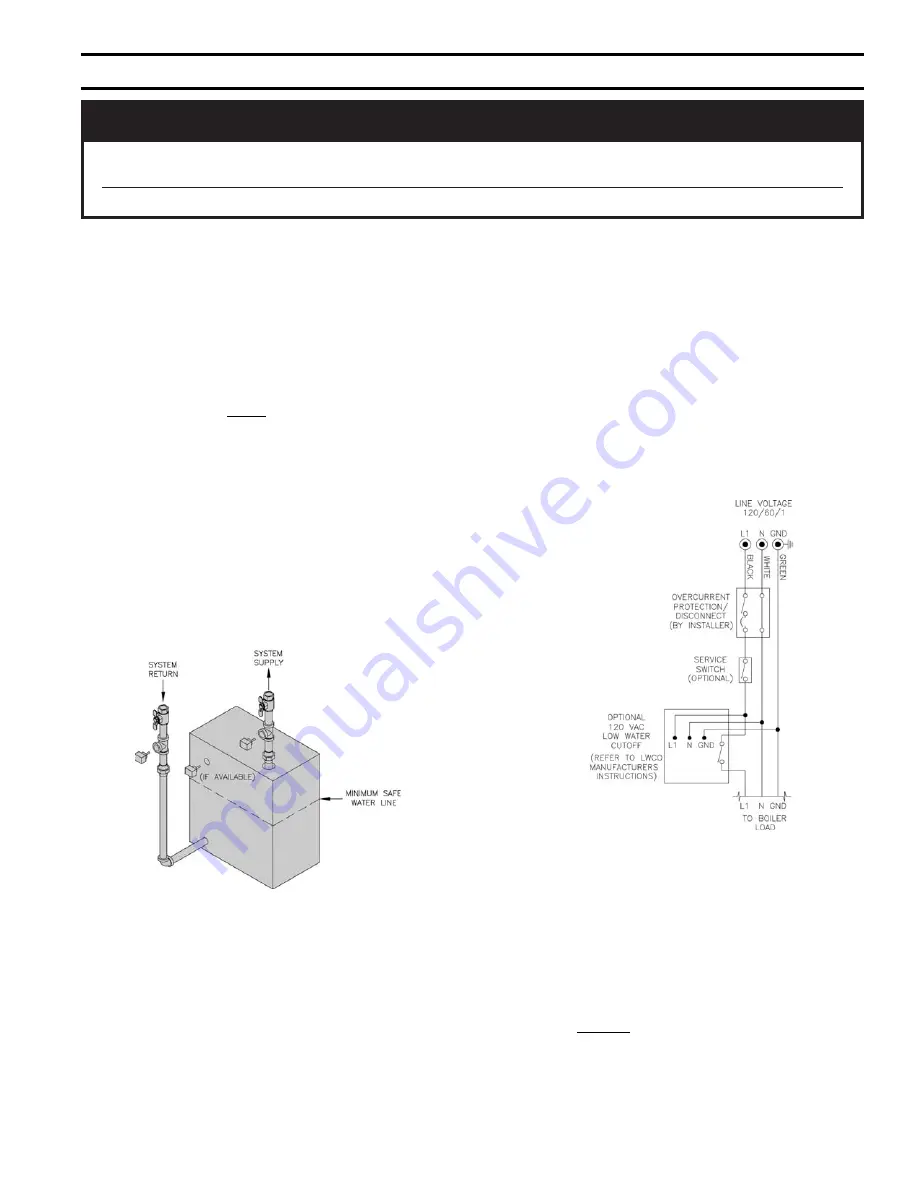
99
XII. Low Water Cut Off (LWCO) on Hot Water Boilers
A 24 VAC LWCO is used primarily for gas fi red boilers
where a 24 volt control circuit exists within the boiler.
However, a 24 VAC LWCO can only be used if the
boiler manufacturer has provided piping and wiring
connections and instructions to allow for this applica-
tion.
How to Test
Shut off fuel supply. Lower water level until water
level is BELOW the LWCO. Generate a boiler demand
by turning up thermostat. Boiler should not attempt to
operate. Increase the water level by fi lling the system.
The boiler should attempt to operate once the water
level is above the LWCO.
Wiring of Typical LWCO
When
A low water cutoff is required to protect a hot water
boiler when any connected heat distributor (radiation) is
installed below the top of the hot water boiler (i.e.
baseboard on the same fl oor level as the boiler). In
addition, some jurisdictions require the use of a LWCO
with a hot water boiler.
Where
The universal location for a LWCO on both gas and oil
hot water boilers is above the boiler, in either the supply
or return piping. The minimum safe water level of a
water boiler is at the uppermost top of the boiler; that is,
it must be full of water to operate safely.
What Kind
Typically, in residential applications, a probe type
LWCO is used instead of a fl oat type, due to their
relative costs and the simplicity of piping for a probe
LWCO.
How to Pipe
A “tee” is commonly used to connect the probe LWCO
to the supply or return piping, as shown below.
LWCO Location
manufacturers recommend an annual inspection of the
probe.
