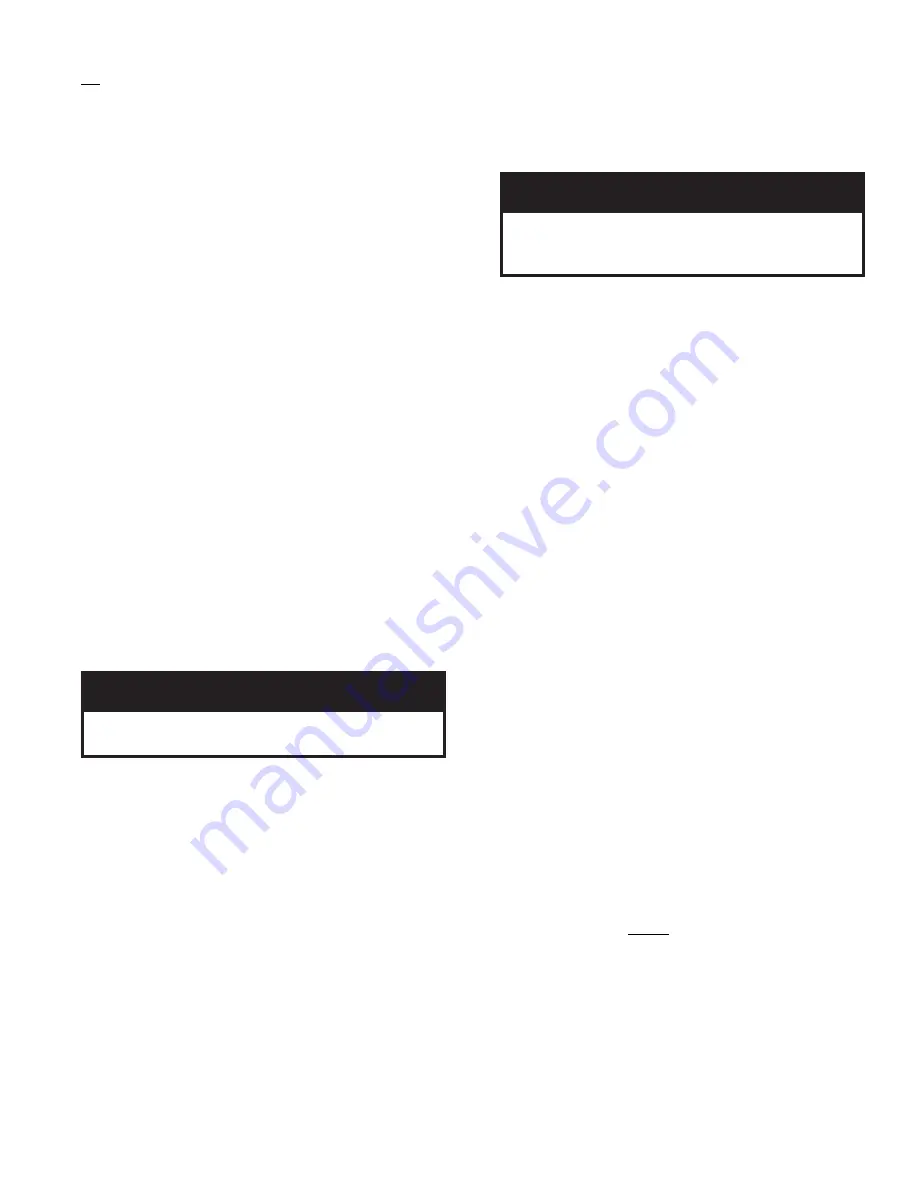
27
The following parts are required for installation which are
not included with this kit. Parts are supplied by others.
