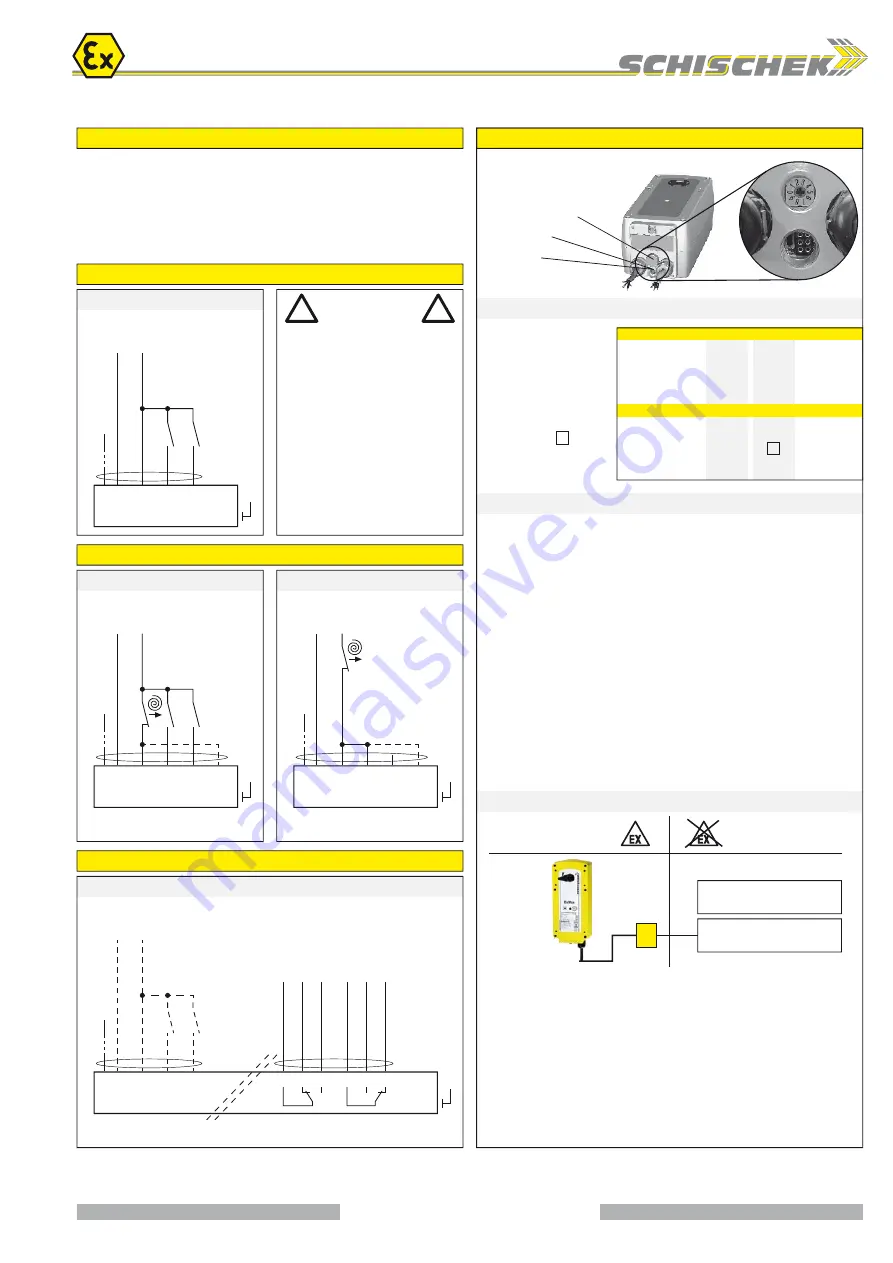
E X P L O S I O N P R O O F
!
!
S
T
ExMax- 5.10
►
ExMax- 15.30
►
ExMax- 5.10-F
►
ExMax- .15-F
►
5 N
15 N
5 N
15 N
▼
10 N
30 N
10 N
▼
3
s/90°
►
15 s/90°
►
30 s/90°
►
60 s/90°
►
120 s/90°
►
00
01
02
03
04
05
06
07
08
09
ExBox
a
a
a
b
b
b
+
~
+
~
+
~
+
~
−
~
−
~
−
~
−
~
PE
PE
PE
PE
1
1
1
1
2
2
2
2
3
3
3
3
5
5
4
4
4
4
PA
PA
PA
PA
1
4
2 3
5 6
< 5°
> 85°
www.schischek.com
Schischek GmbH Germany, Muehlsteig 45, Gewerbegebiet Sued 5, 90579 Langenzenn, Tel. +49 9101 9081-0, Fax +49 9101 9081-77, E-Mail [email protected]
ExMax-S-3P_en
V02 – 20-Apr-2016
ExMax-... ExMax-...-F ExMax-...-S ExMax-...-SF
Special options
... -CTS
... -VAS
Electrical connection
Parameters, adjustments and failure indication
Parameter selection
Functions, adjustments and parameters
Type
Running times
Position of switch (S)
Torques
Example:
ExMax-15.30
Requested parameter:
Torque
30 N
Motor running time 30 s/90°
Result:
Switch position 07
All actuators are equipped with a universal supply unit working at a voltage range from
24...240 VAC/DC. The supply unit is self adjusting to the connected voltage!