How to Wire
LWCO’s are available in either 120 VAC or 24 VAC
confi gurations. The 120 VAC confi guration can be
universally applied to both gas and oil boilers by wiring
it in the line voltage service to the boiler (after the
service switch, if so equipped).
The presence of water in a properly installed LWCO
will cause the normally open contact of the LWCO to
close, thus providing continuity of the 120 VAC service
to the boiler.
It is recommended to supply power to the probe LWCO
with the same line voltage boiler service as shown
below.
Select the appropriate size tee using the LWCO
manufacturer’s instructions. Often, the branch connec-
tion must have a
minimum
diameter to prevent
bridging between the probe and the tee. Also, the run
of the tee must have a minimum diameter to prevent the
end of the probe from touching or being located too
close to the inside wall of the run of the tee.
Ideally, manual shutoff valves should be located above
the LWCO and the boiler to allow for servicing. This
will allow probe removal for inspection without
draining the heating system. Many probe LWCO
G
N
I
N
R
A
W
.
)
O
C
W
L
(
f
f
O
t
u
C
r
e
t
a
W
w
o
L
t
e
k
r
a
m
r
e
t
f
a
n
a
l
l
a
t
s
n
i
o
t
s
e
r
i
w
y
r
o
t
c
a
f
t
u
c
o
t
T
P
M
E
T
T
A
T
O
N
O
D
.
f
f
O
t
u
C
r
e
t
a
W
w
o
L
r
o
f
d
e
i
f
i
t
n
e
d
i
y
l
l
a
c
i
f
i
c
e
p
s
s
n
o
i
t
c
e
n
n
o
c
e
s
u
y
l
n
O
.
s
n
o
i
t
c
u
r
t
s
n
i
s
'
r
e
r
u
t
c
a
f
u
n
a
m
)
O
C
W
L
(
f
f
O
t
u
C
r
e
t
a
W
w
o
L
e
h
t
w
o
l
l
o
f
,
s
e
s
a
c
l
l
a
n
I
Содержание Burnham Hydronics Revolution RV3
Страница 5: ...5 Figure 2 Dimensions...
Страница 15: ...15 Figure 4 Recommended Separate Horizontal Vent Air Intake Installation...
Страница 16: ...16 Figure 5 Separate Horizontal Vent Air Intake Terminal Confi guration...
Страница 19: ...19 Figure 7 Attic Offset Figure 6 Vertical Vent Installation...
Страница 21: ...21 Figure 9 Vertical Air Intake Piping...
Страница 24: ...24 Figure 10 Combination Horizontal Vent Air Installation...
Страница 25: ...25 Figure 11 Combination Horizontal Vent Air Terminal Installation...
Страница 30: ...30 Figure 13 Combination Vertical Air Intake Terminal Assembly...
Страница 31: ...31 Figure 14 Combination Vertical Vent Disc Terminal Assembly...
Страница 34: ...34 Figure 15 Indoor Air Horizontal Vent Installation...
Страница 35: ...35 Figure 16 Indoor Air Vertical Vent Installation...
Страница 37: ...37 Figure 19 Indoor Air Air Intake Terminal Installation...
Страница 46: ...46 Figure 28 Recommended Boiler Piping For Circulator Zoned Heating Systems...
Страница 47: ...47 Figure 29 Boiler Piping for Zone Valve Zoned Systems...
Страница 52: ...52 Figure 31 Internal Boiler Wiring Schematic Diagram...
Страница 56: ...56 Figure 33 Single Heating Zone Only Wiring Schematic...
Страница 58: ...58 Figure 35 Circulator Zoned System Wiring Schematic...
Страница 59: ...59 Figure 36 Zone Valve Zoned System Wiring Schematic...
Страница 60: ...60 Figure 37 Zone Valve Zoned System Wiring Schematic...
Страница 61: ...61 Figure 38 Different Manufacturer s Zone Valve Connections to Honeywell R8889...
Страница 62: ...62 Figure 39 Circulator Zoning with EC5000 Wiring Schematic...
Страница 63: ...63 Figure 40 Zone Valve Zoning with EC5000 Wiring Schematic...
Страница 64: ...64 Figure 41 Radiant Floor Circulator Zoned System with Alliance Water Heater...
Страница 65: ...65 Figure 42 Radiant Floor Zone Valve Zoned System with Alliance Water Heater...
Страница 68: ...68 Figure 43 Modular Boiler Piping...
Страница 69: ...69 Figure 44 Alternate Modular Boiler Piping...
Страница 71: ...71 Figure 45 Operating Instructions...
Страница 74: ...74 Figure 49 Variable Speed Control Sequence of Operation Figure 50 Internal Primary Secondary Piping...
Страница 77: ...77 Figure 53 Cleaning Boiler Flue Passages...
Страница 80: ...80 Revolution Troubleshooting Tree...
Страница 81: ...81 Revolution Troubleshooting Tree...
Страница 84: ...84...
Страница 86: ...86...
Страница 88: ...88...
Страница 90: ...90...
Страница 92: ...92...
Страница 95: ...95 SERVICE RECORD DATE SERVICE PERFORMED...
Страница 96: ...96 SERVICE RECORD DATE SERVICE PERFORMED...
Страница 97: ...97 SERVICE RECORD DATE SERVICE PERFORMED...