•
(1) B-Vent Storm collar – 5 inch
•
(1) B-Vent Boot Flashing – 5 inch
•
(1) B-Vent Support – 5 inch
•
(2) B-Vent Tee – 5 inch
•
(1) B-Vent 1 Foot Pipe Length – 5 inch
•
(1) Fire Stop for Each Floor or Attic Penetration
•
Adequate 5 inch B-Vent for Vertical Run
•
Adequate 3 inch AL 29-4C
®
Vent Pipe for
Vertical Run and Connection to Boiler
•
Adequate Air Intake Piping to Connect B-Vent to
Boiler
•
Adequate Sealant to Ensure Air Tight System
1. Do not exceed maximum vent/air intake lengths.
Refer to Table 4.
2. Position boiler as close to vertical run as possible.
3. Install 5 inch B-vent support, B-vent vertical run,
fl ashing boot and storm collar per B-vent manufac-
turer’s instructions. Apply silicone sealant to all B-
vent joints. Refer to B-vent manufacturer for
approved sealants.
NOTE: Roof penetration must allow enough pipe to
extend above roof surface to maintain minimum
vertical (“X”) and minimum horizontal (“Y”)
distance of twelve (12) inches from roof surface
when B-Vent tee is installed. Allow additional
vertical (“X”) distance for expected snow accumula-
tion. See Figure 12.
E
C
I
T
O
N
h
t
i
w
d
e
t
c
e
t
o
r
p
e
b
t
s
u
m
t
n
e
V
-
B
d
e
s
o
p
x
e
l
l
A
.
t
n
i
a
p
l
e
m
a
n
e
,
x
e
t
a
l
-
n
o
n
,
y
t
i
l
a
u
q
h
g
i
h
a
4. Install B-vent tee at bottom of B-vent vertical run.
Position horizontal leg of tee to allow connection to
air intake piping to boiler. Seal joint per B-vent
manufacturer’s instructions.
5. Install vertical lower seal plate to bottom leg of
B-vent tee. See Figure 12.
6. From top of B-vent vertical run, install three (3) inch
AL 29-4C
®
vent pipe. Refer to Sections C through E
for proper procedures for joining vent pipe and
fi ttings.
NOTE: Female (bell) end of vent pipe is used at
vent terminal.
7. Allow minimum of three (3) inches of vent piping to
extend through lower seal plate of bottom B-vent
tee.
8. Join vent disc terminal to vent terminal elbow.
Refer to Sections C through E for proper procedures
for joining vent pipe and fi ttings.
9. Insert vent disc terminal assembly into horizontal
leg of the remaining B-vent tee. See Figure 14.
Secure terminal to tee.
E
C
I
T
O
N
l
a
i
r
e
t
a
m
e
l
b
i
t
s
u
b
m
o
c
o
t
e
c
n
a
r
a
e
l
c
m
u
m
i
n
i
M
w
o
l
l
o
F
.
h
c
n
i
)
1
(
e
n
o
y
l
l
a
m
r
o
n
s
i
t
n
e
v
-
B
f
o
.
s
n
o
i
t
c
u
r
t
s
n
i
s
'
r
e
r
u
t
c
a
f
u
n
a
m
t
n
e
v
-
B
10. Install B-vent/vent disc terminal assembly to vertical
three (3) inch AL 29-4C
®
vent pipe run and to
vertical B-vent run.
a. Join vertical vent pipe run to vent disc terminal
assembly. Refer to Sections C through E for
proper procedures for joining vent pipe and
fi ttings.
b. With vertical vent pipe and vent disc terminal
assembly joined, lower B-vent tee to join B-vent
vertical run. Seal joint per B-vent manufactur-
er’s instructions.
NOTE: Position horizontal leg of B-vent tee in
direction opposite pitch of roof. See Figure 12.
11. Install one (1) foot B-vent pipe into top leg of
B-vent tee. Seal per B-vent manufacturer’s instruc-
tions.
12. Install disc air intake terminal (supplied with boiler)
to one (1) foot B-vent pipe.
a. Insert collar of disc air intake terminal into air
intake inner disc. Secure disc air intake terminal
to inner disc using four (4) 10 - 32 x ¼ inch
stainless steel machine screws and stainless steel
nuts provided. See Figure 13.
b. Install inner disc/air intake terminal assembly
onto top of one (1) foot B-vent pipe. Secure
inner disc to B-vent pipe and seal with RTV.
