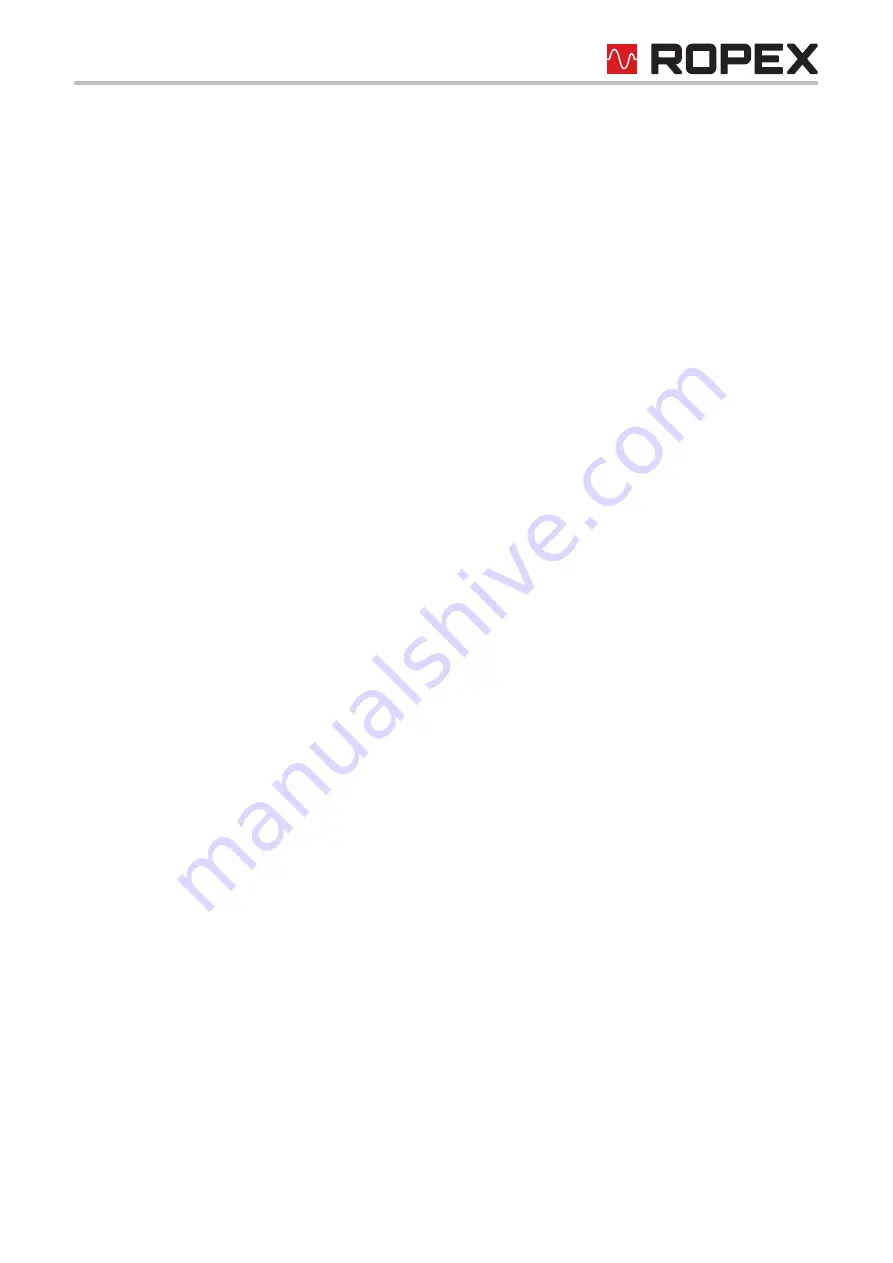
Device functions
Version 1
UPT-6006
Page 27
As long as the RS bit is set, no AUTOCAL and no START request are accepted. In the error diagnosis, only errors
no. 5 and 7 (201…203, 901, 913) are evaluated and output. In this status, no control of the power element takes
place and no measurement impulses are generated. As a result, there is also no more updating of the actual value.
The reset request is not processed until the RS bit is processed. The PROFIBUS communication is not interrupted
by resetting of the controller.
During activation of the RS bit, the actual value output goes to 0…3 °C (i.e. about 0 VDC) and the SA bit is active.
This can be evaluated as feedback by the higher-level controller (e.g. PLC).
Performance of the AUTOCAL function is not interrupted through activation of the RS bit.
After reset of the RS bit, the controller carries out an internal initialisation for about 500 ms. The next sealing pro-
cedure can only be started after that.
A fuse Kb possibly used for switching off the regulation circuit (
section 6.3 "Power supply" on page 10) must be
securely switched on no later than 200 ms after resetting of the RS bit . The switching and delay times of the fuse
must be observed. Switching on later results in an alarm message from the controller.
8.5.5
Measurement pause (MP)
When the MP bit is set, the controller no longer generates any measurement impulses. In the error diagnosis, only
errors no. 5 and 7 (201…203, 901, 913) are evaluated and output. Furthermore, the actual value is no longer
updated. The last value valid - before setting the MP bit - is output. After deletion of the MP bit, measurement
impulses are immediately generated again, all error messages are evaluated, and the actual value is updated.
The MP bit is effective only in measurement mode. The bits ST, RS and AC have priority.
It is suitable for applications in which the electrical connections of the heating element must be disconnected in
normal operations without an alarm being triggered (e.g. with sliding rail contacts).
In contrast to the RS bit (RESET), setting the MP bit does not delete any alarm messages. After deletion of the
MP bit, the controller is immediately active again; no initialisation phase is run through.
After the controller is switched on, the MP bit is not evaluated by the controller until the system check (incl. function
check of the heating circuit) has been successfully completed. This can take several 100 ms.
8.5.6
Master AUTOCAL (MA)
Setting of this control bit starts the calibration process, just as in section 8.5.2 "AUTOCAL autom. zeroing (AC)"
on page 25. But in addition, after successful performance of the Master AUTOCAL function, the heating element
resistance determined by the controller is stored as a reference value, e.g. after a heating element replacement.
This reference value is used in subsequent calibration processes (started with the AC bit) as a basis for calculating
the calibration value deviation. This can be used to evaluate ageing of the heating element.
Querying of the calibration value deviation takes place through acyclical read access.
8.5.7
Channel selection (CH0…CH2)
The CIRUS
®
temperature controller has separate memories for up to eight calibration data sets. A calibration data
set contains the values that the temperature controller determines during the AUTOCAL function. Saving of the
calibration data sets makes it possible to operate sealing tools in alternation without having to perform the
AUTOCAL function after each change. AUTOCAL has to be performed only when connecting a new heating ele-
ment.
As different calibration values, Autocal temperatures, correction factors and temperature coefficients are available
for this in the controller, the desired calibration data set 0…7 can be selected over the 3 bits CH0…CH2. The
channel can be switched at any time.
This function can be used, for example, in applications that require frequent change of the format. In such a case,
different tools can be replaced for the different formats. A channel that contains the corresponding calibration data
set can be assigned to each tool. When all tools have been calibrated with a uniquely assigned channel, the fol-
lowing changes can be performed by just selecting the corresponding channel again.
For applications that do not require a format change, the channel can stay at 0. As a result, the temperature con-
troller acts exactly like older models that do not yet support any different calibration data sets.
Содержание CIRUS UPT-6006
Страница 62: ...Index Page 62 UPT 6006 Version 1 ...