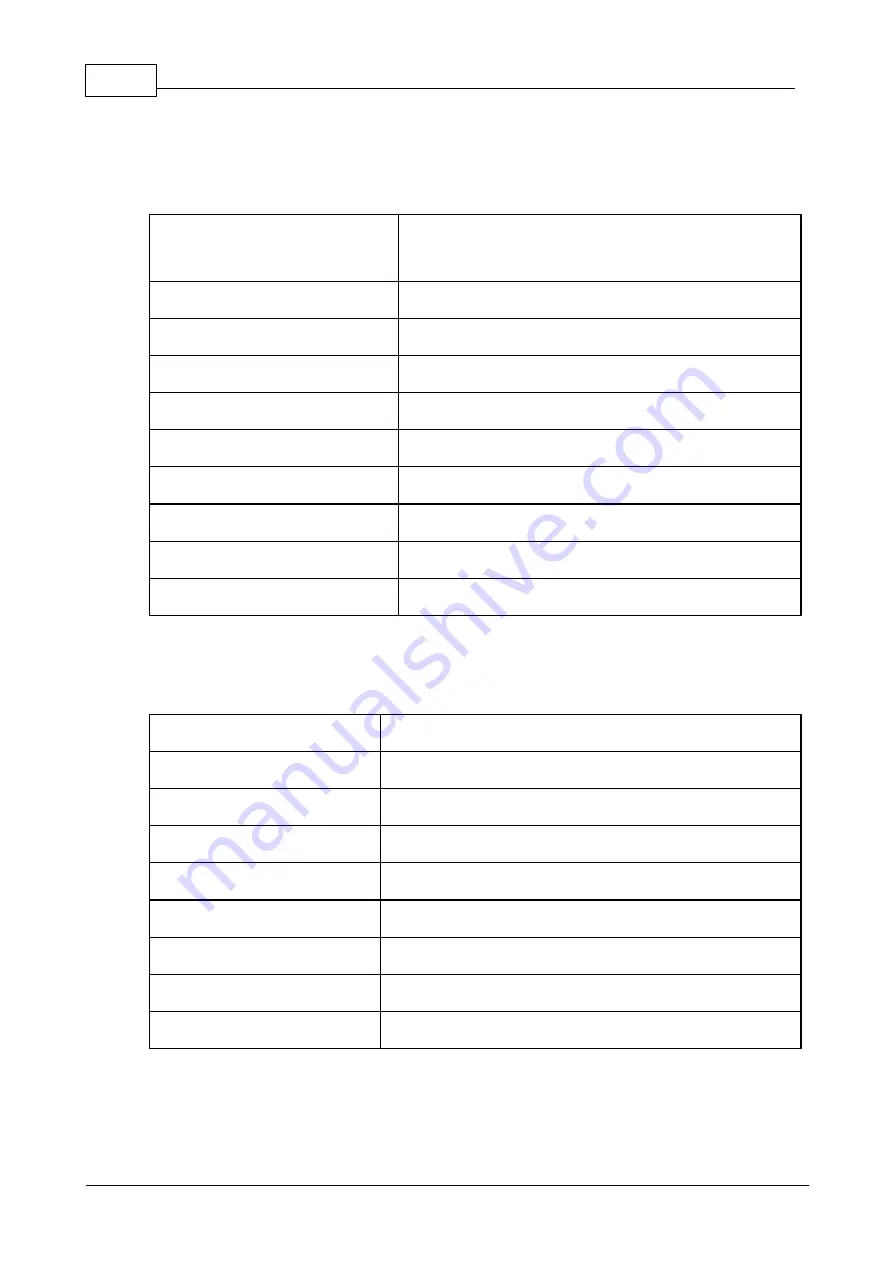
66
Liquidus Tracker
5
Additional information
5.1
Specifications
5.1.1
System specifications
Accuracy
±(0.3 + 0.005 x TM) °C
(where TM is the magnitude of the temperature).
Pump speed
0.1 - 220 rpm
Pump resolution
0.1 rpm
Storage temperature
-10 °C to +50 °C
Storage humidity
5% to 95% relative humidity non-condensing
Operating environment
For indoor use only
Operating temperature
+5 °C to +40 °C
Operating humidity
5% to 90% relative humidity non-condensing
Altitude
up to 2000 m
Pollution degree
Pollution degree 2 (BS EN61010-1)
5.1.2
Controller specifications
PC interface to DeltaT
USB
Dimensions
240 mm high x 235 mm wide x 185 mm deep
Weight
2.8 kg approx.
Display
2 x 16 LCD with backlight
Keypad
3 key keypad
Number of profiles
10
Steps per profile
32
Number of stored runs
1
Power failure backup
1 minute
Содержание Kryo360-1.7
Страница 1: ...Liquidus Tracker Operator s Guide...
Страница 5: ...Introduction Section I...
Страница 20: ......
Страница 21: ...Installing the system Section II...
Страница 29: ...25 Installing the system...
Страница 33: ...29 Installing the system 10 Connect the power supply cables to the pumps and chamber...
Страница 35: ...Operating the system Section III...
Страница 65: ...Routine maintenance and troubleshooting Section IV...
Страница 68: ......
Страница 69: ...Additional information Section V...
Страница 76: ......
Страница 80: ...MA101894 Issue 2 Liquidus Tracker Operator s Guide...