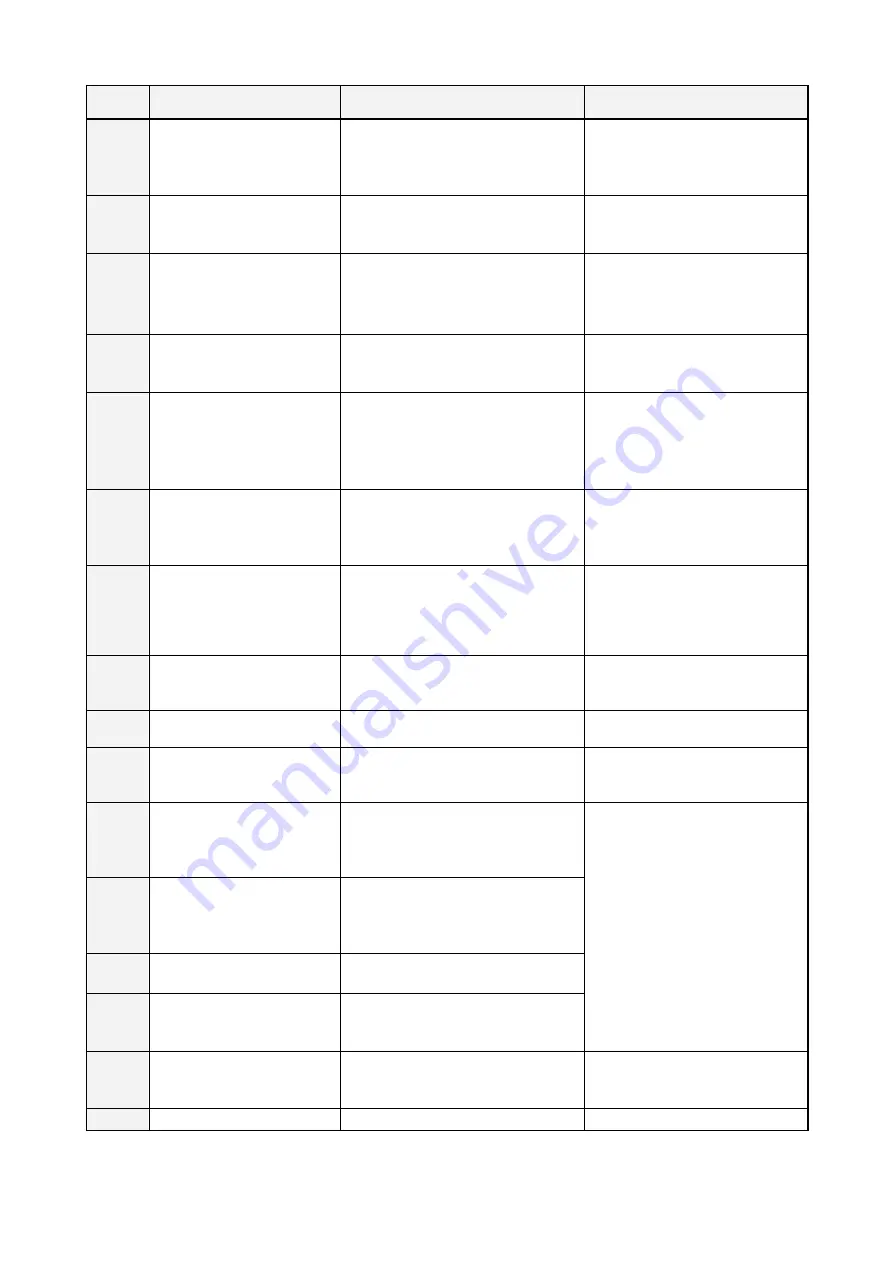
17-6
Error
code
Message
Probable Cause
Remedy
E1210
Overlap is not available
Overlap at re-start will bring the robot
to the preceding teaching point.
Move the robot back to the
preceding teaching point in trace
operation before re-starting
operation.
E1220
Overlap failed
The robot reached the preceding
teaching point during overlap
operation.
Turn off the power and then newly
turn it on.
E1230
Harmonic data Error
occurred
The specified harmonic coordinate
system has not defined. The
specified mechanism is inadequate for
the structure.
Check the settings of the harmonic
coordinate system and the
mechanism.
E1240
The mechanism overlaps
An axis in the mechanism of the
program executed by the PARACALL
command is duplicated.
Check the mechanism structure of
the program.
E1250
Weld slope command error
“D” or “Next” is used as argument in a
program with no mechanism.
Value of an argument to which
variable (GR or LR) is assigned, is
either “0” or negative number.
Check and modify the program.
E1260
Mechanism is unmatched
Processing is not possible as the
mechanism of the running program
and mechanism specified in the
variable do not match.
Re-set the mechanism either of the
running program or of the variable.
Or use another variable.
E1270
TOOL No. Error
The specified tool number is not
correct.
For example, a tool number for the
slave robot is selected in the program
for the master robot.
Check the program.
E1280
No mechanism specified by
the program
The mechanism number in the running
program is not in the range of
mechanisms of this system.
Check and modify the program
and system settings.
E1290
"Start permission input" was
turned off
The "Start permission input" goes off
while running the program.
Restart the program when the
"Start permission input" turns ON.
E1300
"Start permission input" is
turned off
The "Start permission input" was in the
OFF state when the program was
started.
Start the program when the "Start
permission input" turns ON.
E1310
Ext-Axis range monitoring
Error
The robot attempted to enter the area
specified by the "Ext-Axis range
monitor".
(The monitor input is in the ON state.)
E1311
Ext-Axis range monitoring
Error (Slave)
The slave robot attempted to enter the
area specified by the "Ext-Axis range
monitor".
(The monitor input is in the ON state.)
E1320
AND condition monitoring
Error
All the AND conditions are satisfied.
(The monitor input is in the ON state.)
E1321
AND condition monitoring
Error (Slave)
The AND conditions of the slave robot
are satisfied.
(The monitor input is in the ON state.)
Re-start is enabled when the
"Monitor input" goes OFF.
E1330
Cannot update variable
value.
The command that assigns a value to
a position variable was executed in a
protected program.
Change the protect level of the
target program to "Allow Point
Change Only".
E1900
(User defined message)
HOLD command is executed.