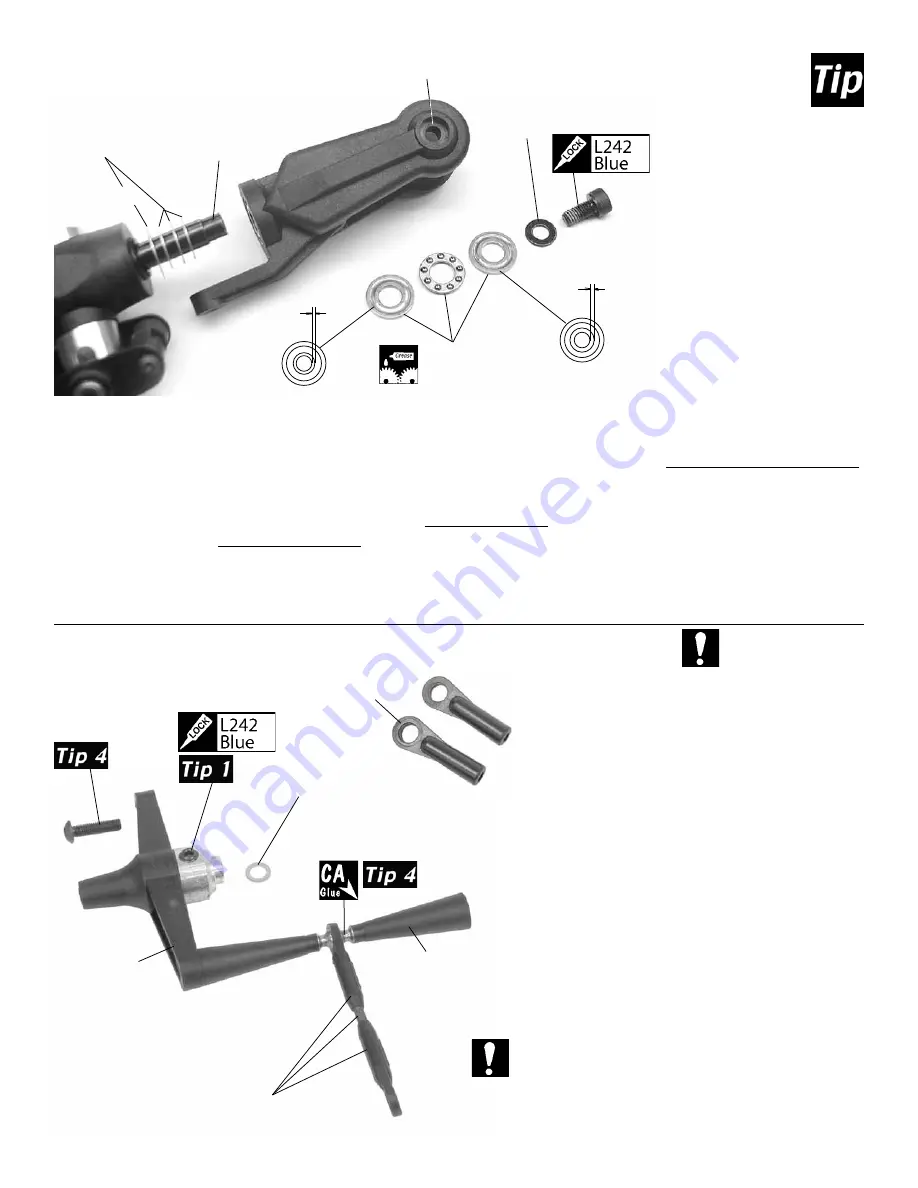
6
Remove one damper and press the feathering spindle to seat the ball near the center of the rotor hub. Reposition the rubber
damper in the rotor hub and slide one large shim against the damper followed by three regular stiffness shims and one blade
grip assembly onto the feathering spindle. The bell mixer and pitch arm of the blade grip is mounted on the leading edge
when as the head rotates clockwise. Install the M7x15 thrust bearing and lubricate the bearings with light grease. Looking at
the two steel races of the thrust bearing, note that the innermost surfaces have different widths because the inside diameters
are different. Slide the first larger diameter steel washer (
thin race, larger ID) followed by the greased ball race, followed by
the second steel washer (thick race, smaller ID). Remove any grease that may have transfered to the threads using a cotton
swab dipped in alcohol. Apply L242 Blue threadlock to the inside threads on the feathering spindle using a pin and install
the M5x10 socket cap screw with washer. Do not overtighten this bolt because it will flair the end of the spindle making
removal of the blade grip nearly impossible. Repeat for the other blade grip.
Step 7 Feathering Spindle & Blade Grip
#HW6182
Stiffness
Shims
#HW6180A
Feathering
Spindle
Large
#HW6180A M5x10
Socket Screw & M5
Flat Washer
thin
race
(inside)
larger ID
thick race
(outside)
smaller ID
#CNBB715T
M7x15 Thrust
Ball Bearing
Hobby Grease
Generally, grease
is needed for thrust
bearings and the tail
rotor gears. A light
Lithium or Silicon
grease should be
used, commonly
found at hobbyshops
for RC cars.
Step 8 Flybar Control Yoke
Pushrod A is already assembled but check that the length is
actually 47mm (center to center). As the pushrods are build
and installed they should be checked for tightness. Press
one ball link onto each double studded steel ball, making
sure that pressure is applied from the side of the ball link
with circle mark. While holding one flybar control arm, ap
-
ply a small amount of slow cyanoacrylate glue and thread
one end of the double studded steel ball into each standoff.
When it becomes difficult to turn with fingers, apply slow
CA to the threads and start screwing in the tapered control
arm stand-off on the other end of the ball.
M3x12 Button
Cap Screw
#HI3176C
Flybar Con-
trol Arm
#HW3176C Double
Studded Steel Ball
Pushrod A 47mm
(center to center)
#HI6145 Ball Link x 2
#HW6192 25mm Pushrod x 2
#CNLR1006
M4x6 Micro Washer
M4x5 Set
Screw
#HI3176C
Tapered
Standoff
Ball Link Direction
All ball links are molded to be installed in only one
direction. Look carefully at the hole for the ball,
one side is clean while the other side has a circular
mark, 1mm larger than the hole. The marked side
presses over the steel control balls.
Circle Mark
presses over
steel ball.
Round Recess
on Top
A correctly installed the ball link should rotate with
some resistance when the metal pushrod is rotated in
your fingers. If the ball link to too tight the preferred
solution is to purchase Century’s ball link sizing tool
[CN2055] to custom fit each ball link to its steel ball.