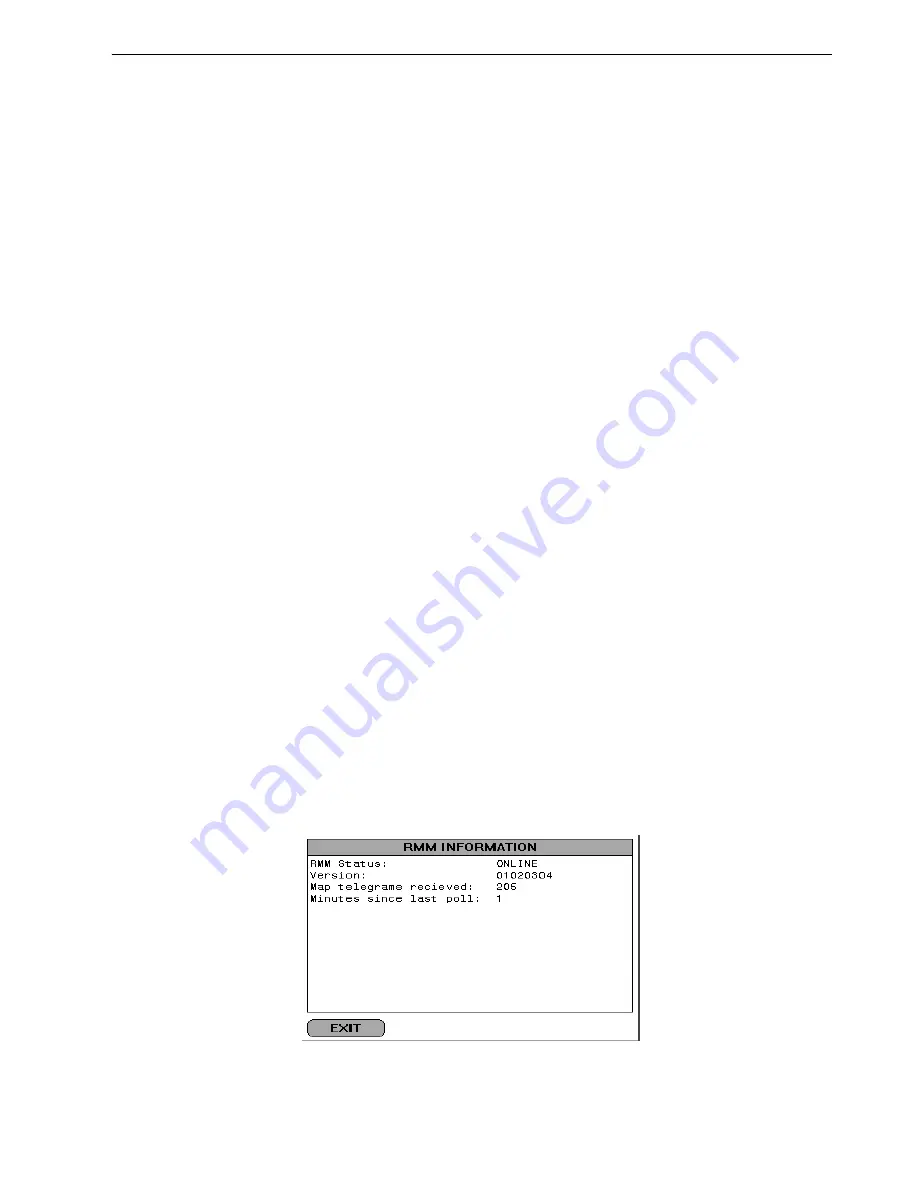
Main Menu
111
Output Information
•
Economizer Valve
•
Digital Valve
•
Heater
•
Evaporator Fan High
•
Evaporator Fan Low
•
Condenser Fan
•
Compressor
RMM and RMM+ States
The RMM (Remote Monitoring Modem) State and RMM+ State menus display the current
communications status with a REFCON system:
Offline:
No communication between the controller RMM and a REFCON system.
Zombie:
The controller has detected a REFCON system master module and is waiting for
communication.
On-line:
The controller RMM is logged-in on a REFCON system.
A complete listing of the controller operating menu is located on an 11” x 17” fold out on the last page of
this manual.
Viewing the RMM State Screen
With the
U
NIT
TURNED
O
N
Allow Unit to start and stabilize and the display showing the unit status
display:
1. Press the
F4
MENU
KEY
to enter the Main menu.
2. Press the
F2
OR
F3 U
P
/D
OWN
key to scroll through Main menu until you reach [States]
3. Press the
F4
ENTER
KEY
to access the STATES Menu
4. Press the
F2
OR
F3 U
P
/D
OWN
key to scroll through Main menu until you reach [RMM or RMM+]
5. Press the
F4
ENTER
KEY
to view the RMM or RMM+ states Menu.
6. Press the
ESC
key to exit the RMM or RMM+ State screen.
Figure 91: RMM States
Содержание 098203
Страница 2: ......
Страница 3: ...MAGNUM TK 60275 4 MM Rev 3 08 15 Copyright 2012 Ingersoll Rand EMEIA Printed in Ireland...
Страница 193: ...Refrigeration Maintenance 191 Figure 163 Filter Drier...
Страница 200: ...Refrigeration Maintenance 198 Figure 169 Receiver Tank Figure 170 Water Cooled Condenser Tank...
Страница 257: ...255 Schematic Diagram RELEASED 19 Sep 2013...
Страница 258: ...256 Wiring Diagram Page 1 of 2 RELEASED 19 Sep 2013...
Страница 259: ...257 Wiring Diagram Page 2 of 2 RELEASED 19 Sep 2013...
Страница 263: ......