The safety operation of the spring return function works if the supply voltage is cut.
For electrical connection inside hazardous areas an Ex-e terminal box, certificated in acc.
with ATEX is required (e.g. ExBox).
An over-current protection fuse < 10 A has to be provided by installer.
Note: the initial current is appr. 2 A for 1 second.
Switch – Push button – Lamp
for adjustment
(behind the blanking plug)
10-position switch (S)
Push button (T)
3-colour LED
Installation
Ex area –
zone 1, 2, 21, 22
Safe area
...Max-...-S or -SF (aux. switches)
24 V / 3 A – 250 V / 0,25 A
Supply *
24...240 VAC/DC ± 10 %
* electrical wiring see diagrams
A) Self adjustment of angle of rotation:
Switch (S) into position 02 (low torque) or 07 (high torque), then push button (T) for
minimum 3 seconds. The actuator will drive into both end positions to be adjusted.
LED indicates GREEN.
Adjustment time needs approx. 60 sec. (30 sec. “On”, 30 sec. “Off”). After that
switch (S) into the position acc. with your required torque and running time.
B) Selection of running time and torque:
Put switch (S) into the correct selected position in acc. to above table.
The selected parameter will work at next operation of the actuator.
Adjustment can be done even without supply voltage. If supply voltage
is available turn switch only if actuator is not running.
C) Running time spring return:
The running time of 3 or 10 sec. spring return is selected by wiring
(see wiring diagrams SB 2.0 and 2.1).
D) Additional information for 3-pos. operation:
a closed, b open = direction I
a and b closed
= motor doesn’t work
b closed, a open = direction II
a and b open
= motor doesn’t work
The rotation direction (I and II) depends on left/right mounting of the actuator to the
damper/valve. You can change direction of the motor by changing electrical wiring
of terminal 3 and 4.
▪ Do not open the cover when circuits are live
▪ Supply cables must be installed in a fixed position and protected against mechanical damage
▪ Connect potential earth
▪
Avoid temperature transfer from process (e.g. hot gas) to actuator (note max. ambient temperature!)
▪ Note ambient temperature
▪ Close all openings with min. IP66
▪ Regard all (inter-)national standards, rules and regulations
▪ Flameproof enclosure is protected against mechanical damages acc. to EN 60079-ff
▪ For outdoor installation a protective housing against rain, snow and sun should be applied to the
actuator, as well as a constant supply at terminal 1 and 2 for the integral heater
▪ Use for wiring an explosion proof Ex-e terminal box
▪ Actuators are maintenance free, an annual function test is recommended
▪ Clean only with damp cloth, avoid dust accumulation
Spring return in ~ 10 s = Standard wiring
Spring return in ~ 3 s = Additional wiring on terminal 5
Spring return in ~ 10 s = Standard wiring
Spring return in ~ 3 s = Additional wiring on terminal 5
On-off / 3-pos.
SB 2.0
On-off / 3-pos.
SB 1.0
On-off (1 wire)
SB 2.1
Wiring of integral auxiliary switches
SB 3.0
Wiring diagram ExMax- ... (without spring return)
Wiring diagram ExMax- ... -F (with spring return)
Wiring diagram ExMax- ... -S and ... -SF
Integral fixed set aux. switches,
potential free contacts switching
at 5° and 85° angle of rotation
max. 24 V / 3 A – 250 V / 0.25 A
min. 5 V / 10 mA
Attention!
At 1-wire control
mode the heater
does not work in
case of open contact.
Wiring of actuator acc. to type and
application see diagrams above
Wiring of the integral, potential free
auxiliary switches
24...240 VAC/DC
24...240 VAC/DC
24...240 VAC/DC
24...240 VAC/DC
Attention
During commissioning apply
a self adjustment drive.
Regard duty cycle at
motor running times!
Never use spring return
actuators without external load.
3 / 4
Содержание X-CUBE Ex
Страница 60: ...Appendix Appendix Air handling unit X CUBE Ex 60...
Страница 159: ...Supplier documents Air handling unit X CUBE Ex 159...