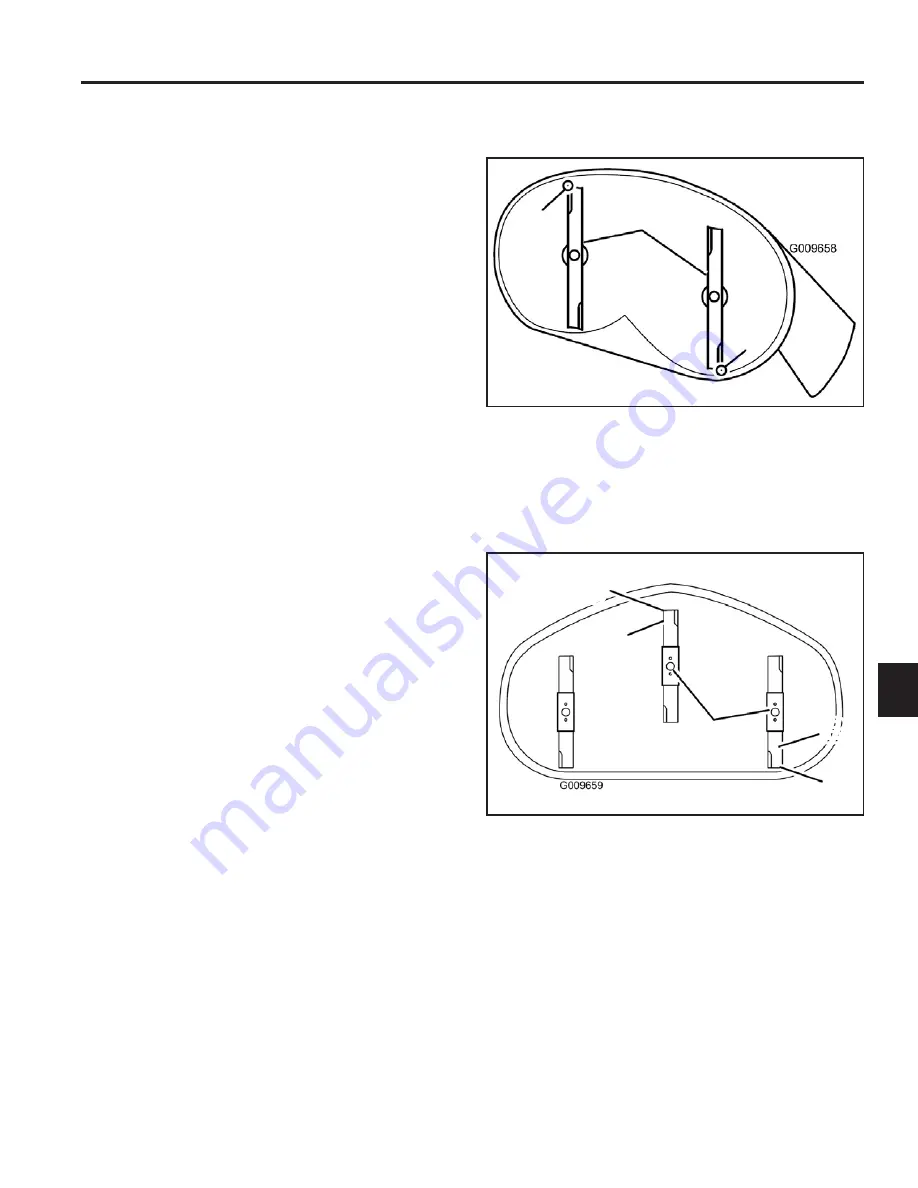
MOWER DECK
6-29
Toro Timecutter SS/MX/ZS Service Manual
6
Fig. 132
fig. 56 G009658
4� Carefully rotate the blades so they are facing front-
to-rear (Fig� 132 and Fig� 133)�
42 & 50 Inch Stamped Deck - Adjusting the
Front-to-Rear Blade Slope
Check the front-to-rear blade level any time you install
the deck� If the front of the deck is more than 5/16”
(7�9mm) lower than the rear of the deck, adjust the blade
level using the following instructions:
1� Park the unit on a level surface and disengage the
PTO switch�
2� Move the motion control levers outward to the park
position, stop engine, remove key, and wait for all
moving parts to stop before leaving the operating
position�
3� Set the height-of-cut lever to middle position�
Note: Check and adjust the side-to-side blade level
if you have not checked the setting; refer to
Side-to-Side Leveling in this chapter.
Mower decks with (2) blades
A� Blades front-to-rear
B� Measure from blade tip to level surface
A
B
B
Fig. 133
fig. 57 G009659
Mower decks with (3) blades
A� Blades front-to-rear
C� Measure from blade tip
B� Outside cutting edges
to level surface
A
B
B
C
C
5� Measure from the tip of the front blade to the level
surface and the tip of the rear blade to the level
surface (Fig� 132 and Fig� 133)� If the front blade tip
is not 1/16-5/16” (1�6-7�9mm) lower than the rear
blade tip, adjust the front locknut�
Содержание TimeCutter SW 4200
Страница 1: ...S E R V I C E MA N U A L T i me C u t t e r S W S WX R e s i d e n t i a l P r o d u c t s ...
Страница 2: ......
Страница 4: ...TABLE OF CONTENTS TOC 6 Toro TimeCutter SS MX ZS Service Manual THIS PAGE INTENTIONALLY LEFT BLANK ...
Страница 11: ...SAFETY INFORMATION 1 2 Toro TimeCutter SW SWX Service Manual 1 THIS PAGE INTENTIONALLY LEFT BLANK ...
Страница 23: ...SPECIFICATIONS 2 12 Toro TimeCutter SW SWX Service Manual 2 THIS PAGE INTENTIONALLY LEFT BLANK ...
Страница 39: ...CHASSIS 3 16 Toro TimeCutter SW SWX Service Manual 3 Fig 027 PICT 1051 A A B C E F D G Deck Lift Exploded View ...
Страница 41: ...CHASSIS 3 18 Toro TimeCutter SW SWX Service Manual 3 Fig 030 PICT 1051 D E G I I K H L Deck Lift Exploded View ...
Страница 55: ...CHASSIS 3 32 Toro TimeCutter SW SWX Service Manual 3 Steering System ...
Страница 59: ...CHASSIS 3 2 Toro TimeCutter SW SWX Service Manual 3 This page is left intentionally blank ...
Страница 81: ...HYDROSTATIC DRIVE SYSTEM 5 16 Toro TimeCutter SW SWX Service Manual 5 THIS PAGE INTENTIONALLY LEFT BLANK ...
Страница 117: ...MOWER DECK 6 36 Toro TimeCutter SS MX ZS Service Manual 6 THIS PAGE INTENTIONALLY LEFT BLANK ...
Страница 132: ...ELECTRICAL 7 15 Toro TimeCutter SW SWX Service Manual 7 Fig 172 PICT 1024 PTO Circuit Schematic ...
Страница 136: ...ELECTRICAL 7 19 Toro TimeCutter SW SWX Service Manual 7 ...
Страница 140: ...ELECTRICAL 7 23 Toro TimeCutter SW SWX Service Manual 7 THIS PAGE INTENTIONALLY LEFT BLANK ...
Страница 141: ......
Страница 142: ...R e s i d e n t i a l P r o d u c t s F o r mN u mb e r 4 9 2 9 3 5 0 D a t e I s s u e d J u n e 2 0 1 5 ...