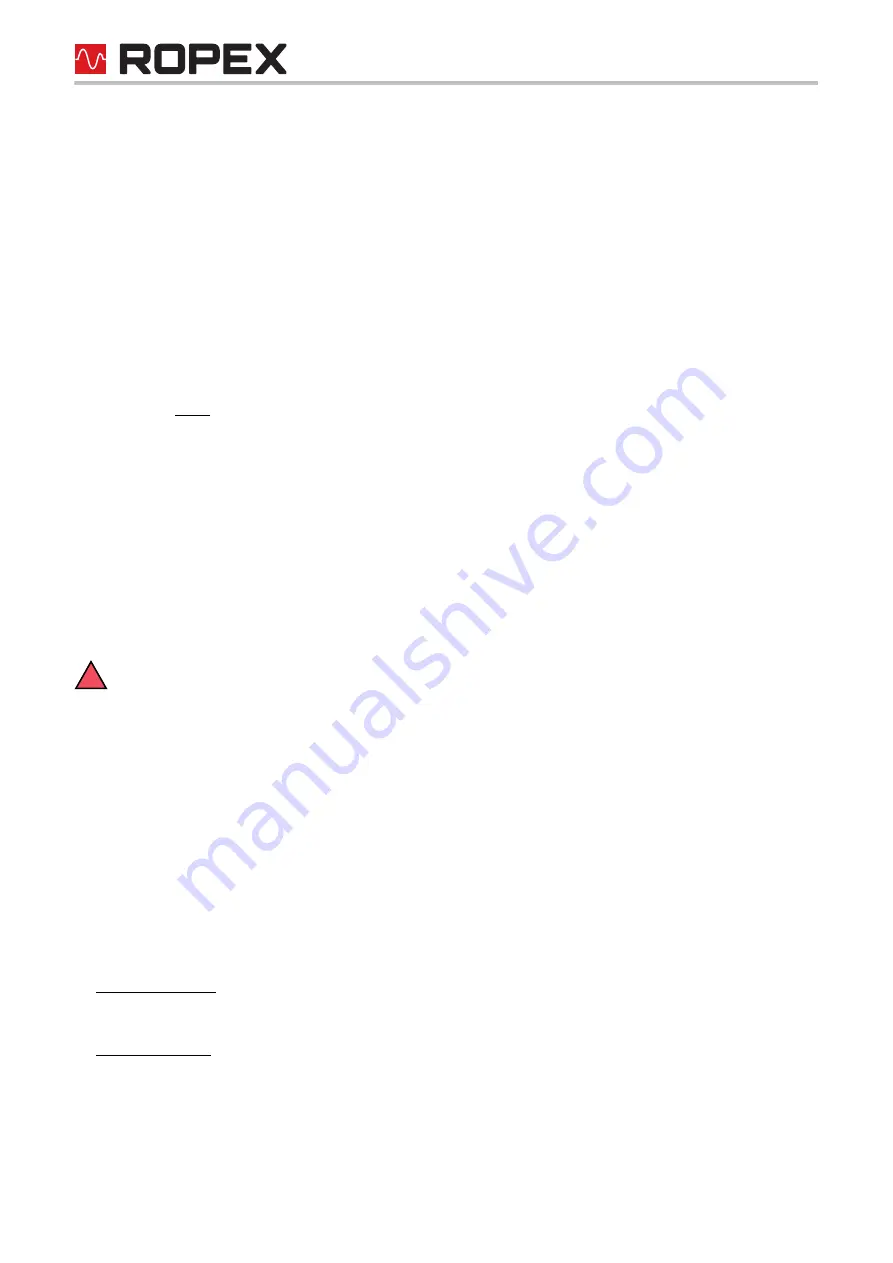
Device functions
Page 34
UPT-6006
Version 1
8.7.6
Expanded device diagnosis
The expanded device diagnosis uses the diagnosis channel of the PROFIBUS protocol to report possible error
statuses of the UPT-6006 to the PROFIBUS master. Text messages for every error status are stored in the GSD
file. The PROFIBUS master can automatically displayed them in case of a corresponding display possibility.
With the help of parameter no. 9, the expanded device diagnosis can be switched on or off. The expanded device
diagnosis is active in the standard setting.
Regardless of this parameter, the possibility remains of querying the device status over the user data.
DPV1 protocol expansion (alarm model):
Expanded device diagnosis is not available if the DPV1 protocol expansion (
section 8.8 "DPV1 protocol expan-
sions" on page 39) is used. The related DPV1 alarm model (
section 8.8.2 "DPV1 alarm model" on page 39)
must then be used. With parameter no. 9 of the GSD file, in this case the so-called DPV1 diagnosis alarm is
switched on or off.
If the previous expanded device diagnosis should continue to be used (e.g. for reasons of software compatibility),
a GSD version lower than v2.0 must be used. This automatically switches off the DPV1 function for the UPT-6006
in the PROFIBUS master.
8.7.7
Measurement impulse duration
The length of the measurement impulses generated by the controller can be set with parameter no. 10. For certain
applications, it can be necessary to lengthen the measurement impulse beyond the standard 1.7ms.
8.7.8
Data format
The format of the cyclically replaced process data (
section 8.4 "PROFIBUS protocol" on page 21) can be
changed. Depending on the type of PROFIBUS master used, it may be necessary to switch the high byte
(bits 15…8) and low byte (bits 7…0) against each other.
For Siemens controllers, the setting “Low/high byte (Motorola)” is recommended.
8.7.9
Error number format
The length of the error number in the cyclical data is set with this parameter. Selection is possible between 4-bit
and 10-bit (
section 8.4 "PROFIBUS protocol" on page 21). The “4-bit” setting generates 2-digit error numbers
in the range 1…13. The “10-bit” setting generates more detailed 3-digit error numbers (
section 8.19 "Error mes-
sages" on page 49).
8.7.10 Correction factor Co
The correction factor Co allows you to adapt the controller to the actual conditions in the machine (type of UPT
heating element, impulse transformer specification, length of connecting cables, cooling etc.).You can set the
required correction factor for the channel 0 with parameter no. 12. The correction factor can be set for each
channel individually. For the channels 1 to 7 use the parameters 29, 33, 37, 41, 45, 49 and 53.
Proceed as follows to determine the optimum correction factor Co:
1. Controller settings:
- Set temperature: 160…180 °C
- Sealing time:
0.20…0.30 s
2. Heating impulses (ST bit = 1):
Proceed as described in section 8.5.3 "Start (ST)" on page 26.
Slowly increase the correction factor, starting either with the lowest value (50%) or with the value recommended
in the ROPEX Application Report minus 25%, until the actual temperature at the end of the heating impulse cor-
responds to the set temperature.
!
Содержание CIRUS UPT-6006
Страница 62: ...Index Page 62 UPT 6006 Version 1 ...