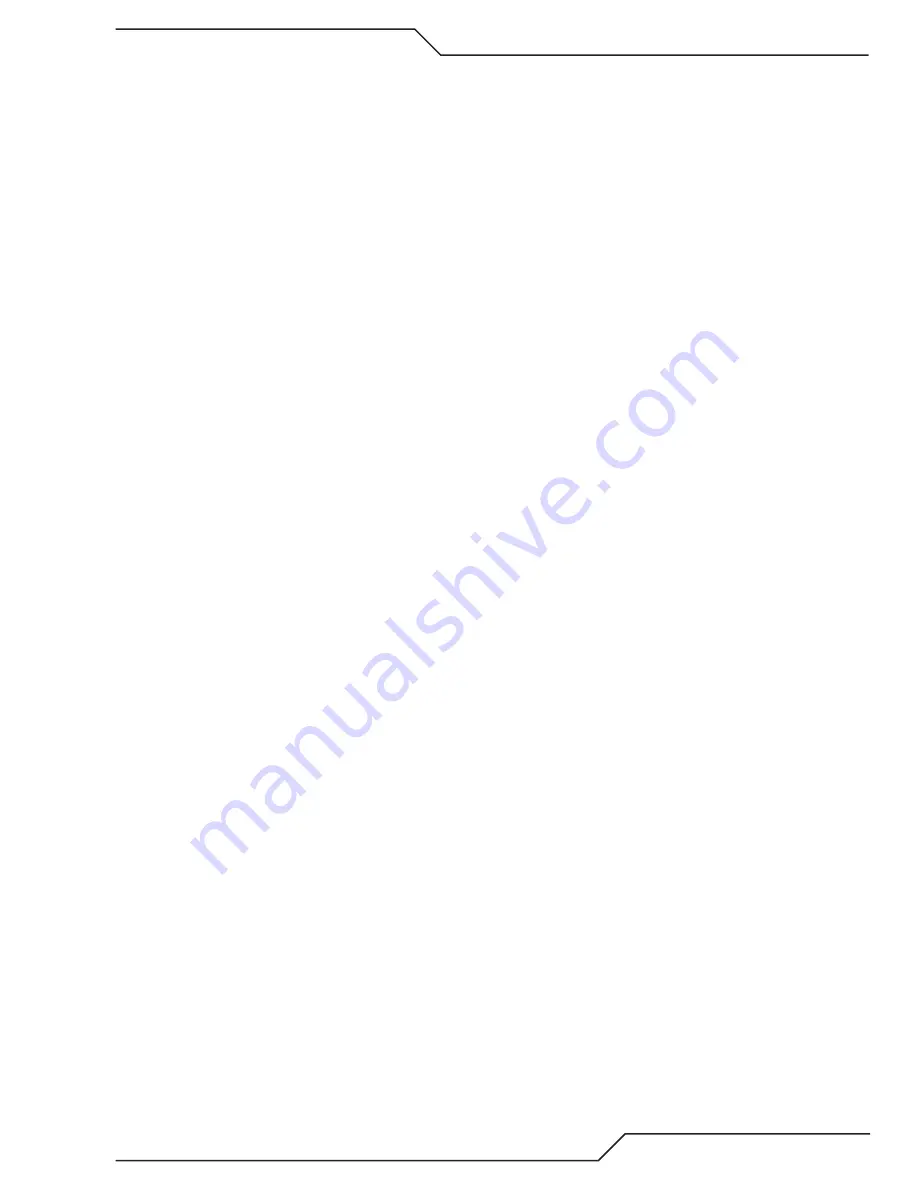
ULTRA-CUT 200 XT
Manual 0-5304
OPERATION
4-13
8. Once purge is complete you are ready to start cutting.
a) If marking is desired press button “Go to Marking”. The screen will show recommended CNC/THC setting. Green
arrow takes you back to the Cut Monitor set up for Marking.
b) To return to cutting on the Cut Monitor press button “Got to Cutting”. Same as with the marking this takes you to
the CNC/THC screen except this displays the cutting settings.
9. Upon applying CNC Start the fan(s) will come on and run during cutting and continue for 4 minutes after the last cut. Then
both pump and fan(s) will shut off. With CNC Start the Gas LED will come on steady indicating gas should be flowing and gas
preflow begins. Near the end of the preflow time the DC LED will come on indicating the inverters are enabled and we have
DC Voltage at the output. At the end of the cut the Gas indicator remains one for the post flow time then goes out.
10. Changing torch consumables:
Following a consumables change or inspection the system will initiate a purge of the gas. This serves two purposes:
a) Remove the coolant that gets into the consumables when they have been removed.
b) If the gas type has changed “Purge” removes the old gas from the lines and replaces it with the new gas. If the
gas type has changed from a fuel gas like H35 to an oxidizing gas like oxygen or air the purge inserts a buffer of inert
gas, nitrogen, so the H35 and oxygen don’t mix.
