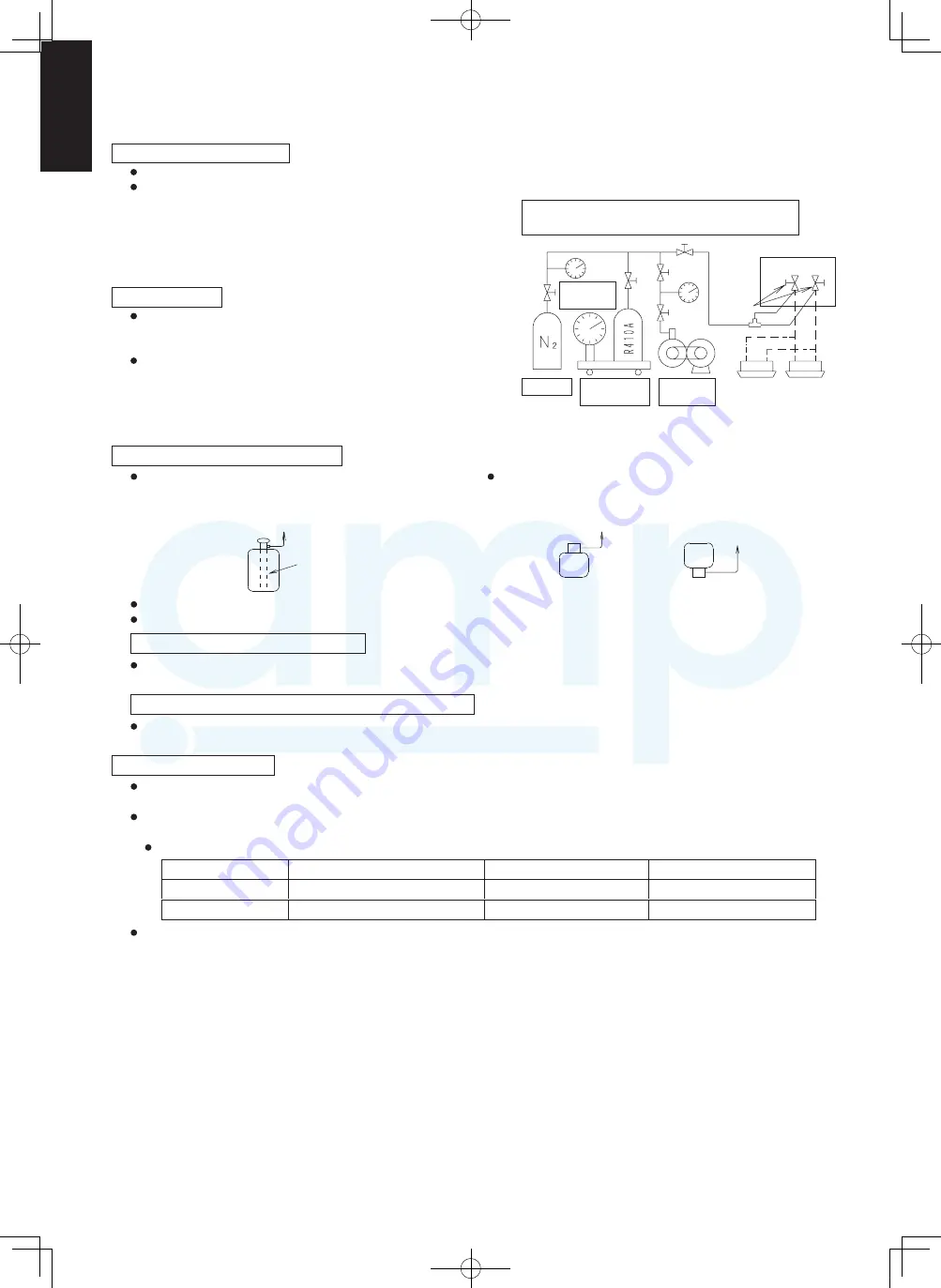
1-98
1
1
Ensure to fi ll only with liquid refrigerant when refi lling.
If gas refrigerant is fi lled, the refrigerant composition will
not be balanced and will cause abnormal operation.
Cylinder with
a siphon tube
Liquid refrigerant
Siphon tube
Cylinder
Cylinder
Gas refrigerant
Possible
(For refi lling due to a leak)
Not possible
1-14. VACUUM PURGING
1-15. REGARDING REFRIGERANT FILLING
Precautions during refrigerant fi lling
Charging with refrigerant
If using cylinders as shown in the bottom left diagram; without
a siphon tube inside, turn it upside down and use it.
(It is recommended to use the manifold with the side glass.)
Use tools that are designed specifi cally for R410A, for pressure resistance and to prevent mixing impurities.
Fill the refrigerant from the 3-way valve’s service port on the liquid-side.
For fi lling and replacing all refrigerant
For refi lling refrigerant, fi rst collect all residual refrigerant and after vacuum dehydration using the vacuum pump. Refi ll the
refrigerant according to the prescribed amount stated on the placard affi xed to this unit.
