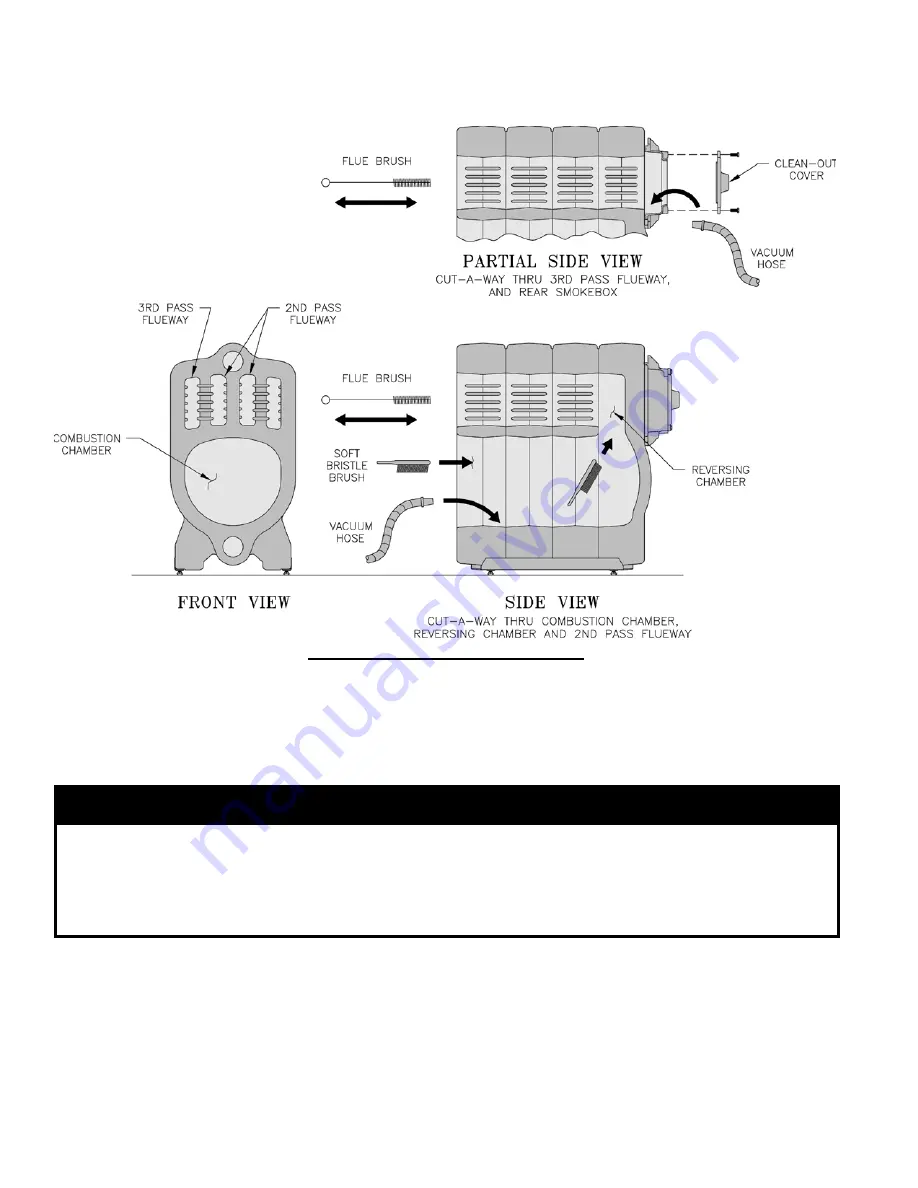
60
Figure 35: Cleaning of Boiler Flueways
WARNING
The boiler must be connected to an approved chimney in good condition. Serious property damage could
result if the boiler is connected to a dirty or inadequate chimney. The interior of the chimney flue must be
inspected and cleaned before the start of the heating season and should be inspected periodically throughout
the heating season for any obstructions. A clean and unobstructed chimney flue is necessary to allow noxious
fumes that could cause injury or loss of life to vent safely and will contribute toward maintaining the boiler's
efficiency.
xII. BOILER CLEANING (continued)
Содержание MPO - IQ
Страница 6: ...6 Figure 1 MPO IQ84 Thru MPO IQ231 Water Boiler ...
Страница 22: ...22 Figure 11 Boiler Removal from Skid III UNIT PAK BOILER ASSEMBLY TRIM CONTROLS continued ...
Страница 27: ...27 Figure 13A Recommended Water Piping for Circulator Zoned Heating Systems IV WATER Boiler PIPING continued ...
Страница 28: ...28 Figure 13B Recommended Water Piping for Zone Valve Zoned Heating Systems IV WATER Boiler PIPING continued ...
Страница 42: ...42 Figure 28A Schematic Wiring Diagram VII ELECTRICAL continued ...
Страница 43: ...43 Figure 28B Schematic Wiring Diagram Burner Options VII ELECTRICAL continued ...
Страница 44: ...44 Figure 28C Ladder Diagram VII ELECTRICAL continued ...
Страница 70: ...70 Bare Boiler Assembly XIV Repair Parts continued ...
Страница 72: ...72 Jacket Assembly XIV Repair Parts continued ...
Страница 74: ...74 MPO IQ84 Thru MPO IQ231 Water Boilers Trim and Controls XIV Repair Parts continued ...
Страница 78: ...78 Beckett AFG Burner XIV Repair Parts continued ...
Страница 80: ...80 Beckett NX Burner XIV Repair Parts continued ...
Страница 92: ...92 U S Boiler Company Inc P O Box 3020 Lancaster PA 17604 1 888 432 8887 www usboiler net ...