You can change consumables by removing power or using the “Plasma Disable” SW.
If you remove power the system does not remember what gasses were last used so you have to select the process again and
it will do a complete purge including nitrogen buffer even if you do not change gas types.
With “Plasma Disable” the system remembers what was used last and does only the amount of purge necessary possibly
saving time.
11. Use “Plasma Disable”.
a) You may use the Plasma Disable when removing the torch cartridge to change or inspect consumables. Plasma
disable stops coolant pump, shuts off all gas solenoids, removes power from the inverter (power supply) and pilot
circuits, inhibits the arc starter ignition (HF) circuit. It does not remove power from the TSC 3000 or the systems
logic and communications circuits so you do not need to go through as long a power up process after replacing the
consumables.
b) If changing to a process with a different gas type you may want to select it before enabling the plasma otherwise it
will start purging the old process and when you do select the new one it will purge again taking more time.
c) If you are not changing gas type you may want to turn on the Enable first to start the purge while you enter the
process.
12. Shutting off power.
a) If you chose to shut off power for inspecting or changing consumables, or any other purpose, the system does not
remember what you were doing last so you will have to go through the complete sequence from the beginning start-
ing with step 1.
Operational Suggestions
1. Wait four minutes before setting the ON/OFF switch to OFF after operation. This allows the cooling fans to remove
operating heat from the power supply.
2. For maximum parts life, do not operate the pilot arc any longer than necessary.
3. Use care in handling torch leads and protect them from damage.
4. When using water as the shield note the following:
• Use clean drinking quality tap water to help prevent particulate build-up within the system water shield plumbing.
• Particulate contamination and build-up can cause reduced consumable parts life and premature torch failure.
• A cartridge type particulate water filter may help achieve optimum cutting performance.
Содержание ULTRA-CUT 200 XT
Страница 6: ...This Page Intentionally Blank...
Страница 15: ...ULTRA CUT 200 XT Manual 0 5304 SAFETY INSTRUCTIONS 1 5 This Page Intentionally Blank...
Страница 28: ...ULTRA CUT 200 XT SPECIFICATIONS Manual 0 5304 This Page Intentionally Blank...
Страница 76: ...ULTRA CUT 200 XT INSTALLATION Manual 0 5304 This Page Intentionally Blank...
Страница 142: ...ULTRA CUT 200 XT APPENDIX Manual 0 5304 APPENDIX 8 CCM CPU PCB Layout Test Point Test Point Art A 11675_AB...
Страница 144: ...ULTRA CUT 200 XT APPENDIX Manual 0 5304 APPENDIX 9 CCM I O PCB Layout Test Point Test Point Art A 11676_AC...
Страница 146: ...ULTRA CUT 200 XT APPENDIX Manual 0 5304 APPENDIX 10 Pilot PCB Layout Art A 11677 Test Point Test Point...
Страница 148: ...ULTRA CUT 200 XT APPENDIX Manual 0 5304 APPENDIX 11 Relay and Interface PCB Layout Test Point Test Point Art A 11678_AB...
Страница 150: ...ULTRA CUT 200 XT APPENDIX Manual 0 5304 APPENDIX 12 Display PCB Layout Test Point Test Point Art A 11679...
Страница 151: ...ULTRA CUT 200 XT Manual 0 5304 APPENDIX A 25 Display PCB Test Points TP1 GND TP2 5VDC TP3 24VDC...
Страница 152: ...ULTRA CUT 200 XT APPENDIX Manual 0 5304 APPENDIX 13 System Bias PCB Layout Test Point Test Point Art A 11680...
Страница 154: ...ULTRA CUT 200 XT APPENDIX Manual 0 5304 APPENDIX 14 Main Inverter Bottom PCB Layout Test Point Test Point Art A11681_AB...
Страница 156: ...ULTRA CUT 200 XT APPENDIX Manual 0 5304 APPENDIX 15 Main Inverter Top PCB Layout Test Point Test Point Art A11682_AB...
Страница 158: ...ULTRA CUT 200 XT APPENDIX Manual 0 5304 APPENDIX 16 Control and Fault PCB Layout Test Point Test Point Art A11683_AB...
Страница 160: ...ULTRA CUT 200 XT APPENDIX Manual 0 5304 APPENDIX 17 Cap Bias Bottom PCB Layout Art A 11685_AB...
Страница 161: ...ULTRA CUT 200 XT Manual 0 5304 APPENDIX A 35 APPENDIX 18 Cap Bias Top PCB Layout Art A 11686_AB...
Страница 162: ...ULTRA CUT 200 XT APPENDIX Manual 0 5304 APPENDIX 19 Suppressor PCB Layout Art A 11684_AB...
Страница 165: ...ULTRA CUT 200 XT Manual 0 5304 APPENDIX A 39 This Page Intentionally Blank...
Страница 227: ......