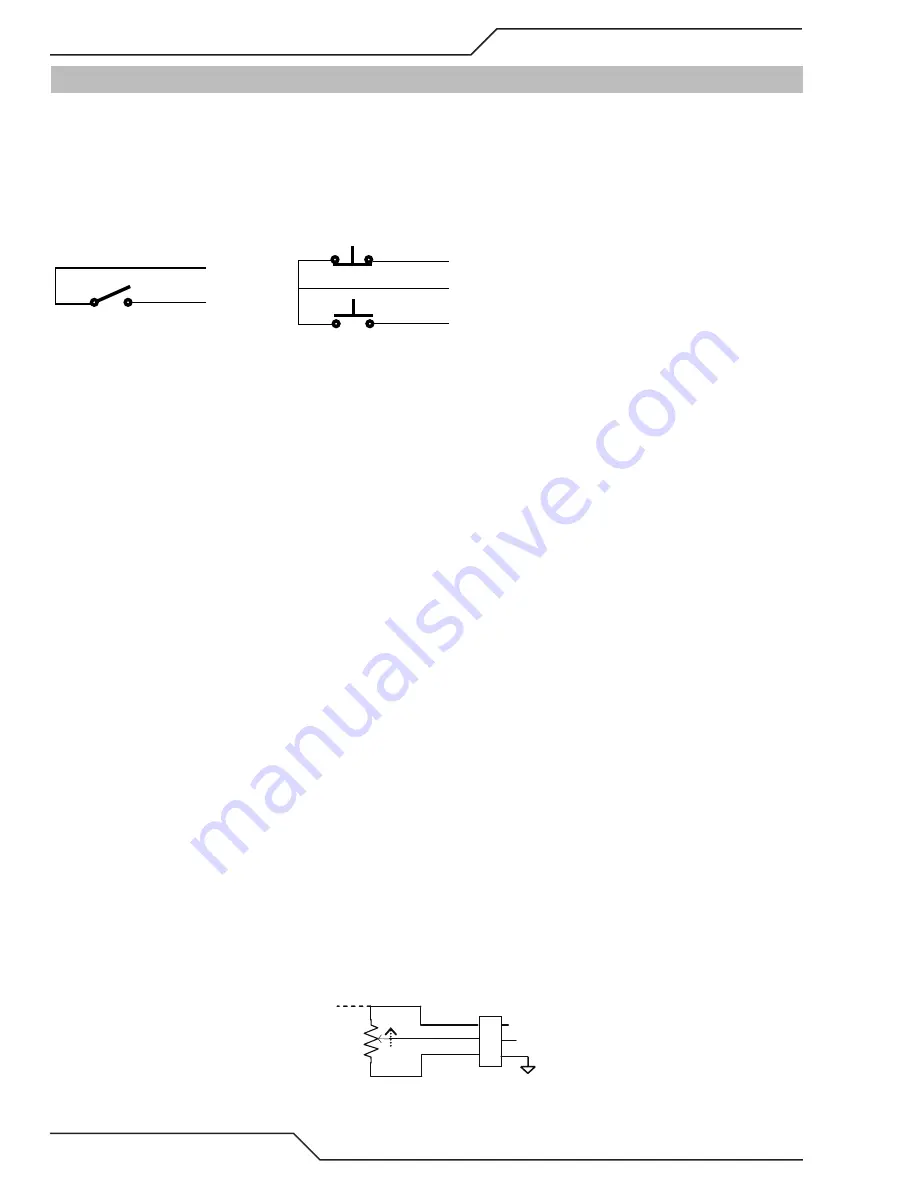
ULTRA-CUT 200 XT
A-6
APPENDIX
Manual 0-5304
CNC Input / Output Descriptions
E-Stop input
— Requires closed connection rated for
35ma. @ 20VDC
for unit to operate. Factory installed jumper
between TB1-1&2 must be removing when connecting user supplied E-Stop circuit.
4
Start/Stop input
—Switch (momentary or sustained) rating 35ma. @ 20 VDC
Start / Stop circuit configurations. Momentary Start / Stop (Latched) is only available at TB1.
MOMENTARY START / STOP
START / STOP
TB1-6
TB1-5
TB1-4
SUSTAINED START / STOP
START
STOP
TB1-5
TB1-6
Divided Arc Voltage output
— Arc Voltage signal is isolated from plasma supply, however (-) is common with
other isolated CNC signals. Max Divided Arc Voltage signal level depends on actual arc voltage times divide ratio
however can not exceed approximately 12 V.
3
Analog Current Control input
— Analog Current Control includes analog isolation module, separate isolation
module not usually required however it’s low input is common with the other isolated CNC inputs. Scaling of Analog
Current Control input is 0V = 0A, 10V. = MAX output and is linear in between. However MIN output is 5A. User
is responsible for setting correct analog voltage to maintain at least 5A output. To use Analog Current Control on
the I/O PCB set SW 11 to down position and on the CPU PCB set SW8-2 ON (up).
Hold Start input
—Normally open, close to hold start. Circuit rating 10 ma. @ 20VDC. Delays pilot ignition, gas
preflow continues. Used by some height controls to flow gas while finding height. Also used for synchronizing starts
when multiple plasma supplies are used on same cutting table. User supplies circuit to keep Hold Start inputs ac-
tive until all torches have found height. Used with CNC START. Apply START to begin gas flow. Same time apply
HOLD to delay ignition until height is found. Remove HOLD to ignite pilot, initiate arc transfer.
