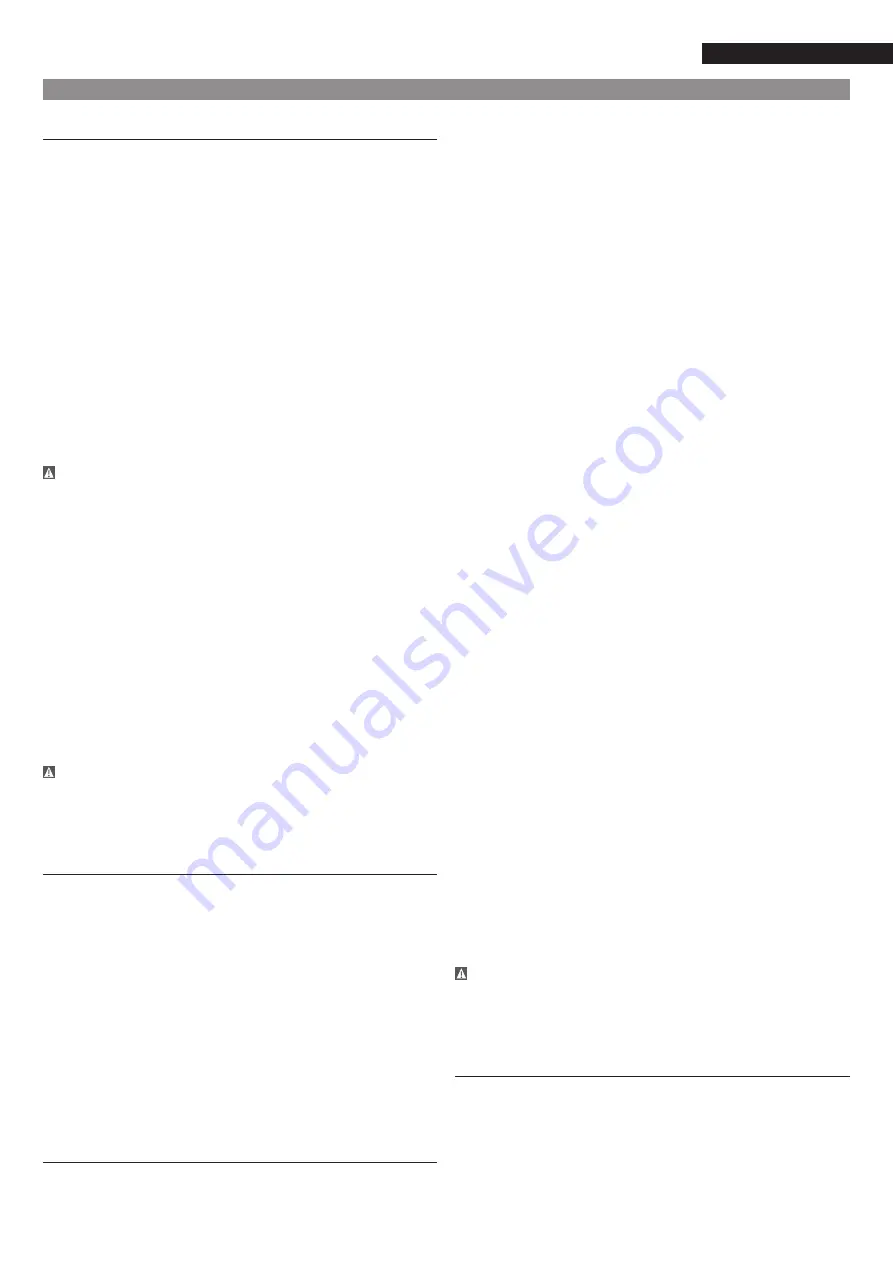
95
Maintenance
EN
5.1 STANDARD MAINTENANCE
In
order
to
ensure
the
unit's
maximum
effi-
ciency and reliability, it is recommended to stipula-
te a maintenance contract with your local support centre.
The contract includes regular inspections performed by the
service's experts, so that any malfunctions will be promptly
detected and corrected, without any serious consequences.
With a maintenance contract, our experienced technicians
will be able to ensure that the devices will last as long as
possible, and the system will be managed in the most ef-
fective manner, even in terms of costs. The air-conditioning
devices must be serviced by authorised professional techni-
cians, while routine checks can be carried out locally by spe-
cialised technicians.
