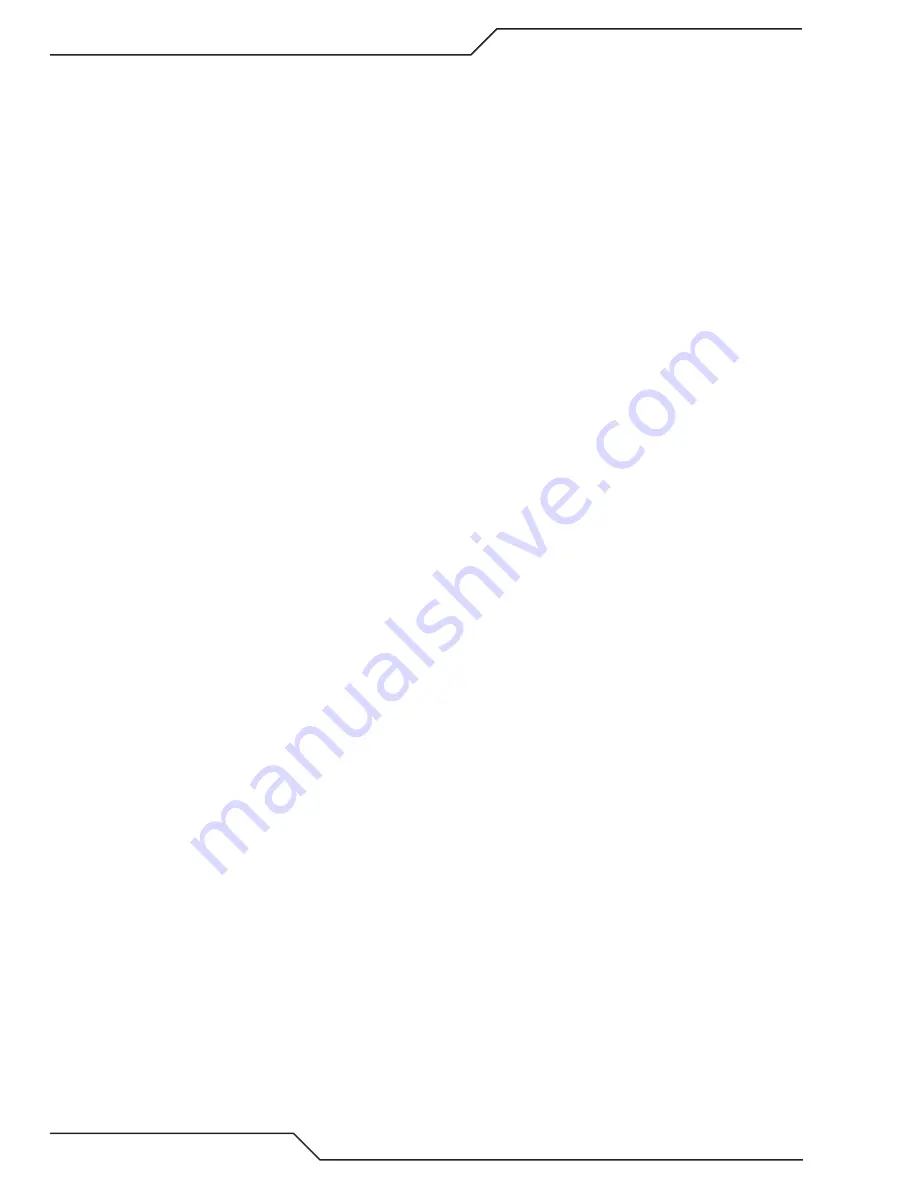
ULTRA-CUT 200 XT
A-74
APPENDIX
Manual 0-5304
302
Gas Control communications reply fault
Communication has been established but Gas Control did not reply to a request from the CCM in the time al-
lowed. Likely cause is Fiber-optic problems (see code 501) or if problem persists defective Gas Control main PCB.
303
Gas Pressure fault
Gas pressure faults only show up when you try to start the torch, not during purging or setting flows .
With the Auto-Cut 200 XT and the Auto-Cut 300 XT (GCM 1000 XT), the gas pressure sensor is only on the
plasma gas and is in series with Run/Set switch. A 303 code here indicates either plasma gas missing or very
low pressure, less than 50 PSI, or RUN/SET switch is in SET position.
Starting with GCM2010 revision AG we measure inlet pressure of both plasma and shield gas at the inlet of
the gas selection manifold. If pressure is either too low or too high it sets 303 code. Earlier revision should not
display 303 code. GCM2010 will display which gas is the problem and its actual pressure. The pressure at the
point where it is measured should be in the range of 100-135 PSI. Exception is for shield gas if the Gas switch
is set to Pressure then the min pressure can be 85 PSI.
In the GCM 2010 Gas Control, on the main PCB, measure between test points TP1 (ground) and TP18 (shield)
and TP19 (plasma) to measure the output of the pressure sensors. Voltage should be between 2.6V to 3.5V for
100-135 PSI. With shield switch set to pressure low limit is 2.1V. Whichever gas is outside those limits will
be the one causing the fault. Remember the pressure may drop during operation, set the code, then recover
displaying L303 when you are measuring it.
