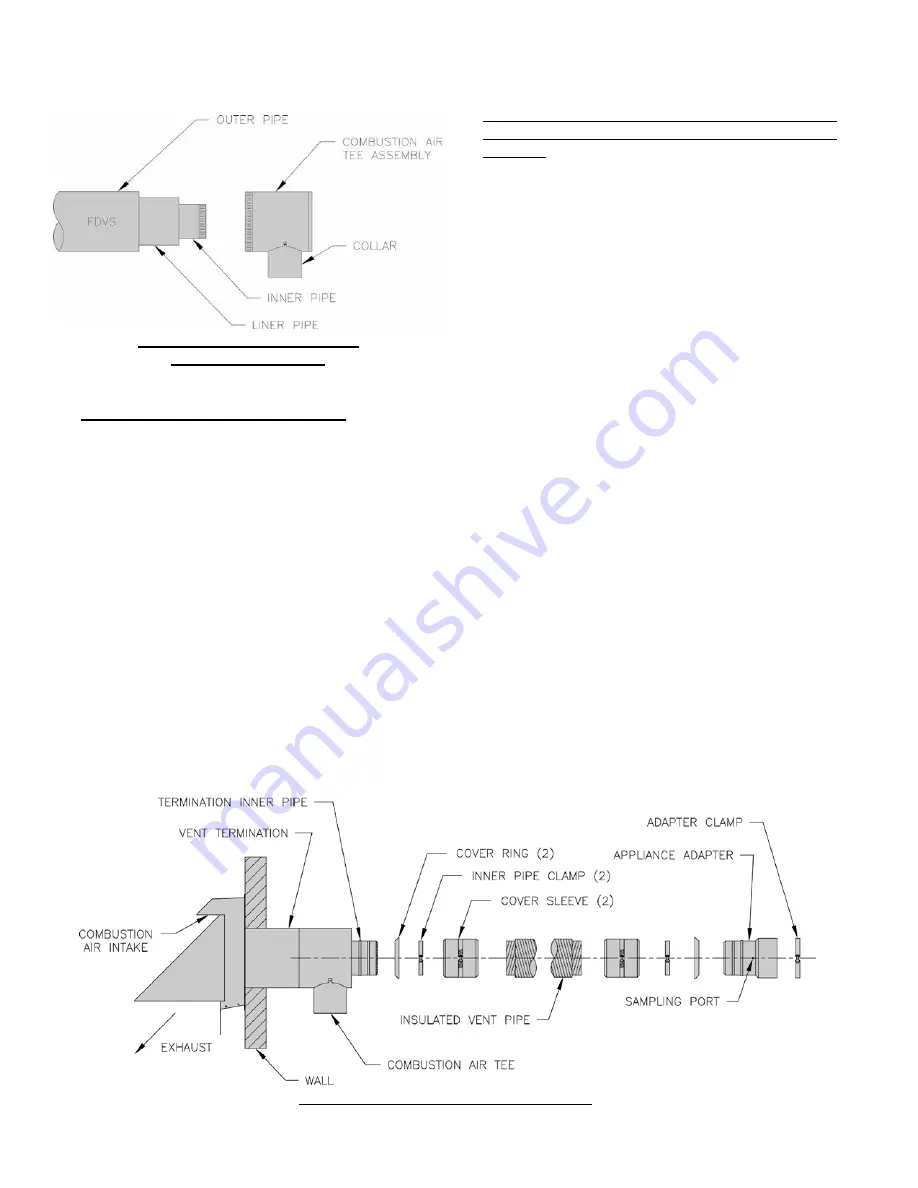
36
C. INSTALLATION OF VENT HOOD TEE
1. Assemble the vent hood tee body to the vent hood outer
pipe, and, rotate the tee, so air intake inlet collar is in the
desired position. See Figure 21.
2. Attach the vent hood tee body to the vent hood outer
pipe with at least tree sheet metal screws (installer
provided).
Note:
The tee may be rotated into any position so that
the collar is in a convenient orientation.
3. After completing assembly of the flexible double wall
insulated vent pipe to the vent termination inner pipe (see
Figure 22 and the following Steps), apply the supplied
high temperature sealant to seal around the inner pipe
protrusion thru the vent tee cover pan, around the joint
between the vent tee collar and the vent tee body, and,
seal or tape the joint between the vent termination outer
pipe and the vent tee body.
D. INSTALLING THE FLEx OIL VENT PIPE FROM
THE VENT TERMINATION TO THE BOILER FLUE
OUTLET
1. The venting system (vent pipe and all connectors) shall
be installed in accordance with the applicable provisions
of any local codes, and, in United States, requirements
of NFPA 31- Standard for the Installation of Oil-Burning
Equipment and NFPA211- Standard for Chimney,
Fireplaces, Vents and Solid Fuel-Burning Appliances,
latest editions. For installations in Canada, follow
requirements of CSA B139 – Installation Code for Oil-
Burning Equipment, latest edition.
2. A vent pipe connector, designed for positive pressure
venting, shall be supported for the design and weight
of material employed, to maintain clearances, prevent
physical damage and separation of joints. All joints MUST
BE sealed, for positive vent pressure, to prevent flue gas
leakage into the structure.
3. Support the vent pipe at intervals no greater than three
(3) feet apart using perforated metal strap or other non-
combustible supports.
4. Allow sealant to cure at least one hour before firing boiler.
5. Route the vent pipe from the vent termination to the boiler
using the minimum number of bends possible. The last
horizontal section of the vent pipe should have a slight
downward slope from the boiler to the vent termination.
For clearances to combustible materials refer to Figure
2B.
6. Maximum length of flexible oil vent pipe is 20 ft. The
vent pipe is also available pre-cut in 5 ft, 10 ft and 15 ft
increments.
7. Verify that flex vent pipe diameter and vent termination
inner pipe diameter correspond to a particular direct vent
configuration MPO-IQ boiler model (see Table 6).
Figure 21: Combustion Air Tee
Assembly Installation
Figure 22: FDVS Component Breakdown
VI. DIRECT VENTING / AIR INTAKE PIPING (continued)
Содержание MPO - IQ
Страница 6: ...6 Figure 1 MPO IQ84 Thru MPO IQ231 Water Boiler ...
Страница 22: ...22 Figure 11 Boiler Removal from Skid III UNIT PAK BOILER ASSEMBLY TRIM CONTROLS continued ...
Страница 27: ...27 Figure 13A Recommended Water Piping for Circulator Zoned Heating Systems IV WATER Boiler PIPING continued ...
Страница 28: ...28 Figure 13B Recommended Water Piping for Zone Valve Zoned Heating Systems IV WATER Boiler PIPING continued ...
Страница 42: ...42 Figure 28A Schematic Wiring Diagram VII ELECTRICAL continued ...
Страница 43: ...43 Figure 28B Schematic Wiring Diagram Burner Options VII ELECTRICAL continued ...
Страница 44: ...44 Figure 28C Ladder Diagram VII ELECTRICAL continued ...
Страница 70: ...70 Bare Boiler Assembly XIV Repair Parts continued ...
Страница 72: ...72 Jacket Assembly XIV Repair Parts continued ...
Страница 74: ...74 MPO IQ84 Thru MPO IQ231 Water Boilers Trim and Controls XIV Repair Parts continued ...
Страница 78: ...78 Beckett AFG Burner XIV Repair Parts continued ...
Страница 80: ...80 Beckett NX Burner XIV Repair Parts continued ...
Страница 92: ...92 U S Boiler Company Inc P O Box 3020 Lancaster PA 17604 1 888 432 8887 www usboiler net ...