Preflow On input
— Normally open, close to start preflow prior to normal START signal. Circuit rating 10 ma. @
20VDC. Torch Height Controls (THC) normally issue START signal to plasma supply after torch height has been
found. Then the plasma takes 1-2 seconds (or more) to perform preflow before igniting pilot. Some THCs have an
output that can start preflow early during height finding saving 1-2 seconds on each cut. PREFLOW ON should
remain active for at least 1 second after CNC START is applied. It is OK if it remains on until the end of the cut.
Need to recycle it to begin a new preflow prior to applying START for the next cut.
Pilot On output
– Relay contacts rated 1A @ 120 VAC / 28 VDC. Contacts close when pilot on. Can be wired parallel
with Ok to Move contacts to start machine motion when pilot established. Used when starting over holes. Starting
over holes requires setting SW8-1 ON (up) on the CPU PCB for extended pilot time. Using extended pilot time to
start over holes or for cutting over holes will reduce parts life.
OK to Move output
— Active when cutting arc is established, arc is transferred. Used to signal cutting table to
start X-Y motion. Relay contacts rated 1A @ 120 VAC or 28 VDC when SW6 set for contacts. When SW6 is set for
DCV, output supplies 15-18 VDC @ 100 ma. May be wired parallel with Pilot On to start cutting machine motion
as soon as pilot established.
5
OK to Move2
– Provides a second set of N.O. contacts that close when arc transfer is detected. Contacts are rated
for maximum of 24 VAC/DC @ 1A. Simplified CNC Circuit.
5
+10V @ 10ma. For Remote CC Pot
– Previously CCM versions if one wanted to use a potentiometer for the Remote
Analog Current Control (CC) input an external 10 V supply was required for Pot High.. Now an isolated (from main
plasma circuits) 10V supply is provided. Recommended value of the pot is 5K or 10K.
Ext. +10V
11
10
9
TB1
+10V
WIPER
Art # A-09246
Содержание ULTRA-CUT 200 XT
Страница 6: ...This Page Intentionally Blank...
Страница 15: ...ULTRA CUT 200 XT Manual 0 5304 SAFETY INSTRUCTIONS 1 5 This Page Intentionally Blank...
Страница 28: ...ULTRA CUT 200 XT SPECIFICATIONS Manual 0 5304 This Page Intentionally Blank...
Страница 76: ...ULTRA CUT 200 XT INSTALLATION Manual 0 5304 This Page Intentionally Blank...
Страница 142: ...ULTRA CUT 200 XT APPENDIX Manual 0 5304 APPENDIX 8 CCM CPU PCB Layout Test Point Test Point Art A 11675_AB...
Страница 144: ...ULTRA CUT 200 XT APPENDIX Manual 0 5304 APPENDIX 9 CCM I O PCB Layout Test Point Test Point Art A 11676_AC...
Страница 146: ...ULTRA CUT 200 XT APPENDIX Manual 0 5304 APPENDIX 10 Pilot PCB Layout Art A 11677 Test Point Test Point...
Страница 148: ...ULTRA CUT 200 XT APPENDIX Manual 0 5304 APPENDIX 11 Relay and Interface PCB Layout Test Point Test Point Art A 11678_AB...
Страница 150: ...ULTRA CUT 200 XT APPENDIX Manual 0 5304 APPENDIX 12 Display PCB Layout Test Point Test Point Art A 11679...
Страница 151: ...ULTRA CUT 200 XT Manual 0 5304 APPENDIX A 25 Display PCB Test Points TP1 GND TP2 5VDC TP3 24VDC...
Страница 152: ...ULTRA CUT 200 XT APPENDIX Manual 0 5304 APPENDIX 13 System Bias PCB Layout Test Point Test Point Art A 11680...
Страница 154: ...ULTRA CUT 200 XT APPENDIX Manual 0 5304 APPENDIX 14 Main Inverter Bottom PCB Layout Test Point Test Point Art A11681_AB...
Страница 156: ...ULTRA CUT 200 XT APPENDIX Manual 0 5304 APPENDIX 15 Main Inverter Top PCB Layout Test Point Test Point Art A11682_AB...
Страница 158: ...ULTRA CUT 200 XT APPENDIX Manual 0 5304 APPENDIX 16 Control and Fault PCB Layout Test Point Test Point Art A11683_AB...
Страница 160: ...ULTRA CUT 200 XT APPENDIX Manual 0 5304 APPENDIX 17 Cap Bias Bottom PCB Layout Art A 11685_AB...
Страница 161: ...ULTRA CUT 200 XT Manual 0 5304 APPENDIX A 35 APPENDIX 18 Cap Bias Top PCB Layout Art A 11686_AB...
Страница 162: ...ULTRA CUT 200 XT APPENDIX Manual 0 5304 APPENDIX 19 Suppressor PCB Layout Art A 11684_AB...
Страница 165: ...ULTRA CUT 200 XT Manual 0 5304 APPENDIX A 39 This Page Intentionally Blank...
Страница 227: ......