• To test for faulty pressure sensor or inadequate gas supply with too much restriction. On the GCM 2010
place the Mode switch to SET Plasma & Shield, turn the mechanical pressure regulators to max pressure
and compare mechanical gauges with the pressure display. If the pressure display doesn’t approximately
match the gauge the sensor is likely defective. If the gauge and the pressure display both show low pres-
sure the supply to the gas control has too much restriction. Perhaps the hose is too long or too small.
304
Gas Control not ready
This is the normal code when the gas control is conducting a purge at start up or when the process is loaded
or changed or when the plasma system has been disabled and is returned to “Enable”. If it is a GCM 2010 the
Mode switch may not be set to the RUN mode.
Code 304 combined with 204 & 402 when the Plasma Enable on the GCM 2010 gas control is set to disable can
indicate a fault in the CCM I/O PCB. When switching back to Enabled the pump will not restart so continues
to display 4-2 indicating no coolant flowing.
Normally the code during a disable should be 101. Circuits on the I/O PCB detect the Plasma Enable is disabled
and send signal to the microcontroller in the CCM. If a fault in the CCM prevents that signal from getting sent
to the microcontroller it doesn’t know the system is disabled so it sets these other 3 codes.
305
Gas Control Protocol Error
Application error or firmware incompatibility fault. Consult factory for latest firmware update. Possible elec-
tromagnetic interference from the Arc Starter; inspect grounding, bonding, and isolation.
306
Not Used. This is one of the reserved codes from the earlier product.
307
Gas Control returns wrong command sequence.
Firmware incompatibility. Consult factory for latest firmware update. Possible electromagnetic interference
from the Arc Starter; inspect grounding; bonding; and isolation.
308
Mismatch between the CCM and gas control type.
The Auto-Cut XT CCM is designed to work with the GCM 1000 (AC 300 XT) or the built in gas control of the AC
200 XT. Attempting to use a GCM 2010 or DFC 3000 Auto Gas Control on an Auto-Cut will result in a 308 code.
Similarly attempting to use a CCM from an Auto-Cut XT in an Ultra-Cut XT supply will also result in a 308 code.
Содержание ULTRA-CUT 200 XT
Страница 6: ...This Page Intentionally Blank...
Страница 15: ...ULTRA CUT 200 XT Manual 0 5304 SAFETY INSTRUCTIONS 1 5 This Page Intentionally Blank...
Страница 28: ...ULTRA CUT 200 XT SPECIFICATIONS Manual 0 5304 This Page Intentionally Blank...
Страница 76: ...ULTRA CUT 200 XT INSTALLATION Manual 0 5304 This Page Intentionally Blank...
Страница 142: ...ULTRA CUT 200 XT APPENDIX Manual 0 5304 APPENDIX 8 CCM CPU PCB Layout Test Point Test Point Art A 11675_AB...
Страница 144: ...ULTRA CUT 200 XT APPENDIX Manual 0 5304 APPENDIX 9 CCM I O PCB Layout Test Point Test Point Art A 11676_AC...
Страница 146: ...ULTRA CUT 200 XT APPENDIX Manual 0 5304 APPENDIX 10 Pilot PCB Layout Art A 11677 Test Point Test Point...
Страница 148: ...ULTRA CUT 200 XT APPENDIX Manual 0 5304 APPENDIX 11 Relay and Interface PCB Layout Test Point Test Point Art A 11678_AB...
Страница 150: ...ULTRA CUT 200 XT APPENDIX Manual 0 5304 APPENDIX 12 Display PCB Layout Test Point Test Point Art A 11679...
Страница 151: ...ULTRA CUT 200 XT Manual 0 5304 APPENDIX A 25 Display PCB Test Points TP1 GND TP2 5VDC TP3 24VDC...
Страница 152: ...ULTRA CUT 200 XT APPENDIX Manual 0 5304 APPENDIX 13 System Bias PCB Layout Test Point Test Point Art A 11680...
Страница 154: ...ULTRA CUT 200 XT APPENDIX Manual 0 5304 APPENDIX 14 Main Inverter Bottom PCB Layout Test Point Test Point Art A11681_AB...
Страница 156: ...ULTRA CUT 200 XT APPENDIX Manual 0 5304 APPENDIX 15 Main Inverter Top PCB Layout Test Point Test Point Art A11682_AB...
Страница 158: ...ULTRA CUT 200 XT APPENDIX Manual 0 5304 APPENDIX 16 Control and Fault PCB Layout Test Point Test Point Art A11683_AB...
Страница 160: ...ULTRA CUT 200 XT APPENDIX Manual 0 5304 APPENDIX 17 Cap Bias Bottom PCB Layout Art A 11685_AB...
Страница 161: ...ULTRA CUT 200 XT Manual 0 5304 APPENDIX A 35 APPENDIX 18 Cap Bias Top PCB Layout Art A 11686_AB...
Страница 162: ...ULTRA CUT 200 XT APPENDIX Manual 0 5304 APPENDIX 19 Suppressor PCB Layout Art A 11684_AB...
Страница 165: ...ULTRA CUT 200 XT Manual 0 5304 APPENDIX A 39 This Page Intentionally Blank...
Страница 227: ......