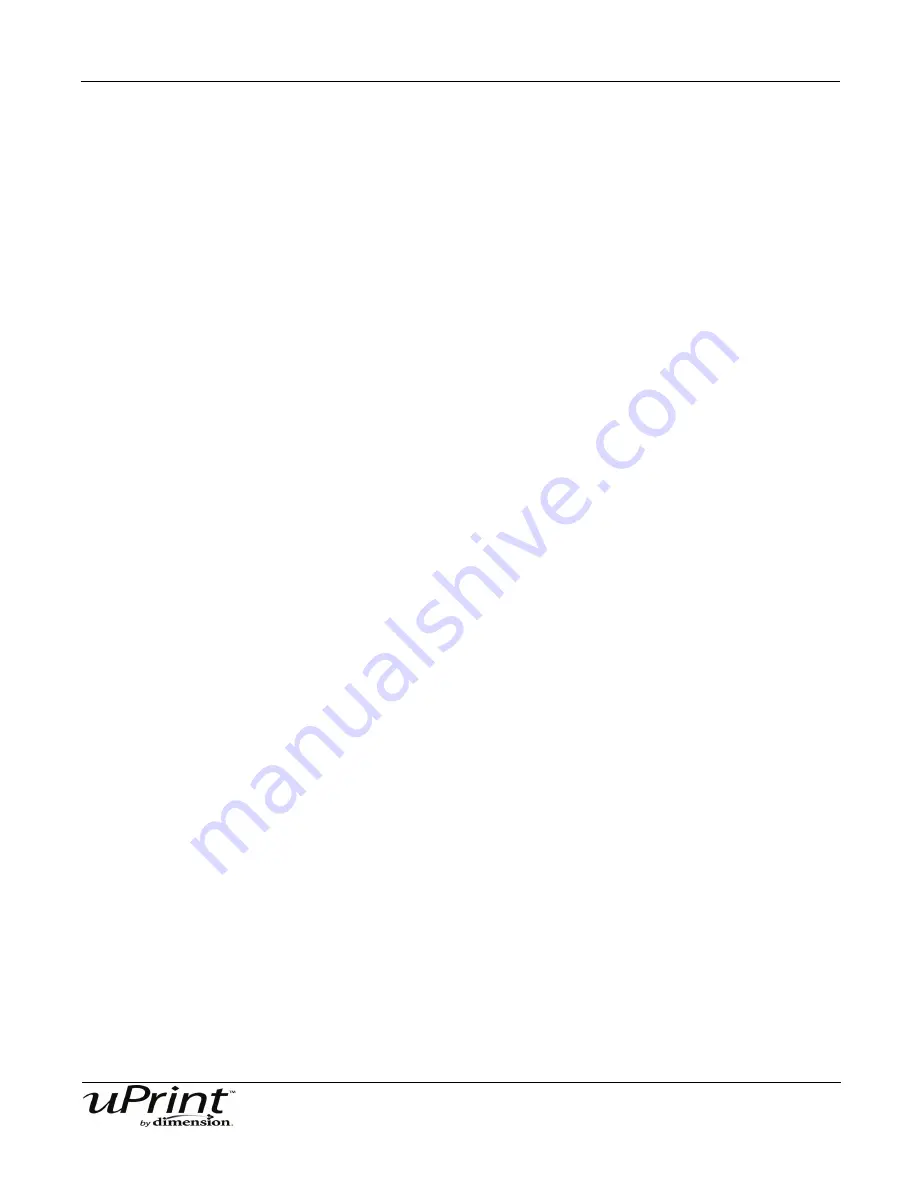
Stratasys Document Number 206465-0001
Troubleshooting and Maintenance
64
Chamber Light Bar
Replace chamber light bar:
1. Power down the printer.
2. Locate the wiring harness leading away from the bottom of the light bar.
3. Disconnect the light bar from the wiring harness by squeezing the wiring harness clip while pulling
down.
4. Remove the light bar by removing the 3 attachment screws (top, middle, bottom) - use the 7/64 T-han-
dle wrench supplied in the Startup Kit.
5. Install a replacement light bar with the 3 attachment screws - do not overtighten the screws.
6. Re-attach the wiring harness lead.
Содержание 180-00108 uPrint
Страница 1: ...User Guide ...