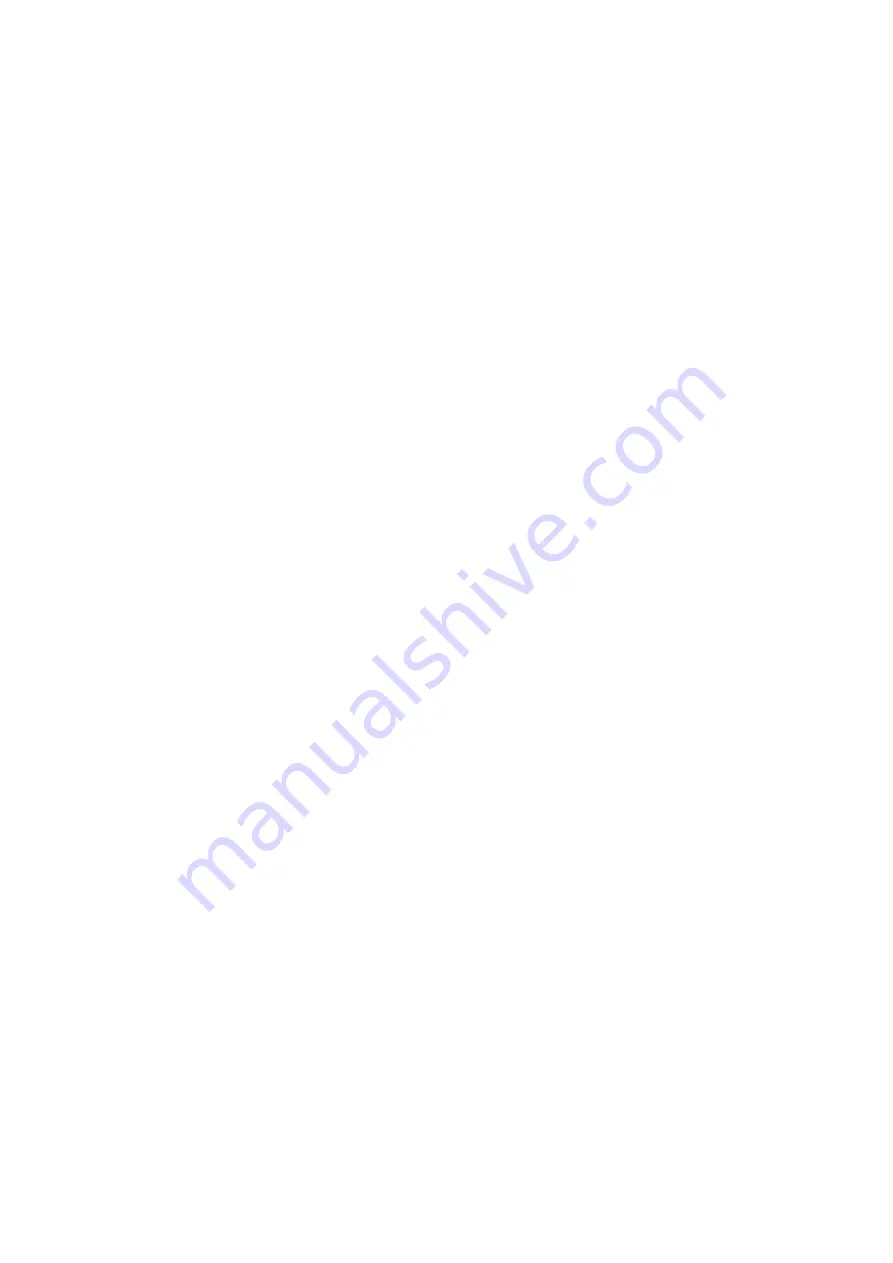
12 Chapter 2 - Introduction
User Manual
Standard functions
-
Feed voltages generated from intermediate circuit voltage by switching technology.
-
Reduced motor noise thanks to special PWM control technology.
-
Output protected against short circuits between phases and to ground.
-
Possibility of switching motors in and out of the drive output (see section 5.2.3).
-
Protection against over-current, over-voltage and under-voltage.
-
Ability to withstand mains power outages of up to 15 ms (see section 7.6 for automatic restart programming).
-
Sinsoidal output current from sinusoidal PWM.
-
Smooth, controlled motor rotation even at very low speeds.
-
Programmable slip compensation to minimise load-related speed variation.
-
Manual or automatic low speed voltage boost.
-
Automatic voltage and frequency control in case of overload to avoid motor stalling.
-
Keypad or RS 485 serial line parameter control.
-
Linear or S acceleration/deceleration ramps.
-
DC braking with the following control modes:
a - digital input control;
b - automatic braking below a set frequency;
c - pre-start braking for pumps and fans rotated by liquid or air movement prior to electrical start-up, to prevent switching
on a motor that is already rotating.
-
Wide selection of V/f ratios.
-
Overload level control.
-
Non-volatile memory for the last 4 alarm event messages; messages not lost even if power is switched off.
-
Set speed signalling via potential-free contacts or over a serial line for signalling e.g. zero speed.
-
Digital parameter or serial line referencing.
Advanced functions available from the complete version
-
Referencing with 0...10 V, -10...10 V, 0...20 mA, 4...20 mA analog signal.
-
Choice of open loop or closed loop functioning.
Options
-
RS 485 serial line control card (to be specified at time of order)
-
E
2
PROM key for saving custom settings.
-
Remote keyboard kit.
-
Serial keyboard.