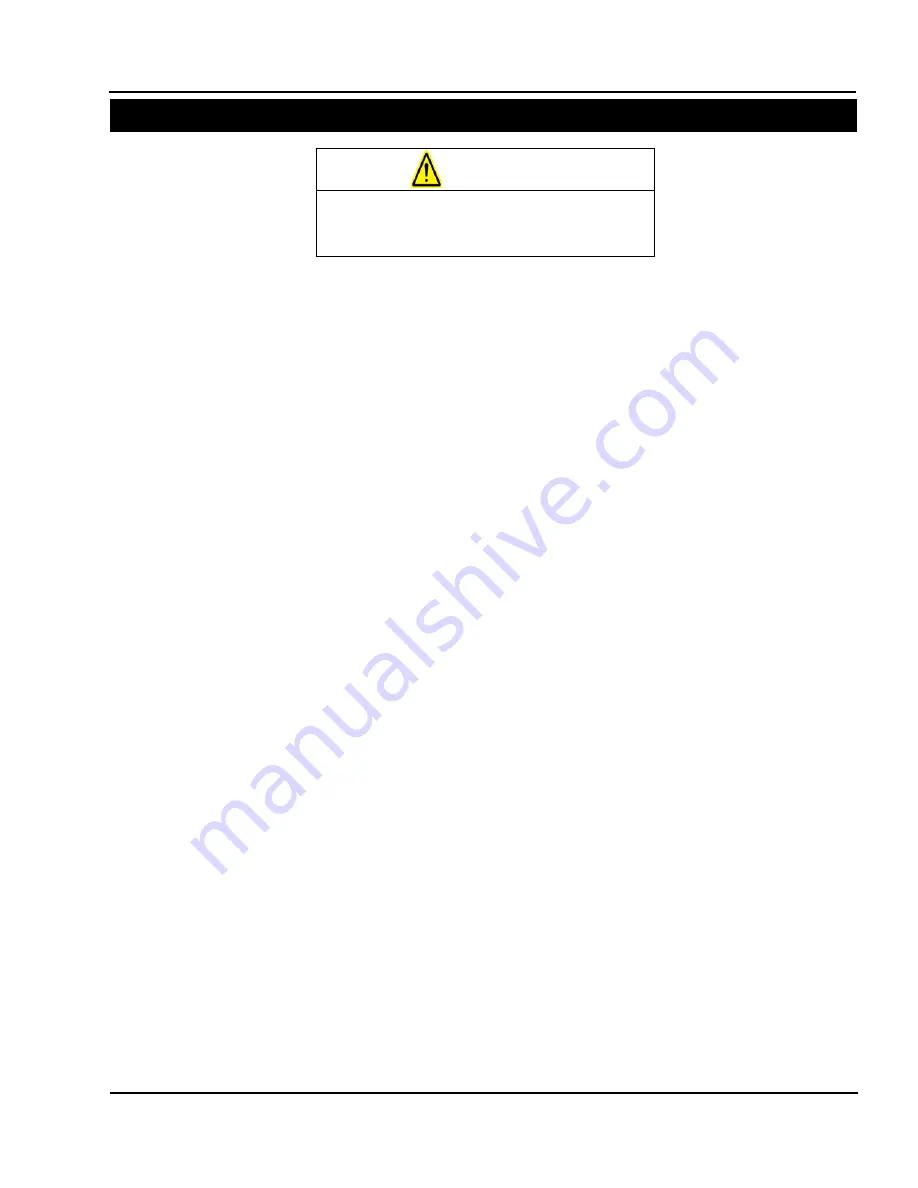
SX
™
Service and Maintenance Manual 2-1 960714-02B © 2007 I2407
SECTION 2 – MAINTENANCE AND ADJUSTMENTS
MAINTENANCE SCHEDULE
DAILY MAINTENANCE
•
Inspect the electric eye. Clean with a cotton
swab if dirty. Do not use any solvents or
cleaning solutions on the sensing portions of
the electric eye.
•
Clean any excess material from the drive
roller and platen roller on the film feed
assembly. Plastic compounds tend to build-
up on the rollers. Clean regularly with a soft,
lint-free cloth using a rubber platen roller
conditioner/cleaner or isopropyl alcohol.
•
Inspect Teflon tape on the seal wire and
replace if damaged or worn.
•
Inspect the anvil rubber on the pressure bar
assembly and replace if damaged or worn.
•
Inspect all electrical lines for any sign of wear
or damage. Replace any lines that appear
worn or unsafe.
•
If the Sharp SX
is equipped with a printer,
the printhead needs to be cleaned with a
soft, lint-free cloth and isopropyl alcohol. This
will be explained further on page 2-3 in the
section entitled “Cleaning the Printhead and
Film Feed Rollers.”
MONTHLY MAINTENANCE
•
Clean the foam element located on the
cooling fan on the rear of the machine with
water, wring out, and reinstall.
ANNUAL MAINTENANCE
•
Check all electrical connections.
•
Check entire machine for loose bolts or nuts.
•
Inspect all drive belts for excessive wear and
slack.
•
Grease the four pressure bar linear guide
bearings using lithium grease (JIS Type 2).*
•
Apply a light film of grease to the pressure
bar rack and pinion gearing using lithium
grease (JIS Type 2).*
*
Note: The recommended lubrication interval for
the linear guide bearings based on total travel is
approximately 500,000 cycles. Sharp Packaging
Systems suggests greasing the bearings at this
frequency or once a year, whichever comes first.
Both the linear guide bearings and the pressure bar
gear rack and pinion gear can be lubricated with
the same frequency.
Always remove electrical power from the
SX
prior to performing any maintenance
on the machine.
WARNING