-REL
A
TED FUNCT
IONS
Chapter
5
5-4.
Digital filter
The digital filter is a function for reducing fluctuations of the indicated value by means of a moving
average of data converted. With an increase in the number of filterings, the indicated value becomes
more stable, but the response to inputs becomes slower. It can be set for each of the torque, the
rotation speed and angle.
≪
Setting value
≫
OFF(0), 2 to 999 [times]
* One time corresponds to one sampling for A/D conversion.
■
Digital filter (torque) setting method
1.
Select setting mode 3.
Press
→
twice.
2.
Set "Digital filter (torque)."
Press
once.
⇒
"Digital filter (torque)" is displayed.
Press
, and the highest digit blinks.
Input the setting value with
.
(Initial value: 030)
Press
to validate it.
3.
Press
twice to go back to the indicated value display.
* Digital filter for rotation speed is F3-4.
* Digital filter for angle is F3-7.
5-5.
Dead band
With respect to torque, the display is forcedly zeroed in a certain range by this function. Use this
function when you do not want to display minute changes, such as microvibration, near zero.
≪
Setting value
≫
0 to 9999
■
Dead band setting method
1.
Select setting mode 3.
Press
→
twice.
2.
Set "Dead band."
Press
three times.
⇒
"Dead band" is displayed.
Press
, and the highest digit blinks.
Input the setting value with
.
Move to the lower digits with
. (Initial value: 0000)
Validate it with
.
3.
Press
twice to go back to the indicated value display.
Speed
rpm
Angle
rad deg
FNC
Torque
Speed
rpm
Nm
H I
LO
HOLD
Angle
rad deg
RECALL
RECALL
ESC
Speed
rpm
Angle
rad deg
FNC
Torque
Speed
rpm
Nm
H I
LO
HOLD
Angle
rad deg
RECALL
RECALL
ESC
Содержание TM380
Страница 1: ...TM380 20MAY2021REV 1 02 TORQUE MONITOR OPERATION MANUAL ...
Страница 11: ...Contents X Contents X M E M O ...
Страница 147: ......