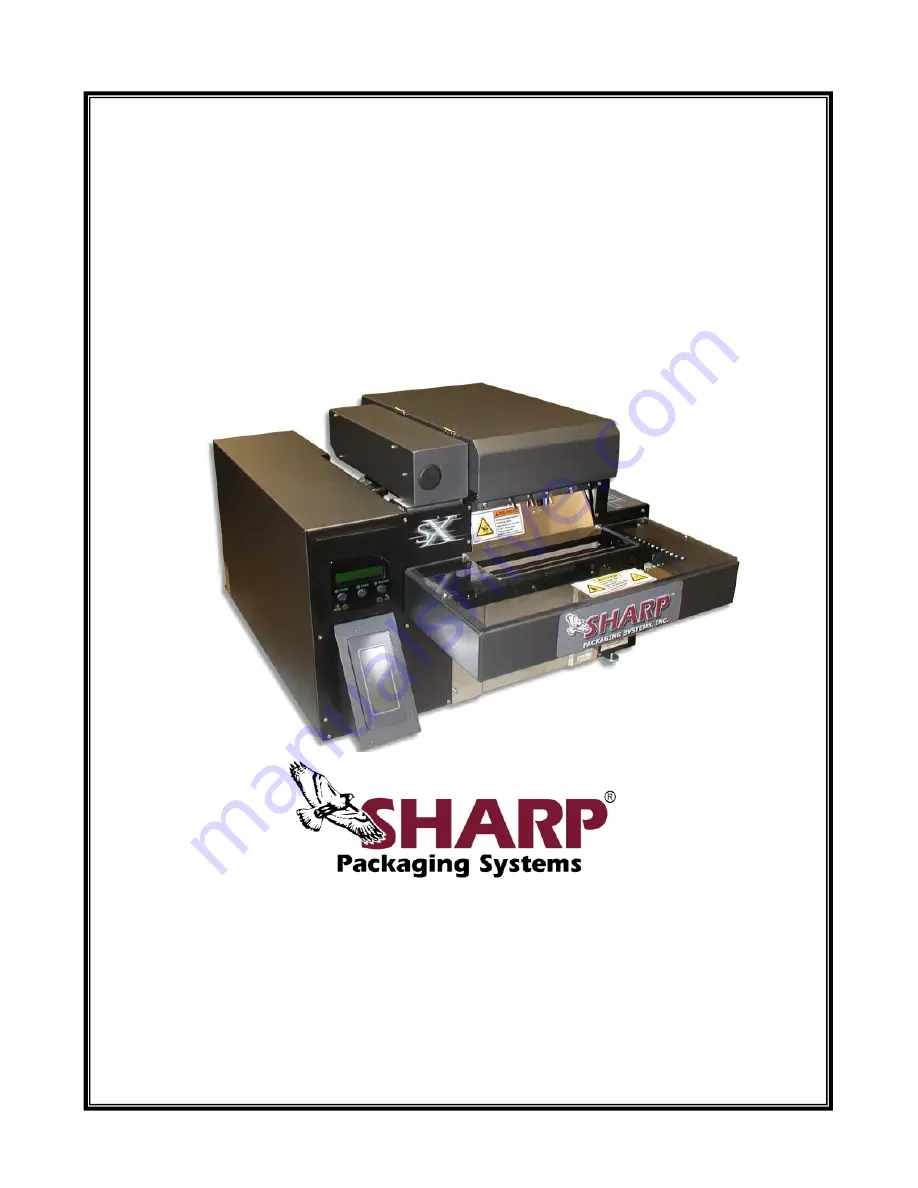
T
T
h
h
e
e
S
S
h
h
a
a
r
r
p
p
S
S
X
X
T
T
M
M
&
&
T
T
h
h
e
e
S
S
h
h
a
a
r
r
p
p
S
S
X
X
T
T
M
M
w
w
i
i
t
t
h
h
P
P
r
r
i
i
n
n
t
t
e
e
r
r
Service & Maintenance Manual
Models 1075, 1084, 1097, 1099, 1108, 1109, and 1121
Printed In USA 0924
PN: 960714-02B
Copyright © 2007
Parts:
(800) 634-6359 ext. 571
Service:
(800) 634-6359 ext. 572
www.sharppackaging.com