See the EN 378-4 or ISO 5149 standards.
All the refrigerant filling, removal, and discharging opera-
tions must be performed by qualified personnel, using the
correct materials for the unit in question. Any inadequate
handling could result in fluid leaks or uncontrolled pressure
values.
Prior to performing any interventions upon the machine,
always make sure that the power supply is turned off. If a
cooling circuit is opened, it must be completely drained,
refilled, and tested to check for any leaks. Prior to perfor-
ming any operations upon a cooling circuit, the entire re-
frigerant charge must be drained from the unit using a
refrigerant recovery unit.
Simple preventive maintenance operations can ensure the
unit's excellent performance:
• improved heating and cooling performance
• reduced energy consumption
• prevention of accidental component functions
• prevention of major interventions, thus ensuring savings
in terms of time and costs
• protection of the environment
The units require five different levels of maintenance.
Any deviations or failure to observe these maintenance
criteria will nullify the unit's warranty conditions, thus
releasing the manufacturer of any responsibility.
5.1.1 Maintenance level 1
Simple procedures can be performed by the user on a
weekly basis:
• visually check for any traces of oil (indication of a refrige-
rant leak);
• clean the air heat exchanger;
• check for any protection devices that may have been re-
moved, and any doors or covers that may not have been
closed properly;
• check the unit alarm report while the unit is not in fun-
ction (refer to section "Control Panel");
• visually check for any signs of deterioration;
• check the charge on the level indicator;
• check that the difference in water temperature between
the heat exchanger's intake and delivery is correct.
5.1.2 Maintenance level 2
This level requires a specific know-how in the electrical,
hydronic, and mechanical fields.
This maintenance level can be performed monthly or yearly
according to the type of verification.
Under these conditions, it is recommended to perform the
following maintenance interventions.
Perform all the level 1 operations, and then perform the fol-
lowing:
Electrical checks
• Tighten the power circuit's electrical connections at least
once a year (see the table containing the tightening tor-
ques).
• If necessary, check and tighten all the connections for the
controls/commands (the table containing the tightening
torques).
• Dust and clean the inside of the control units, if necessary.
• Check the status of the contactors, switches, and capaci-
tors.
• Verify the presence and check the conditions of the elec-
trical protection devices.
• Check that all the electric heaters are functioning properly.
• Check that no water has penetrated into the control unit.
Mechanical checks
• Check the tightness of the fastening bolts of the fan co-
lumn, the fan, the compressor, and the control unit.
Water circuit checks
• Always use caution when working on the water circuit, and
take care to avoid damaging the adjacent capacitor.
• Check the water connections.
• Check whether the expansion tank shows any signs of
excessive corrosion or gas leaks, and replace it if necessa-
ry.
• Drain the impurities from the water circuit.
• Clean the impurities from the water filter.
• Check the fixed speed pump's bearing after 17,500 hours
of operation with water, and the seal of the mechanical
pump after 15,000 hours. •
Check the operation of the
low water flow safety device.
• Check the status of the pipes' thermal insulation.
• Check the concentration of the anti-freeze solution (ethyle-
ne glycol or propylene glycol).
Cooling circuit
• Thoroughly clean the air heat exchangers with a low pres-
sure jet and a biodegradable detergent.
• Check the unit's operating parameters and compare them
with the previous values.
• Perform an oil contamination test. • Change the oil if
necessary.
• Check the operation of the high-pressure switch. Replace
it if faulty.
• Check the cleanliness of the dehydration filter. Replace it if
necessary.
• Keep and maintain a maintenance sheet for each unit.
All these operations require the user to strictly follow the
safety measures: personal protective equipment, com-
pliance with all sector regulations, compliance with all
applicable local regulations and use of common sense.
5.1.3 Maintenance level 3
Maintenance at this level requires specific skills, permissions,
instruments and know-how, and the relative operations may
only be carried out by the manufacturer, its representatives,
or other authorised agents. These maintenance operations
involve the following interventions, for example:
• the replacement of major components (compressor, eva-
porator, etc.);
• any interventions upon the cooling circuit (handling of
the refrigerant);