13. Install lower air intake adapter to interior B-vent
tee’s horizontal leg. Secure adapter and seal with
RTV.
14.
Connect boiler vent connector to vertical vent
pipe run
. See Figure 12.
a. Vent length is measured from boiler to vent
terminal. Do not exceed maximum vent length.
b. Start at vent connector on top of boiler and work
towards vent piping positioned in B-vent tee.
c. Maintain minimum 1/4 inch per foot slope in
horizontal runs. Slope down towards boiler.
d. Use non-combustible 3/4 inch pipe strap to
support horizontal runs and maintain vent
location and slope. Maximum support spacing is
fi ve (5) feet.
Содержание Burnham Hydronics Revolution RV3
Страница 5: ...5 Figure 2 Dimensions...
Страница 15: ...15 Figure 4 Recommended Separate Horizontal Vent Air Intake Installation...
Страница 16: ...16 Figure 5 Separate Horizontal Vent Air Intake Terminal Confi guration...
Страница 19: ...19 Figure 7 Attic Offset Figure 6 Vertical Vent Installation...
Страница 21: ...21 Figure 9 Vertical Air Intake Piping...
Страница 24: ...24 Figure 10 Combination Horizontal Vent Air Installation...
Страница 25: ...25 Figure 11 Combination Horizontal Vent Air Terminal Installation...
Страница 30: ...30 Figure 13 Combination Vertical Air Intake Terminal Assembly...
Страница 31: ...31 Figure 14 Combination Vertical Vent Disc Terminal Assembly...
Страница 34: ...34 Figure 15 Indoor Air Horizontal Vent Installation...
Страница 35: ...35 Figure 16 Indoor Air Vertical Vent Installation...
Страница 37: ...37 Figure 19 Indoor Air Air Intake Terminal Installation...
Страница 46: ...46 Figure 28 Recommended Boiler Piping For Circulator Zoned Heating Systems...
Страница 47: ...47 Figure 29 Boiler Piping for Zone Valve Zoned Systems...
Страница 52: ...52 Figure 31 Internal Boiler Wiring Schematic Diagram...
Страница 56: ...56 Figure 33 Single Heating Zone Only Wiring Schematic...
Страница 58: ...58 Figure 35 Circulator Zoned System Wiring Schematic...
Страница 59: ...59 Figure 36 Zone Valve Zoned System Wiring Schematic...
Страница 60: ...60 Figure 37 Zone Valve Zoned System Wiring Schematic...
Страница 61: ...61 Figure 38 Different Manufacturer s Zone Valve Connections to Honeywell R8889...
Страница 62: ...62 Figure 39 Circulator Zoning with EC5000 Wiring Schematic...
Страница 63: ...63 Figure 40 Zone Valve Zoning with EC5000 Wiring Schematic...
Страница 64: ...64 Figure 41 Radiant Floor Circulator Zoned System with Alliance Water Heater...
Страница 65: ...65 Figure 42 Radiant Floor Zone Valve Zoned System with Alliance Water Heater...
Страница 68: ...68 Figure 43 Modular Boiler Piping...
Страница 69: ...69 Figure 44 Alternate Modular Boiler Piping...
Страница 71: ...71 Figure 45 Operating Instructions...
Страница 74: ...74 Figure 49 Variable Speed Control Sequence of Operation Figure 50 Internal Primary Secondary Piping...
Страница 77: ...77 Figure 53 Cleaning Boiler Flue Passages...
Страница 80: ...80 Revolution Troubleshooting Tree...
Страница 81: ...81 Revolution Troubleshooting Tree...
Страница 84: ...84...
Страница 86: ...86...
Страница 88: ...88...
Страница 90: ...90...
Страница 92: ...92...
Страница 95: ...95 SERVICE RECORD DATE SERVICE PERFORMED...
Страница 96: ...96 SERVICE RECORD DATE SERVICE PERFORMED...
Страница 97: ...97 SERVICE RECORD DATE SERVICE PERFORMED...