Precautions after the pipes’ connection have completed
Ensure to open the 3-way valve after completing the piping installation, leak test and vacuuming. If it is closed during operation,
it can lead to compressor failure.
At the time of shipment from the factory, this unit is charged with enough refrigerant for an equivalent pipe length of 30m.
If the equivalent pipe length used will be 30m or less, no additional charging will be necessary.
If the equivalent pipe length will be between 30 and 120m, charge with additional refrigerant according to the equivalent length
given in the table below.
For standard type
Pump down operation
Please refer to the service manual for pump down method.
Liquid refrigerant
Model name
Add. gas amount
Equivalent length
Minimum length
m
5
m
0
2
1
m
/
g
0
5
A
8
E
2
E
P
0
0
2
-
U
m
5
m
0
2
1
m
/
g
0
8
A
8
E
2
E
P
0
5
2
-
U
Keep 3-way valve fully closed and pressurize through 3-way valve service port.
Do not pressurize to the default value at once. Pressurize gradually.
1 Pressurize to 0.5MPa (5k
g
f/cm²G) and then leave it for 5 minutes
to ensure that the pressure does not drop.
2 Pressurize to 1.5MPa (15k
g
f/cm²G) and leave it for 5 minutes
to ensure that the pressure does not drop.
3 For the test, pressurize to 4.15MPa and leave it for about 1 day
to ensure that the pressure does not drop.
Leak Tightness Test Method
Vacuum Purging
Use a vacuum pump (with back-fl ow prevention device) to vacuum
through the 3-way valve service port to achieve the pressure below
-101kPa (5 Toor).
Air and moisture remaining in the refrigerant system due to poor
vacuum drying can cause performance decrement and malfunction
of the compressor.
Outdoor unit
3-way
valve
Indoor unit
Use nitrogen gas for the leak tightness test.
Using fl ammable gas can cause an explosion.
Pressure
meter
Nitrogen
Refrigerant
meter
Vacuum
pump
Test Run Procedure
If there are duplicated system addresses, or if the settings for the Nos. of the indoor units are not consistent, an alarm will
occur and the system will not start.
Switch the power supply ON both indoor and outdoor unit.
Short-circuit CHK pin on the outdoor main PCB.
Do not remove CHK pin until test run is completed.
Removing CHK pin stops test run.
Short-circuit RUN pin on the outdoor main PCB for
one second or longer.
Factory setting is cooling operation mode and
cooling operation test run starts.
If heating operation starts, short-circuit both right
side and centre of the MODE pin (centre and COOL)
continuously.
Ensure to conduct a test run. In addition, be sure
to run the cooling operation test run for at least 20
minutes before starting the heating operation test
run.
To conduct heating operation test run, short-circuit
left side and centre of the MODE pin (centre and
HEAT) continuously.
Removing CHK pin’s and MODE pin's short-circuit
stops test run.
For the test run using remote control unit, please
see installation manual included with the remote
control unit.
Check Before Test Run
Content check
Power supply cable
Indoor/outdoor
connection wire
Earth wire
Is the wire set up and connected as described in the instructions? Check for any phase sequence.
Are the wire connection’s screws loose?
Is the open and close device / leakage breaker installed?
Is the power supply cable’s thickness and length appropriately measured as described in the instructions?
Is it earthed (grounded)?
Check that the insulation resistant value is more than 1 MΩ.
Use the 500 V mega-testers to measure the insulation.
Do not use the mega-tester for any other circuit except for voltage of 220-240V or 380-415V.
Are the wire connections for the indoor/outdoor units connected as described in the instructions? Are there
any looped wires?
Was the “N-phase” surely connected when connecting the power supply wire on the three-phase model?
If N-phase is not connected, only the fan may repeat turning ON/OFF without the compressor operating.
In that case, check if there is any problem with N-phase connection.
Refrigerant pipe
Is the piping installed as described in the instructions?
Are the pipes sizes appropriate?
Does the pipe’s length adhere to the specifi cations?
Is the branch pipe slant being appropriately done as described in the instructions?
Was vacuum removal suffi ciently carried out?
Was the leak tightness test carried out with nitrogen gas? Use the testing pressure of 4.15 MPa.
Is the piping insulation material appropriately installed? (Insulation material is necessary for both gas and
liquid piping.)
Is the 3-way valve for the liquid side and gas side open?
Always be sure to use a properly insulated tool to operate the short-circuit pin on the circuit board. (Do not use your fi nger.)
Never switch the power supply ON until the installation has completed.
Supply electrical current through all indoor units and check the voltage.
Supply electrical current through all the outdoor units and check each inter-phase voltage.
Before the test run, ensure to check that the 3-way valve is open. Operating while the valve is closed causes the compressor
to fail.
1-16. PRECAUTIONS REGARDING TEST RUN
RUN pin
MODE pin
*MODE pin: factory setting is cooling
operation mode.
Outdoor main PCB
CHK pin
SM830252-01_欧州_Single_8・10HP_TD_SM.indb 98
16/10/14 13:58:14
AMP Air Conditioning
www.ampair.co.uk | [email protected]